公开(公告)日2015.03.04
IPC分类号C02F9/04
摘要
本发明涉及一种高浓度表面活性剂废水处理工艺。目的是提供的工艺具有过程简单、操作简便、运行费用低、处理效果好的特点。技术方案是:一种高浓度表面活性剂废水处理工艺,依次按照以下步骤进行:1)酸解:在搅拌表面活性剂废水的同时加入硫酸进行混合,调节该废水的pH值1-2,静置沉淀1.5-2h,取上清液;2)萃取:在步骤1)获得的上清液中按30-50mL/L废水的比例加入氯仿,充分搅拌后静置沉淀;3)混凝沉淀:取步骤2)获得的上清液,投加NaOH溶液调节废水pH值至中性,同时加入氯化钙、混凝剂和助凝剂,充分搅拌,静置沉淀即可。
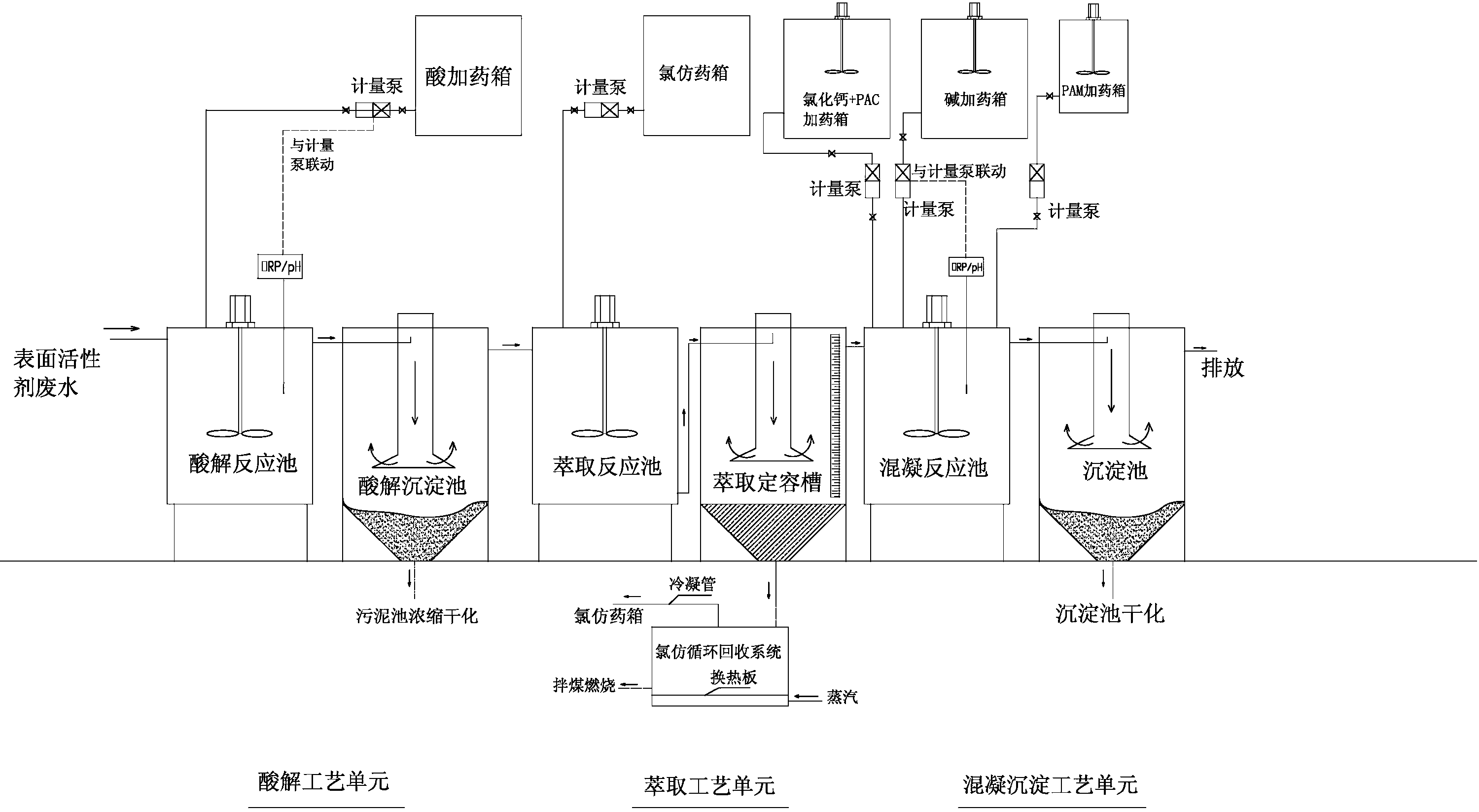
权利要求书
1.一种高浓度表面活性剂废水处理工艺,依次按照以下步骤进行:
1)酸解:在搅拌表面活性剂废水的同时加入硫酸进行混合,调节该废水的pH值1-2,静置沉淀1.5-2h,取上清液;
2)萃取:在步骤1)获得的上清液中按30-50mL/L废水的比例加入氯仿,充分搅拌后静置沉淀;
3)混凝沉淀:取步骤2)获得的上清液,投加NaOH溶液调节废水pH值至中性,同时加入氯化钙、混凝剂和助凝剂,充分搅拌,静置沉淀即可。
2.根据权利要求1所述的高浓度表面活性剂废水处理工艺,其特征在于:所述酸解步骤中的搅拌时间不小于1h,静置沉淀1.5-2h。
3.根据权利要求2所述的高浓度表面活性剂废水处理工艺,其特征在于:所述萃取步骤中的混合搅拌时间不小于1.5h,静置沉淀时间1.5-2h。
4.根据权利要求3所述的高浓度表面活性剂废水处理工艺,其特征在于:所述混凝沉淀步骤中,废水的中性为pH值7.5-8.5。
5.根据权利要求4所述的高浓度表面活性剂废水处理工艺,其特征在于:所述混凝沉淀步骤中,氯化钙(CaCl2)投加量0.5-1.5g/L。
6.根据权利要求5所述的高浓度表面活性剂废水处理工艺,其特征在于:所述混凝沉淀步骤中,混凝剂为聚合氯化铝(PAC),投加量300-500mg/L,助凝剂为聚丙烯酰胺(PAM),投加量2-4mg/L,混合搅拌时间不小于1.5h,静置沉淀4-6h。
7.根据权利要求6所述的高浓度表面活性剂废水处理工艺,其特征在于:所述萃取步骤中,提取上清液后的萃取物排入氯仿循环回收系统,使其加热至氯仿沸点(61~62℃),然后冷却分离出氯仿和萃取物,提取的氯仿循环使用。
8.根据权利要求7所述的高浓度表面活性剂废水处理工艺,其特征在于:所述氯仿循环回收系统采用电能或者蒸汽进行加热,配套氯仿蒸汽冷却回收管路,回收氯仿后继续循环使用。
说明书
一种高浓度表面活性剂废水处理工艺
技术领域
本发明属于水处理技术领域,可用于高浓度表面活性剂废水(COD≥ 5000mg/L)的处理。
背景技术
表面活性剂(surfactant),是指具有固定的亲水亲油基团,在溶液的表面能定 向排列,并能使表面张力显著下降的物质,具有良好的增溶、乳化、润湿、助 悬、起泡和消泡、消毒、杀菌、抗硬水性及洗涤作用,可分为阴离子表面活性 剂、阳离子表面活性剂及非离子表面活性剂,在生产、生活中得到了广泛的应 用。在生产和使用过程中,大量含表面活性剂废水不可避免地排入自然环境中, 其在环境中大量存在会对生态系统造成严重的危害,表面活性剂废水的处理对 于保护环境、促进经济社会发展都具有十分重要的意义。
现有表面活性剂预处理技术包括泡沫分离法、吸附法、混凝法、膜分离法、 催化氧化法及生物法等。
泡沫分离法是指在含有表面活性剂废水中通入空气而产生大量气泡,使废 水中的表面活性剂吸附于气泡表面而形成泡沫并上升至水面形成泡沫层,除去 泡沫层既可使废水得到净化。大量的试验及工程实践证明,泡沫分离法只适合 浓度较低的表面活性剂废水处理,浓度过高时造成泡沫量过大,清理困难,并 且泡沫层后续无法处理。
吸附法是利用吸附剂的多孔性和大比表面积,将废水中的污染物吸附在表 面从而达到分离的目的。常用的吸附剂有活性炭、吸附树脂、硅藻土及高岭土 等。对于低浓度表明活性剂废水吸附法具有速度快、稳定性好、设备占地小等 优点,但对于高浓度表面活性剂废水存在吸附剂再生困难,运行费用高,预处 理要求高等缺点。
混凝法是在表面活性剂废水中加入混凝剂,一方面利用混凝剂产生的絮体 去除吸附在胶体上的表面活性剂,另一方面利用混凝剂与水相中的表面活性剂 发生化学反应形成难溶性的沉淀。该方法对处理阴离子表面活性剂效果较好, 但是对非离子表面活性剂去除效果有限,对于阴离子和非离子复合废水必须与 其他处理工艺配合使用。
膜分离法是利用膜的高渗透选择性来分离溶液中的溶剂和溶质,常用膜分 离有反渗透、超滤、微滤、电渗析等,其中超滤和纳滤对表面活性剂具有较好 的去除效果。但是对于高浓度表面活性剂废水,预处理工艺复杂、膜易污染、 清洗困难、运行费用高。
催化氧化法是在光能、电能或者氧化还原剂的作用产生氢氧基自由基,氧 化废水中有机物的方法。催化氧化法同时伴随着气浮和絮凝等作用。常用的方 法有光催化氧化法、电催化氧化法及电絮凝法等。催化氧化法对于低浓度表面 活性剂废水处理效果明显,一般作为表面活性剂废水生化法前的预处理单元。 对于高浓度表面活性剂废水的处理效果则不理想。
发明内容
本发明所要解决的技术问题是克服上述背景技术的不足,提供一种工艺过 程简单、操作简便、运行费用低、处理效果好的高浓度表面活性剂废水处理工 艺。
本发明要解决的技术问题是通过以下技术方案实现的:
一种高浓度表面活性剂废水处理工艺,依次按照以下步骤进行:
1)酸解:在搅拌表面活性剂废水的同时加入硫酸进行混合,调节该废水的 pH值1-2,静置沉淀1.5-2h,取上清液;
2)萃取:在步骤1)获得的上清液中按30-50mL/L废水的比例加入氯仿, 充分搅拌后静置沉淀;
3)混凝沉淀:取步骤2)获得的上清液,投加NaOH溶液调节废水pH值 至中性,同时加入氯化钙、混凝剂和助凝剂,充分搅拌,静置沉淀即可。
所述酸解步骤中的搅拌时间不小于1h,静置沉淀1.5-2h。
所述萃取步骤中的混合搅拌时间不小于1.5h,静置沉淀时间1.5-2h。
所述混凝沉淀步骤中,废水的中性为pH值7.5-8.5;
所述混凝沉淀步骤中,氯化钙(CaCl2)投加量0.5-1.5g/L;
所述混凝沉淀步骤中,混凝剂为聚合氯化铝(PAC),投加量300-500mg/L, 助凝剂为聚丙烯酰胺(PAM),投加量2-4mg/L,混合搅拌时间不小于1.5h,静 置沉淀4-6h。
所述萃取步骤中,提取上清液后的萃取物排入氯仿循环回收系统,使其加 热至氯仿沸点(61~62℃),然后冷却分离出氯仿和萃取物,提取的氯仿循环使 用。
所述氯仿循环回收系统采用电能或者蒸汽进行加热,配套氯仿蒸汽冷却回 收管路,回收氯仿后继续循环使用。