申请日2016.02.29
公开(公告)日2016.06.15
IPC分类号C02F9/04; C02F101/16
摘要
本发明公开了一种经济型火电厂含氨废水处理系统及方法,包括调节池、脱氨剂储罐、液碱储罐、脱氨塔、酸储罐、清水池、汽水分离设备、引风机、高盐废水处理系统及离心风机;调节池的出口、脱氨剂储罐的出口及液碱储罐的出口均与脱氨塔顶部的入口相连通,脱氨塔底部浆液池的出口及酸储罐的出口均与清水池的入口相连通,脱氨塔顶部的出风口与汽水分离设备的入口相连通,汽水分离设备的液体出口与调节池的入口相连通,汽水分离设备的气体出口经引风机与外接设备相连通,清水池的出口与高盐废水处理系统的入口相连通,离心风机的出风口与脱氨塔底部浆液池的入风口相连通。本发明能够有效对氨区废水与精处理再生高盐废水进行处理,并且成本低。
摘要附图
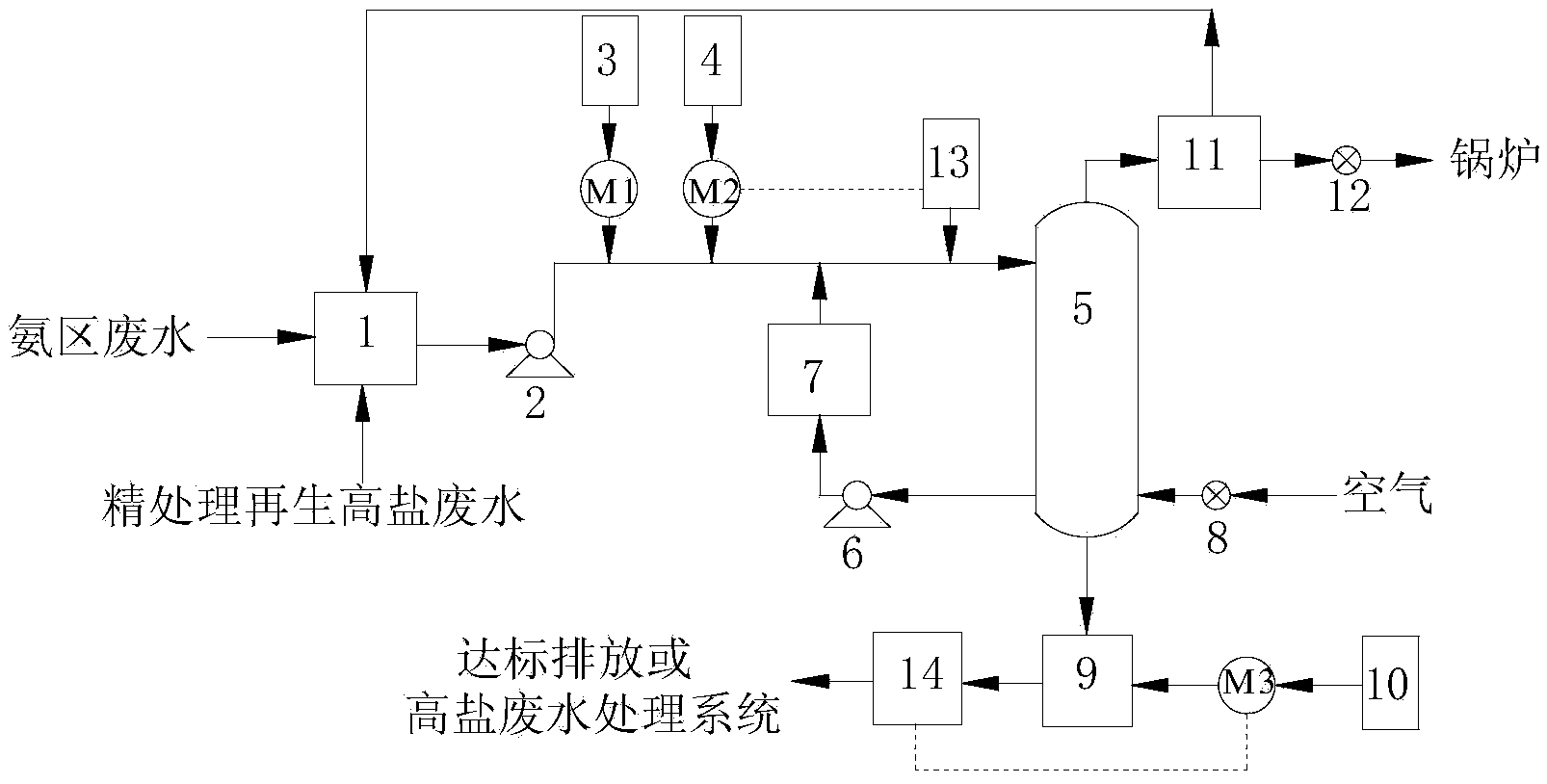
权利要求书
1.一种经济型火电厂含氨废水处理系统,其特征在于,包括调节池(1)、脱氨剂储罐(3)、液碱储罐(4)、脱氨塔(5)、酸储罐(10)、清水池(9)、汽水分离设备(11)、引风机(12)、高盐废水处理系统及离心风机(8);
调节池(1)的出口、脱氨剂储罐(3)的出口及液碱储罐(4)的出口均与脱氨塔(5)顶部的入口相连通,脱氨塔(5)底部浆液池的出口及酸储罐(10的出口均与清水池(9)的入口相连通,脱氨塔(5)顶部的出风口与汽水分离设备(11)的入口相连通,汽水分离设备(11)的液体出口与调节池(1)的入口相连通,汽水分离设备(11)的气体出口经引风机(12)与外接设备相连通,清水池(9)的出口与高盐废水处理系统的入口相连通,离心风机(8)的出风口与脱氨塔(5)底部浆液池的入风口相连通。
2.根据权利要求1所述的经济型火电厂含氨废水处理系统,其特征在于,脱氨剂储罐(3)的出口经脱氨剂计量泵(M1)与脱氨塔(5)顶部的入口相连通。
3.根据权利要求1所述的经济型火电厂含氨废水处理系统,其特征在于,液碱储罐(4)的出口经液碱计量泵(M2)与脱氨塔(5)顶部的入口相连通。
4.根据权利要求1所述的经济型火电厂含氨废水处理系统,其特征在于,酸储罐(10)的出口经酸计量泵(M3)与清水池(9)的入口相连通。
5.根据权利要求1所述的经济型火电厂含氨废水处理系统,其特征在于,还包括循环水泵(6)及换热器(7),循环水泵(6)的入口与脱氨塔(5)底部浆液池的出口相连通,循环水泵(6)的出口经换热器(7)与脱氨塔(5)顶部的入口相连通。
6.根据权利要求1所述的经济型火电厂含氨废水处理系统,其特征在于,清水池(9)的出口与高盐废水处理系统的入口之间设有第一在线pH计(14)。
7.根据权利要求6所述的经济型火电厂含氨废水处理系统,其特征在于,脱氨塔(5)顶部的入口处设有第二在线pH计(13)。
8.根据权利要求1所述的经济型火电厂含氨废水处理系统,其特征在于,调节池(1)通过废水提升泵(2)与脱氨塔(5)顶部的入口相连通。
9.一种经济型火电厂含氨废水处理方法,其特征在于,基于权利要求1所述的经济型火电厂含氨废水处理系统,包括以下步骤:
调节池(1)中的氨区废水与精处理再生高盐废水的混合水、脱氨剂储罐(3)中的脱氨剂、以及液碱储罐(4)中的液碱混合后经脱氨塔(5)顶部的入口进入到脱氨塔(5)中,并在脱氨塔(5)底部的浆液池中生成游离的NH3,同时离心风机(8)排出的空气进入到脱氨塔(5)底部的浆液池中,从而使游离的NH3随空气从脱氨塔(5)顶部的出气口排入到汽水分离设备(11)中,汽水分离设备(11)分离出来的气体经引风机(12)进入到外接设备中,汽水分离设备(11)分离出来的液体返回至调节池(1)中,脱氨塔(5)底部浆液池中的浆液及酸储罐(10)中的酸液进入到清水池(9)中,通过酸液对浆液进行pH调节后排入到高盐废水处理系统中进行废水处理。
说明书
一种经济型火电厂含氨废水处理系统及方法
技术领域
本发明属于节能环保领域,涉及一种含氨废水处理系统及方法,具体涉及一种经济型火电厂含氨废水处理系统及方法。
背景技术
火电厂是工业用水大户,用、排水量均很大。近年来,随着环保减排政策日益收紧,火电企业废水外排压力日渐增大。2015年4月,《水污染防治行动计划》发布,对废水排放标准和污染物排放总量要求空前严格,氨氮等环保敏感指标已成为火电厂废水排放的强制控制项目。
火电厂含氨废水主要有精处理再生废水和脱硝氨库区产生的氨区废水。火电厂精处理再生过程步序较多,其中树脂输送、清洗、分离、混合四个步序的排水以及阴、阳树脂正洗排水约占再生废水总量的50%~60%,含盐量较低;进酸/碱、置换、正洗初期排水为高含盐的强酸/碱性废水,氨氮浓度高达4000mg/L左右。随着火电厂深度节水需求的日益增大,很多电厂已经或拟进行精处理再生废水的分类、分质收集改造,低盐废水可收集后送至原水预处理系统处理回用,高盐再生废水的氨氮和含盐量均很高,必须经过适当处理后才能达标排放或进一步深度处理。
2011年7月最新版《火电厂大气污染物排放标准》(GB13223-2011)颁布,对火电机组NOx排放标准提出了非常严格的要求。因此,近年来国内很多火电厂都进行了烟气脱硝改造,多数采用国际上应用最多、最为成熟的选择性催化还原技术(SCR)。SCR原理是在含有NOx的尾气中喷入氨、尿素或者其它含氮化合物,将NOx还原成N2。火电厂由于无法耗尽液氨贮罐内所存全部液氨,为此需将氨库区容器内残余的液氨进行排放;火电厂要定期对氨库区容器及管路进行冲洗,这些过程中排放的废水称为氨区废水,一般收集到氨区废水池,主要污染物为氨氮,浓度约200mg/L。
目前,绝大部分火电厂尚未对含氨废水进行处理,多与其他废水掺混稀释后外排。但随着火电厂深度节水改造工程的逐步实施,外排废水量大幅减少,甚至在部分环保要求高的地区将实现废水零排放。因此,含氨废水掺混稀释的外排方式将不再适用,必须设置单独的处理系统,实现达标处理。
常规的废水氨氮处理工艺有生物法和物化法,其中物化法包括吹脱法/汽提法、蒸氨法、离子交换法、折点氯化法和化学沉淀法(鸟粪石法)。生物法和离子交换法不适合于处理高浓度氨氮废水;折点加氯法操作要求高,药剂成本高,中间产物会生成有害气体;吹脱法/汽提法、蒸氨法的投资成本高,能耗大,有可能产生二次污染;鸟粪石法用药量大,成本较高,且鸟粪石用途有待开发。
发明内容
本发明的目的在于克服上述现有技术的缺点,提供了一种经济型火电厂含氨废水处理系统及方法,该系统及方法能够有效对氨区废水与精处理再生高盐废水进行处理,并且成本低,节能环保。
为达到上述目的,本发明所述的经济型火电厂含氨废水处理系统包括调节池、脱氨剂储罐、液碱储罐、脱氨塔、酸储罐、清水池、汽水分离设备、引风机、高盐废水处理系统及离心风机;
调节池的出口、脱氨剂储罐的出口及液碱储罐的出口均与脱氨塔顶部的入口相连通,脱氨塔底部浆液池的出口及酸储罐的出口均与清水池的入口相连通,脱氨塔顶部的出风口与汽水分离设备的入口相连通,汽水分离设备的液体出口与调节池的入口相连通,汽水分离设备的气体出口经引风机与外接设备相连通,清水池的出口与高盐废水处理系统的入口相连通,离心风机的出风口与脱氨塔底部浆液池的入风口相连通。
脱氨剂储罐的出口经脱氨剂计量泵与脱氨塔顶部的入口相连通。
液碱储罐的出口经液碱计量泵与脱氨塔顶部的入口相连通。
酸储罐的出口经酸计量泵与清水池的入口相连通。
还包括循环水泵及换热器,循环水泵的入口与脱氨塔底部浆液池的出口相连通,循环水泵的出口经换热器与脱氨塔顶部的入口相连通。
清水池的出口与高盐废水处理系统的入口之间设有第一在线pH计。
脱氨塔顶部的入口处设有第二在线pH计。
调节池通过废水提升泵与脱氨塔顶部的入口相连通。
本发明所述的经济型火电厂含氨废水处理方法包括以下步骤:
调节池中的氨区废水与精处理再生高盐废水的混合水、脱氨剂储罐中的脱氨剂、以及液碱储罐中的液碱混合后经脱氨塔顶部的入口进入到脱氨塔中,并在脱氨塔底部的浆液池中生成游离的NH3,同时离心风机排出的空气进入到脱氨塔底部的浆液池中,从而使游离的NH3随空气从脱氨塔顶部的出气口排入到汽水分离设备中,汽水分离设备分离出来的气体经引风机进入到外接设备中,汽水分离设备分离出来的液体返回至调节池中,脱氨塔底部浆液池中的浆液及酸储罐中的酸液进入到清水池中,通过酸液对浆液进行pH调节后排入到高盐废水处理系统中进行废水处理。
本发明具有以下有益效果:
本发明所述的经济型火电厂含氨废水处理系统及方法在处理过程中,将氨区废水与精处理再生高盐废水这两种水质及水量相差较大的含氨废水在调节池中混合均匀,保证进入到脱氨塔中含氨废水的水质及水量稳定,通过脱氨剂储罐输出的脱氨剂与碱液储罐输出的碱液与含氨废水进行混合,从而改变含氨废水中NH4+的存在形态,增大液相中NH3的传质速率系数,加快NH3在液相中的传质过程,使平衡向生成NH3的方向偏移,提高氨氮去除速率及效率,降低液碱的用药量和汽液比,大幅降低运行费用,再经离心风机输出的风将NH3带出脱氨塔,并通过汽水分离设备进行分离,其中,气体经引风机进入到外接设备中被利用,避免直接排放NH3污染环境造成二次污染,同时可以避免传统吹脱塔存在的汽液比高、吸收效率低、运行成本高等问题;分离出来的液体进入到调节池中进行循环,脱氨塔底部浆液池中的浆液经酸储罐中的酸调节pH值后进入到后续的高盐废水处理系统进一步处理,从而实现氨区废水与精处理再生高盐废水得到综合处理,并且成本低,节能环保。