1.1技术研发理念气旋浮含油污水复合处理技术并非将常规气浮分离设备与水力旋流器相对独立地串联组合,也不是在常规水力旋流器单体入口污水中注气或在旋流器腔体上打孔注气,而是基于对湍流场和离心场内微气泡与油滴颗粒碰撞、黏附和分离过程全新认识的结果。该技术在常规气浮分离设备的设计基础上,将分离区的表面水力负荷率由2~7m3(m2·h)提高到20~40m3(m2·h),利用适当的湍流作用促进油滴与微气泡之间碰撞黏附形成“微气泡-油滴黏附体”的几率,同时利用低强度旋转离心力场(弱旋流)加速“微气泡-油滴黏附体”的分离,以此来有效提高设备的分离性能,使最初的大容积、低表面水力负荷气浮分离池型逐渐向集成、紧凑型立式结构方向发展,更能满足陆上各类已建装置区以及海洋石油平台等环境空间受限场合后期增配相关处理设备的需要。
以美国Schlumberger公司的气旋浮装置(第一代产品为EpconCFU,第二代产品为EpconDualCFU)为例,该公司声称设备分离区的水力停留时间最低可至30s,有效容积仅2m3左右的设备处理量可达250m3h;当入口含油浓度低于100mgL且原油密度较小时,单级CFU运行可使出水口含油浓度低于20mgL,两级CFU串联运行可使出水口含油浓度低至10mgL。截止到2009年10月,EpconCFU共在欧美近40个海上油田的采出水处理流程中得到安装使用,中国海油西江(XJ)30-2油田于2008年第三季度耗资800多万美元引进了总处理量为3600m3h的EpconCFU。但由于技术保密等方面的原因,国内目前很难从公开的科技文献查阅渠道获取国外各种气旋浮装置的技术研发细节,只能从一些公开的产品样本和现场使用性能描述大致了解其研究动向和技术发展水平,导致迄今仍然缺乏大处理量自主品牌的工业化产品。另一方面,国内外炼油企业一直未能对该技术予以必要关注,致使迄今尚没有在该领域相关的工程应用案例。具体联系污水宝或参见http://www.dowater.com更多相关技术文档。
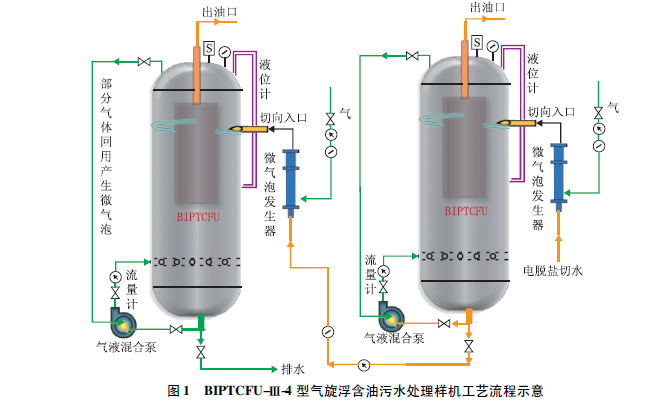
1.2工艺流程与工作原理北京石油化工学院多相流高效分离技术与设备研究所自2005年以来在国内率先关注并着手自主研究气旋浮含油污水复合处理技术,在推出BIPTCFU-Ⅰ型、BIPTCFU-Ⅱ型可视化样机的基础上,自主研发的BIPTCFU-Ⅲ-4型气旋浮含油污水处理样机在中国石化中原油田、中国海油秦皇岛(QHD)32-6油田和流花(LH)11-1油田等地成功进行了现场试验,且在水力停留时间、除油率等性能指标方面位居国内前列。图1为BIPTCFU-Ⅲ-4型气旋浮含油污水处理样机的工艺流程示意。样机主要包括微气泡发生器、气液混合泵、气旋浮罐等;采用撬装模块化设计,总体上采用两级CFU串联且各级可相对独立运行。核心设备气旋浮罐主要由立式压力容器罐体、内部稳流筒、污水切向入口、顶部排气口、顶部排油口、底部排水口等组成,有效容积为0.17m3,内径为Ф400mm,高度为1675mm。样机的设计处理量为4m3h,设计水力停留时间为2.5min,旋流强度为35g,设计处理量下的表面水力负荷率为32.65m3(m2·h)。
工作过程中,首先利用微气泡发生器向待处理含油污水中混入大量微气泡。微气泡与污水中的分散相油颗粒在入口管路内进行一定程度的碰撞黏附后,从罐体上部切向进入气旋浮罐内的旋流区。在该区域内一方面利用中低湍流作用促进油滴与微气泡的碰撞黏附,另一方面利用弱旋流促进轻质油相和微气泡向罐中心运移,该过程称为“一次气浮作用”。浮升到上部液面的“油-气泡-水”多相混合物(或称“富油相排出物”)自罐顶部出油口依靠压力排出,处理后的水从罐底部排出。为进一步改善气浮分离效果,将部分处理后的排出水回流,利用气液混合泵抽吸罐内顶部气相空间的气体,产生带有大量微气泡的回流水并经罐内中下部的布气中排均匀分布,产生“二次气浮作用”。总的来看,含油污水相当于在气旋浮罐内进行了一次旋流分离与两次气浮分离,因此除油率较常规旋流分离设备和常规气浮分离设备有较大幅度的提升。