申请日2014.04.17
公开(公告)日2014.07.16
IPC分类号C07C63/26; C01F11/46; C07C51/42
摘要
本发明涉及碱减量废水净化领域,特指一种碱减量废水处理后的残渣固废纯化工艺,通过将粗对苯二甲酸固废在胺过量的条件下反应后,加入活性炭搅拌,分离,在液相中加入硫酸,析出对苯二甲酸,再次分离,对产生的硫酸铵进行回收利用。采用上述方案后,省略了烧碱的消耗,降低了回收成本,使资源得到了充分的循环利用。
摘要附图
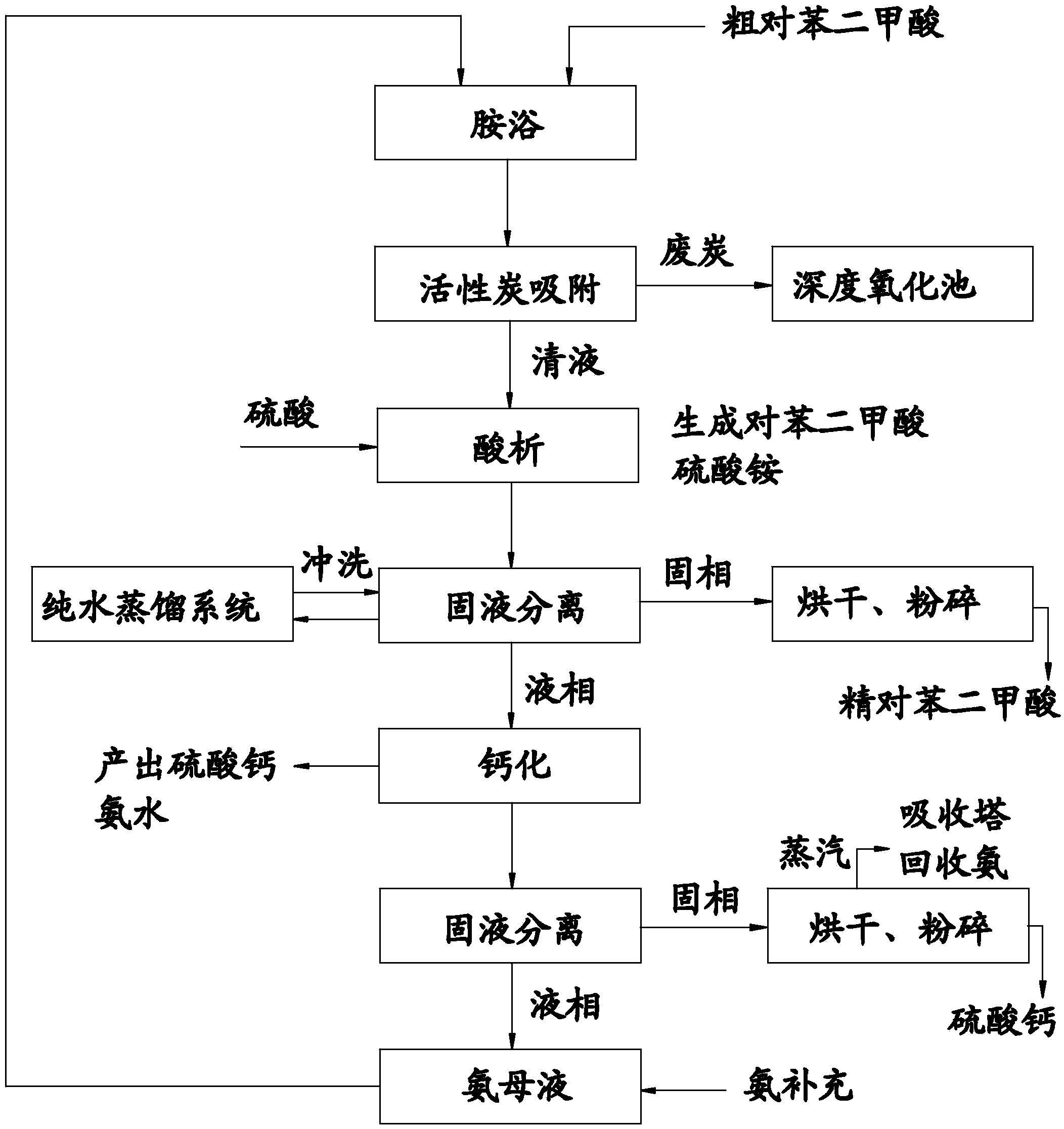
权利要求书
1.一种碱减量废水处理后的残渣固废纯化工艺,包括如下步骤:
(1)将碱减量废水中回收的粗对苯二甲酸固废在胺过量的条件下,反应生成对苯二甲酸铵,得到PH值≥7的胺盐溶液;
(2)在胺盐溶液中加活性炭粉,充分搅拌半小时以上,使活性炭完成吸附,经过滤分离后即可得到胺盐纯清液;
(3)将得到的胺盐纯清液在搅拌状态下,逐步加入硫酸,使得对苯二甲酸铵还原成对苯二甲酸析出,同时硫酸根和胺反应生成硫酸铵溶于母液中;
(4)将以上母液经固液分离,固相对苯二甲酸经纯水循环冲洗,带出硫酸铵后烘干粉碎即为精对苯二甲酸成品;
(5)固液分离后的母液引入钙化池,在搅拌状态下,逐步加入氧化钙或氢氧化钙,反应生成硫酸钙,同时还原出氨水;
(6)硫酸钙和母液固液分离后,用烘干机烘干粉碎成为二水硫酸钙成品,烘干机产生的蒸汽引入吸收塔,回收氨回用;
(7)和硫酸钙分离的母液循环到第一步回收利用。
2.根据权利要求1所述的一种碱减量废水处理后的残渣固废纯化工艺,包括如下步骤:所述步骤(1)中的胺最终能转换成NH3·H2O或NH4OH的含氮化合物,(如氨水,碳酸氢铵,尿素,硫胺等)。
3.根据权利要求1所述的一种碱减量废水处理后的残渣固废纯化工艺,包括如下步骤:所述步骤(2)中的活性炭粉,可以是煤质的,也可以是植物炭的中孔活性炭粉末。
4.根据权利要求1所述的一种碱减量废水处理后的残渣固废纯化工艺,包括如下步骤:所述步骤(3)中硫酸为工业硫酸,在母液搅拌状态下逐步加入,使浓度降低到30%以下,使反应充分,防止对苯二甲酸成团析出,反应终点PH值为6.5-7。
5.根据权利要求1所述的一种碱减量废水处理后的残渣固废纯化工艺,包括如下步骤:所述步骤(4)纯水是去离子水。
6.根据权利要求1所述的一种碱减量废水处理后的残渣固废纯化工艺,包括如下步骤:所述步骤(5)钙化池内为氧化钙或氢氧化钙中的一种或两种。
说明书
一种碱减量废水处理后的残渣固废纯化工艺
技术领域
本发明涉及碱减量废水净化领域,特指一种碱减量废水处理后的残渣固废纯化工艺。
背景技术
现有的从碱减量废水中提取对苯二甲酸的方法,有CN200910096512.1中提到的以烧碱(氢氧化钠)碱解,虽然能得到较高纯度的对苯二甲酸,但烧碱的投入成本较高,且酸析得到的钠盐没有充分利用;CN201110103937提出以极性溶剂DMF进行高温溶解、母液净化、再结晶的工艺中,忽略了碱减量废水产出的对苯二甲酸夹带着强酸,PH值一般在2~3,强酸作为催化剂对DMF产生水解作用,使其水解成蚁酸和二甲基胺,DMF溶剂有损耗,生产成本较高。
因此,本发明人对此做进一步研究,研发出一种碱减量废水处理后的残渣固废纯化工艺,本案由此产生。
发明内容
本发明的目的在于提供一种碱减量废水处理后的残渣固废纯化工艺,在做到从碱减量废水中提取对苯二甲酸的同时,还能实现更好的经济效益。
为了实现上述目的,本发明的技术方案如下:
一种碱减量废水处理后的残渣固废纯化工艺,包括如下步骤:
(1)将碱减量废水中回收的粗对苯二甲酸在胺过量的条件下,反应生成对苯二甲酸铵,得到PH值≥7的胺盐溶液;
(2)在胺盐溶液中加活性炭粉,充分搅拌半小时以上,使活性炭完成吸附,经过滤分离后即可得到胺盐纯清液;
(3)将得到的胺盐纯清液在搅拌状态下,逐步加入硫酸,使得对苯二甲酸铵还原成对苯二甲酸析出,同时硫酸根和胺反应生成硫酸铵溶于母液中;
(4)将以上母液经固液分离,固相对苯二甲酸经纯水循环冲洗,带出硫酸铵后烘干粉碎即为精对苯二甲酸成品;
(5)固液分离后的母液引入钙化池,在搅拌状态下,逐步加入氧化钙或氢氧化钙,反应生成硫酸钙,同时还原出氨水;
(6)硫酸钙和母液固液分离后,用烘干机烘干粉碎成为二水硫酸钙成品,烘干机产生的蒸汽引入吸收塔,回收氨回用;
(7)和硫酸钙分离的母液循环到第一步回收利用。
进一步,所述步骤(1)中的胺最终能转换成NH3·H2O或NH4OH的含氮化合物,(如氨水,碳酸氢铵,尿素,硫胺等)。
进一步,所述步骤(2)中的活性炭粉,可以是煤质的,也可以是植物炭的中孔活性炭粉末。
进一步,所述步骤(3)中硫酸为工业硫酸,在母液搅拌状态下逐步加入,使浓度降低到30%以下,使反应充分,防止对苯二甲酸成团析出,反应终点PH值为6.5-7。
进一步,所述步骤(4)纯水是去离子水。
进一步,所述步骤(5)钙化池内为氧化钙或氢氧化钙中的一种或两种。
采用上述方案后,本发明与现有技术相比,具有以下优点:
省略了烧碱的消耗,降低了回收成本,硫酸钙可回收利用,使资源得到了充分的循环利用。