申请日2016.02.19
公开(公告)日2016.07.13
IPC分类号C02F1/78; C02F9/04; B01J23/889; B01J29/48; B01J29/78
摘要
本发明实施例公开了一种臭氧催化氧化塔,包括氧化塔本体、臭氧发生器、循环泵和尾气破坏装置;氧化塔本体包括第一微孔曝气盘、第二微孔曝气盘、催化剂层、进水口、出水口、至少一个氧化剂加药口、排气口、循环进水口和循环出水口;第一微孔曝气盘位于氧化塔本体底部;第二微孔曝气盘位于第一微孔曝气盘上方;催化剂层位于第二微孔曝气盘上方;在第一微孔曝气盘和第二微孔曝气盘之间的氧化塔本体侧壁上由下至上依次设置有进水口和循环进水口;在催化剂层上方的塔体侧壁上由下至上依次设置有循环出水口和出水口;在进水口和循环出水口之间的氧化塔本体侧壁上设置有至少一个氧化剂加药口。该氧化塔可缩短臭氧在塔内的停留时间,提高臭氧利用率。
摘要附图
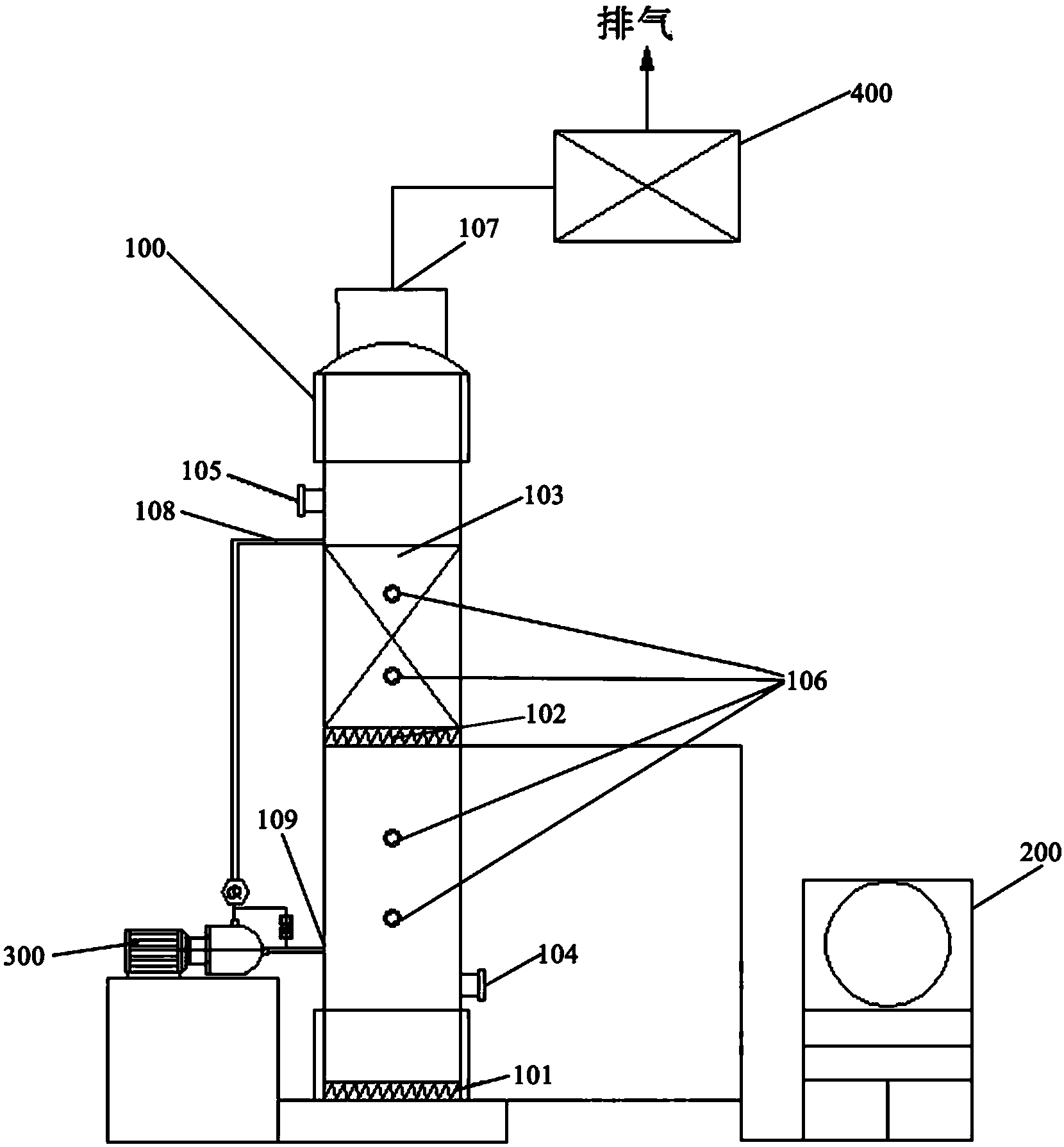
权利要求书
1.一种臭氧催化氧化塔,其特征在于,该氧化塔包括氧化塔本体、臭氧发生器、循环泵和尾气破坏装置;
所述氧化塔本体包括第一微孔曝气盘、第二微孔曝气盘、催化剂层、进水口、出水口、至少一个氧化剂加药口、排气口、循环进水口和循环出水口;
第一微孔曝气盘位于氧化塔本体底部;第二微孔曝气盘位于第一微孔曝气盘上方;催化剂层位于第二微孔曝气盘上方;第一微孔曝气盘和第二微孔曝气盘分别通过管路与臭氧发生器相连通;
在第一微孔曝气盘和第二微孔曝气盘之间的氧化塔本体侧壁上由下至上依次设置有进水口和循环进水口;在催化剂层上方的塔体侧壁上由下至上依次设置有循环出水口和出水口;在进水口和循环出水口之间的氧化塔本体侧壁上设置有至少一个氧化剂加药口;在氧化塔本体顶部设置有排气口,排气口通过管路与尾气破坏装置相连通;循环泵的进水端通过管路与循环出水口相连通,循环泵的出水端通过管路与循环进水口相连通。
2.如权利要求1所述的臭氧催化氧化塔,其特征在于,所述第二微孔曝气盘位于第一微孔曝气盘到出水口高度的1/2处。
3.如权利要求1所述的臭氧催化氧化塔,其特征在于,在进水口和循环出水口之间的氧化塔本体侧壁上设置有2个氧化剂加药口,优选为4个氧化剂加药口。
4.一种处理煤气化废水的方法,其特征在于,包括以下步骤:
将煤气化废水的pH值调至4~10,优选为6~9,之后进行混凝沉淀处理,将经混凝沉淀处理获得的上清液的pH值调至7~9后,将其输送至如权利要求1至3所述的臭氧催化氧化塔内进行臭氧催化氧化处理,并向臭氧催化氧化塔内投加氧化剂;同时进行内循环;上清液在臭氧催化氧化塔内的停留时间为10~60分钟;臭氧催化氧化塔中的催化剂为Poten-SOT型臭氧氧化催化剂;臭氧和氧化剂在所述氧化塔内的上清液中的投加量分别为50~350mg/L和50~300mg/L;
所述Poten-SOT型臭氧氧化催化剂由以下步骤制得:
将臭氧氧化催化剂载体进行预处理;所述预处理为先将臭氧氧化催化剂载体进行至少一次水洗,再将其浸泡在酸溶液中1~48h,然后洗涤至中性,最后干燥处理;
将预处理后的臭氧氧化催化剂载体进行至少一次浸渍处理,所述浸渍处理为将预处理后的臭氧氧化催化剂载体浸泡在浸渍溶液中,20~100℃浸泡6~48h,之后干燥处理;所述浸渍溶液为含有锰、镍、铁、铈、钴和铜中至少3种金属元素的硝酸盐、硫酸盐、醋酸盐或氯化物的混合溶液;所述至少3种金属元素在浸渍溶液中的浓度分别为0.01~1.00mol/L;
将浸渍后的臭氧氧化催化剂载体进行焙烧处理。
5.如权利要求4所述的方法,其特征在于,所述臭氧氧化催化剂载体选自颗粒状多孔陶瓷、颗粒状活性氧化铝、颗粒状分子筛、煤基柱状活性炭、颗粒状果壳活性炭或颗粒状多硅斜发沸石,并且其粒径为3~6mm,比表面积≥250m2/g,抗压强度>100N,堆积密度>0.17g/mL。
6.如权利要求5所述的工艺方法,其特征在于,所述浸渍溶液为锰、镍、铁、铈、钴和铜中6种金属元素的硝酸盐、硫酸盐、醋酸盐或氯化物的混合溶液,其中,锰、镍、铁、铈、钴和铜元素的物质的量之比为(1~50):(1~50):(1~50):(1~50):(1~30):(1~30),并且锰、镍、铁、铈、钴和铜元素在浸渍溶液中的浓度分别为0.01~0.50mol/L。
7.如权利要求4所述的方法,其特征在于,所述预处理为先将臭氧氧化催化剂载体进行至少一次水洗,再将其浸泡在0.01~1.00mol/L的硝酸溶液中10~30小时,优选地,0.05~0.15mol/L的硝酸溶液中10~24小时,然后洗涤至中性,最后干燥处理。
8.如权利要求4所述的方法,其特征在于,所述混凝沉淀处理为先向混凝沉淀池中加入无机混凝剂,以100~300转/分的转速搅拌0.5~3.0分钟,再向混凝沉淀池中加入有机絮凝剂,以100~300转/分的转速搅拌0.5~3.0分钟,之后调节转速至30~100转/分,搅拌10~30分钟,最后静止沉淀。
9.如权利要求8所述的方法,其特征在于,所述无机混凝剂为聚合氯化铝、聚合硫酸铁、聚合氯化铝铁、聚合硫酸铝、硫酸铝中的至少一种;所述有机絮凝剂为阳离子聚丙烯酰胺、阴离子聚丙烯酰胺、部分水解的聚丙烯酰胺中的至少一种;所述无机混凝剂和所述有机絮凝剂在调好pH值的煤气化废水中的投加量分别为100~1000mg/L和1~30mg/L;氧化剂为过氧化氢、次氯酸钠、二氧化氯和氯气中的至少一种。
10.如权利要求4所述的方法,其特征在于,所述内循环的回流比为3:5~6:5。
说明书
一种臭氧催化氧化塔及应用其处理煤气化废水的方法
技术领域
本发明涉及工业废水处理领域,特别涉及一种臭氧催化氧化塔及应用其处理煤气化废水的方法。
背景技术
煤气化废水的水质成分复杂,其中含有大量的酚类、联苯、吡啶、吲哚和喹啉等有机污染物,还含有氰、无机氟离子和氨氮等有毒有害物质,污染物浓度高,色度也高,属较难生化降解的高浓度有机工业废水。因此煤气化废水的处理,一直是国内外废水处理领域的一大难题。
为了解决上述难题,中国申请号为201110045621.8的发明专利申请公开了一种臭氧催化氧化处理炼化废水反渗透浓水的工艺方法,在常温常压条件下采用臭氧催化氧化工艺对炼化废水反渗透浓水进行处理。具体工艺流程是反渗透浓水经过调节池均质后,经供水泵进入预曝气罐,水在罐中与由臭氧发生器提供的臭氧充分混合反应,出水经提升泵进入催化氧化反应塔,出水可达综合排放标准(GB8978-1996)中的一级标准。预曝气罐和催化氧化反应塔排放的尾气进入尾气净化器,净化后的气体排放。该方法对于有机污染物的氧化处理需要先将炼化废水反渗透浓水送入预曝气罐中经臭氧氧化处理,再送入催化氧化塔中进一步利用催化剂进行氧化处理。由此可见,在预曝气罐中没有充分发挥臭氧对于有机污染物的氧化作用,还需要将炼化废水反渗透浓水再送入催化氧化塔中进一步利用催化剂进行氧化处理。这样的氧化处理过程需要两次泵的抽提,过程略显繁琐,并且需要两种装置(预曝气罐和催化氧化塔),在实际处理炼化废水反渗透浓水工程中占地面积大,投资和运行成本高。
发明内容
本发明实施例公开了一种臭氧催化氧化塔,用于解决煤气化废水在氧化处理过程中需要多个反应装置,导致过程繁琐、投资和运行成本高的问题。技术方案如下:
一种臭氧催化氧化塔,该氧化塔包括氧化塔本体、臭氧发生器、循环泵和尾气破坏装置;
所述氧化塔本体包括第一微孔曝气盘、第二微孔曝气盘、催化剂层、进水口、出水口、至少一个氧化剂加药口、排气口、循环进水口和循环出水口;
第一微孔曝气盘位于氧化塔本体底部;第二微孔曝气盘位于第一微孔曝气盘上方;催化剂层位于第二微孔曝气盘上方;第一微孔曝气盘和第二微孔曝气盘分别通过管路与臭氧发生器相连通;
在第一微孔曝气盘和第二微孔曝气盘之间的氧化塔本体侧壁上由下至上依次设置有进水口和循环进水口;在催化剂层上方的塔体侧壁上由下至上依次设置有循环出水口和出水口;在进水口和循环出水口之间的氧化塔本体侧壁上设置有至少一个氧化剂加药口;在氧化塔本体顶部设置有排气口,排气口通过管路与尾气破坏装置相连通;循环泵的进水端通过管路与循环出水口相连通,循环泵的出水端通过管路与循环进水口相连通。
在本发明的一种优选实施方式中,所述第二微孔曝气盘位于第一微孔曝气盘到出水口高度的1/2处。
在本发明的一种优选实施方式中,在进水口和循环出水口之间的氧化塔本体侧壁上设置有2个氧化剂加药口,优选为4个氧化剂加药口。
本发明还公开了一种处理煤气化废水的方法,包括以下步骤:
将煤气化废水的pH值调至4~10,优选为6~9,之后进行混凝沉淀处理,将经混凝沉淀处理获得的上清液的pH值调至7~9后,将其输送至上述臭氧催化氧化塔内进行臭氧催化氧化处理,并向臭氧催化氧化塔内投加氧化剂;同时进行内循环;上清液在臭氧催化氧化塔内的停留时间为10~60分钟;臭氧催化氧化塔中的催化剂为Poten-SOT型臭氧氧化催化剂;臭氧和氧化剂在所述氧化塔内的上清液中的投加量分别为50~350mg/L和50~300mg/L;
所述Poten-SOT型臭氧氧化催化剂由以下步骤制得:
将臭氧氧化催化剂载体进行预处理;所述预处理为先将臭氧氧化催化剂载体进行至少一次水洗,再将其浸泡在酸溶液中1~48h,然后洗涤至中性,最后干燥处理;
将预处理后的臭氧氧化催化剂载体进行至少一次浸渍处理,所述浸渍处理为将预处理后的臭氧氧化催化剂载体浸泡在浸渍溶液中,20~100℃浸泡6~48h,之后干燥处理;所述浸渍溶液为含有锰、镍、铁、铈、钴和铜中至少3种金属元素的硝酸盐、硫酸盐、醋酸盐或氯化物的混合溶液;所述至少3种金属元素在浸渍溶液中的浓度分别为0.01~1.00mol/L;
将浸渍后的臭氧氧化催化剂载体进行焙烧处理。
在本发明的一种优选实施方式中,所述臭氧氧化催化剂载体选自颗粒状多孔陶瓷、颗粒状活性氧化铝、颗粒状分子筛、煤基柱状活性炭、颗粒状果壳活性炭或颗粒状多硅斜发沸石,并且其粒径为3~6mm,比表面积≥250m2/g,抗压强度>100N,堆积密度>0.17g/mL。
在本发明的一种更优选实施方式中,所述浸渍溶液为锰、镍、铁、铈、钴和铜中6种金属元素的硝酸盐、硫酸盐、醋酸盐或氯化物的混合溶液,其中,锰、镍、铁、铈、钴和铜元素的物质的量之比为(1~50):(1~50):(1~50):(1~50):(1~30):(1~30),并且锰、镍、铁、铈、钴和铜元素在浸渍溶液中的浓度分别为0.01~0.50mol/L。
在本发明的一种优选实施方式中,所述预处理为先将臭氧氧化催化剂载体进行至少一次水洗,再将其浸泡在0.01~1.00mol/L的硝酸溶液中10~30小时,优选地,0.05~0.15mol/L的硝酸溶液中10~24小时,然后洗涤至中性,最后干燥处理。
在本发明的一种优选实施方式中,所述混凝沉淀处理为先向混凝沉淀池中加入无机混凝剂,以100~300转/分的转速搅拌0.5~3.0分钟,再向混凝沉淀池中加入有机絮凝剂,以100~300转/分的转速搅拌0.5~3.0分钟,之后调节转速至30~100转/分,搅拌10~30分钟,最后静止沉淀。
在本发明的一种更优选实施方式中,所述无机混凝剂为聚合氯化铝、聚合硫酸铁、聚合氯化铝铁、聚合硫酸铝、硫酸铝中的至少一种;所述有机絮凝剂为阳离子聚丙烯酰胺、阴离子聚丙烯酰胺、部分水解的聚丙烯酰胺中的至少一种;所述无机混凝剂和所述有机絮凝剂在调好pH值的煤气化废水中的投加量分别为100~1000mg/L和1~30mg/L;氧化剂为过氧化氢、次氯酸钠、二氧化氯和氯气中的至少一种。
在本发明的一种优选实施方式中,所述内循环的回流比为3:5~6:5。
本发明实施例公开了一种臭氧催化氧化塔,只需一个臭氧催化氧化塔即可完成煤气化废水的氧化处理过程,使得氧化处理过程操作简单,而且降低了投资和运行成本。同时,该氧化塔采用两次曝气的结构设计,缩短了臭氧在塔内的停留时间,提高了臭氧的利用率。此外,对废水中的污染物进行梯度氧化反应,先在臭氧与氧化剂作用下,将容易降解的污染物去除掉,再在臭氧、臭氧氧化催化剂和氧化剂三者共同作用下,将稳定性高、难降解的污染物去除掉,从而减少了催化剂用量,降低了废水处理的运行成本。本发明实施例还公开了应用该氧化塔处理煤气化废水的方法,工艺简单,可有效去除煤气化废水中的污染物,出水指标远高于《污水综合排放标准》(GB8978-1996)一级排放标准。