申请日2014.06.05
公开(公告)日2014.09.03
IPC分类号C02F1/469; C02F9/06
摘要
本发明涉及工业废水处理工艺领域。本发明的基于多级逆流倒极电渗析器的煤化工含盐废水处理方法,包括以下步骤:1)将煤化工含盐废水使用臭氧催化氧化处理;2)将步骤1)臭氧催化氧化后的废水依次经多介质过滤和膜过滤处理;3)将步骤2)膜过滤出水经多级逆流倒极电渗析器处理,实现煤化工含盐废水的深度处理与脱盐回用;其中,所述多级逆流倒极电渗析器包括:电渗析膜堆单元、频繁倒极控制单元和在线监测与过程控制单元。本发明具有淡水回收率高、浓水排放量低、运行成本低、系统运行稳定等优点,可避免常规技术存在淡水回收率低、浓缩倍数低、处理成本高、膜污染严重和系统运行不稳定等问题。
摘要附图
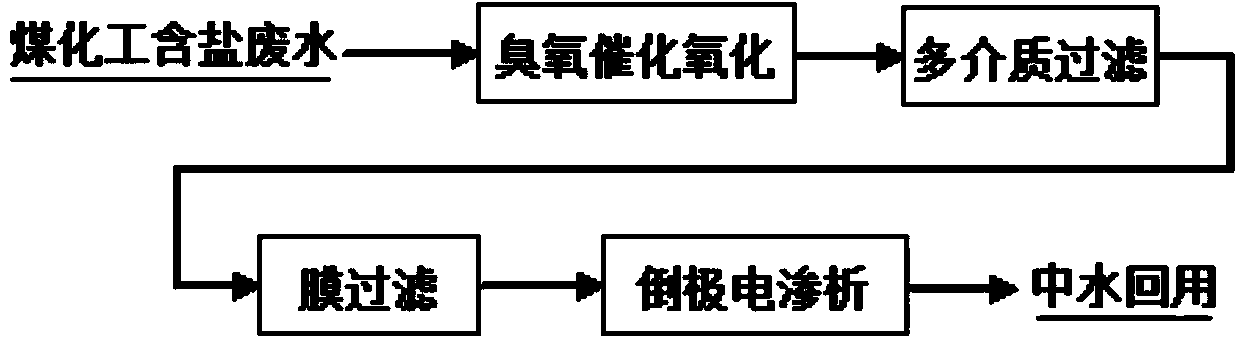
权利要求书
1.一种基于多级逆流倒极电渗析器的煤化工含盐废水处理方法,包括以下步骤:
1)将煤化工含盐废水使用臭氧催化氧化处理;
2)将步骤1)臭氧催化氧化后的废水依次经多介质过滤和膜过滤处理;
3)将步骤2)膜过滤出水经多级逆流倒极电渗析器处理,实现煤化工含盐废水 的深度处理与脱盐回用;
其中,所述多级逆流倒极电渗析器包括:电渗析膜堆单元、频繁倒极控制单元 和在线监测与过程控制单元;
所述电渗析单元包括:电渗析膜堆(3)、输液泵、流量计、压力表、管路、储 液罐(4)和组装框架和整流器(5);所述电渗析膜堆(3)包括:若干交替排列的 抗污染离子交换膜、隔板、膜堆两侧的电极板、夹紧装置,共同构成电渗析膜堆(3) 的极室、脱盐室和浓缩室;由两个以上所述膜堆组成一组,同一组膜堆由一个整流 器(5)并联供电;两组以上的膜堆(3)进行串联;所述储液罐(4)包括极水罐、 浓水罐、淡水罐;所述不同膜堆(3)的不同隔室间的管路串联,控制其浓水/淡水的 流向相反,由此构成多级/逆流体系,以减小膜堆(3)中相邻隔室间的浓差扩散,提 高废水脱盐率与浓缩倍数。
2.根据权利要求1所述的煤化工含盐废水处理方法,其特征在于,所述多介质 过滤使用石英砂、活性炭和粉煤灰作为过滤介质。
3.根据权利要求1所述的煤化工含盐废水处理方法,其特征在于,所述膜过滤 采用微滤、超滤和纳滤膜技术中的一种或几种。
4.根据权利要求1所述的煤化工含盐废水处理方法,其特征在于,所述倒极控 制单元包括:PLC单元(6)、自动控制阀和整流器(5),用于完成电渗析膜堆(3) 倒极过程中自动控制阀开启或关闭、整流器(5)正负极换向信号输出,以及电渗析 过程控制;通过触摸屏进行膜堆(3)的倒极时间间隔、电源关闭或开启的延时时间 以及手动自动模式的设定。
5.根据权利要求1所述的煤化工含盐废水处理方法,其特征在于,所述参数在 线监测与过程控制单元包括:电导率传感器(1)、温度传感器(2)、无纸记录仪、 PLC单元(6)和自动控制阀;所述多个电导率传感器(1)安装在膜堆中淡水和/或 浓水的出水管,用于在线监测一组膜堆(3)淡水脱盐率和浓水浓缩倍数;通过PLC 单元(6)把电导率传感器(1)的数据传输到无纸记录仪保存,并与预设值进行比 较,由PLC单元(6)输出信号控制对应自动控制阀开启或关闭,实现不同隔室溶液 在膜堆(3)中循环或部分循环,使管路中淡水/浓水返回另一组膜堆(3)处理或直 接排放;所述温度传感器(2),用来监测膜堆极室溶液的温度。
6.根据权利要求1、4或5所述的煤化工含盐废水处理方法,其特征在于,所 述的抗污染离子交换膜是在离子膜表面覆盖与本体膜带相反电荷的薄膜层,利用静 电作用和减小膜表面粗糙度,抑制污染物在膜表面的吸附沉积。
说明书
基于多级逆流倒极电渗析器的煤化工含盐废水处理方法
技术领域
本发明涉及工业废水处理工艺领域,具体地,本发明涉及基于多级逆流倒极电 渗析器的煤化工含盐废水处理方法。
背景技术
煤化工含盐废水主要来源于生产过程中煤气洗涤废水、循环水系统排水、化学 水站排水等,有时还包括生化处理后的有机废水,其特点是含盐量高、污染物以总 含盐量为主,部分废水中还含有难降解的有机物。这类废水TDS通常在5000mg/L 左右,甚至更高,无法直接回用。目前,这类工业废水虽然COD、氨氮等达到环保 外排标准,但水里面含有NaCl、Na2SO4、CaCl2、MgSO4、MgCl2等盐类,直接回用 会引起设备结垢、腐蚀和软泥沉积等,需进行脱盐处理。虽然可用于煤灰增湿及冲 洗路面或冲厕所,但消耗量也很有限。因此,需要对煤化工含盐废水进行深度处理 和脱盐回用,实现废水循环利用和减少外排。
尽管目前关于煤化工废水处理的报道较多,但大多是研究如何实现煤化工废水 达标排放。如王奉军(小氮肥,2010,38(1):1-4)报道了A/O法处理煤化工废水的应 用;王文标等(广东化工,2010,37(6):186-188)报道了采用氯碱氧化/混凝气浮/HBF-N 联合工艺处理安徽某煤化工企业综合废水,出水可达到一级排放标准;唐秀华(中 国给水排水,2011,27(16):85-87)报道了强化生物脱碳脱氮及回用工艺处理煤化工废 水,并采用臭氧生物活性炭技术作为深度处理单元,出水水质虽然达到《城市污水 再生利用工业用水水质》标准,但仍无法作为工业循环水再利用。近年来有关煤化 工废水处理与应用的发明专利,如《煤化工废水的生化处理方法》 (CN201310198071)、《一种高浓度含酚氨煤化工废水的萃取脱酚方法》 (CN103496757)、《煤化工废水外循环移动床反应器和曝气生物滤池联用短程脱氮 系统及方法》(CN103351078)、《煤气化废水深度处理系统》(CN201310475332)等, 大多是提出利用生物法、臭氧氧化、萃取等方法或联合使用,目的是使煤化工废水 实现达标排放。
煤化工含盐废水尽管可达到国家和地方废水排放标准(COD<100mg/L,SS<60 mg/L,pH6~9),但这类工业废水中仍存在部分难降解有机物、微生物、胶体、颗粒 悬浮物、Ca2+和Mg2+及其他高价离子、无机盐等。目前,通常采用膜分离或热浓缩 工艺富集废水中的杂质,清水回用于循环水系统,浓水外排。如谢晓和凌怡敏(水 处理信息报导,2010,6:15-20)探讨了煤化工废水零排放策略,指出国外处置高含盐 废水及废水零排放的措施有:自然蒸发塘、深井灌注、焚烧、蒸汽驱动的多效蒸发、 机械压缩循环蒸发技术(MVC)等;而国内采用节水工艺提高用水效率,以及通过膜 技术如反渗透膜(RO)、电渗析(ED)、微滤(MF)、超滤(UF)和膜生物反应器(MBR)工 艺等技术处理,最大限度地减少高含盐废水量。郭森等(煤化工,2011,1:27-30)探 讨了煤化工含盐废水的处理方法,认为反渗透膜技术和热浓缩工艺可用于煤化工含 盐废水的处理。近年来有关高含盐工业废水处理与零排放的发明专利,如《利用循 环水余热处理高含盐废水的装置及方法》(CN103553166)、《利用废热烟气处理高含 盐废水的方法》(CN103553170)、《一种农化高浓含盐废水处理工艺》(CN103601331), 大多是利用热浓缩工艺来实现高含盐废水减排。
目前煤化工含盐废水主要是采用热浓缩和膜技术处理,但热浓缩工艺普遍存在 设备庞大、能耗高的问题,而且废水热浓缩过程中氯离子对设备的腐蚀及钙镁离子 的结垢,会造成维护费用高,而且加大企业的投资和运行风险。采用超滤-反渗透双 膜法处理煤化工废水,仅有60%-70%的淡水回用,剩余30%-40%的浓水还需外排。 由于废水中有机物浓度较高,容易形成膜污染,需要经常进行化学清洗,造成膜使 用寿命缩短,膜材料损耗大,系统无法长期稳定运行,投资运行成本高。而且外排 废水中盐分大,外排很容易造成土壤板结,严重时会使土壤盐碱化。电渗析技术虽 然在苦咸水淡化、海水浓缩制盐等获得应用,但由于受到反渗透技术的冲击,目前 该技术处于停滞和萎缩状态。采用常规电渗析技术处理煤化工含盐废水,由于煤化 工含盐废水中的杂质含量高,还含有少量难降解有机物,必然会导致电渗析过程脱 盐效率低、膜污染严重、系统难以长期稳定运行、维护成本高等问题。总之,现有 脱盐技术用于煤化工含盐废水处理,其设备投资和运行成本都较高,经济上不合算。 需进一步研究高效、低成本的废水处理技术,提高这类废水的回收利用率。
发明内容
针对煤化工含盐废水的水质特点,本发明提出了一种采用多级逆流倒极电渗析 处理煤化工含盐废水的新方法,该方法把倒极电渗析与臭氧催化氧化、多介质过滤、 膜过滤等技术耦合,实现煤化工含盐废水的深度处理与脱盐回用。采用该技术处理 煤化工含盐废水,具有淡水产率高、浓水排放量小、降低电渗析膜污染和提高系统 运行稳定性等特点,其中淡水产率超过85%,浓水浓缩10倍以上。该方法可避免常 规超滤-反渗透技术处理煤化工含盐废水时存在淡水回收率低、浓缩倍数低、运行成 本高、膜污染严重和系统运行不稳定等问题,可促进煤化工等行业含盐废水深度处 理与脱盐回用的工程化应用。
具体地,本发明的基于多级逆流倒极电渗析器的煤化工含盐废水处理方法,包 括以下步骤:
1)将煤化工含盐废水使用臭氧催化氧化处理;
2)将步骤1)臭氧催化氧化后的废水依次经多介质过滤、精密过滤和膜过滤处 理;
3)将步骤2)膜过滤出水经多级逆流倒极电渗析器处理,实现煤化工含盐废水 的深度处理与脱盐回用;
其中,所述多级逆流倒极电渗析器包括:电渗析膜堆单元、频繁倒极控制单元 和在线监测与过程控制单元;
所述电渗析单元包括:电渗析膜堆3、输液泵、流量计、压力表、管路、储液罐 4、组装框架和整流器5;所述电渗析膜堆3包括:若干交替排列的抗污染离子交换 膜、隔板、膜堆两侧的电极板、夹紧装置,共同构成电渗析膜堆3的极室、脱盐室 和浓缩室;由两个以上所述膜堆组成一组,同一组膜堆由一个整流器5并联供电;两 组以上的膜堆3进行串联;所述储液罐4包括极水罐、浓水罐、淡水罐;所述不同 膜堆3的不同隔室间的管路串联,控制其浓水/淡水的流向相反,由此构成多级/逆流 体系,以减小膜堆3中相邻隔室间的浓差扩散,提高废水脱盐率与浓缩倍数。
所述倒极控制单元包括:PLC单元6、自动控制阀和整流器5,用于完成电渗析 膜堆3倒极过程中自动控制阀开启或关闭、整流器5正负极换向信号输出,以及电 渗析过程控制;通过触摸屏进行膜堆3的倒极时间间隔、电源关闭或开启的延时时 间以及手动自动模式的设定。
所述参数在线监测与过程控制单元包括:电导率传感器1、温度传感器2、无纸 记录仪、PLC单元6、自动控制阀;所述多个电导率传感器1安装在膜堆中淡水和/ 或浓水的出水管,用于在线监测一组膜堆3淡水脱盐率和浓水浓缩倍数;通过PLC 单元6把电导率传感器1的数据传输到无纸记录仪保存,并与预设值进行比较,由 PLC单元6输出信号控制对应自动控制阀开启或关闭,实现不同隔室溶液在膜堆3 中循环或部分循环,使管路中淡水/浓水返回另一组膜堆3处理或直接排放;所述温 度传感器2,用来监测膜堆极室溶液的温度。
本发明所述的煤化工含盐废水,包括但不限于来源于煤化工行业生产过程中的 煤气洗涤废水、循环水系统排水、化学水站排水等,有时还包括生化处理后的有机 废水,其特点是含盐量高(TDS通常在5000mg/L左右甚至更高),还含有部分难降 解有机物,这类废水需要进一步深度处理和电渗析脱盐才能实现回用。煤化工含盐 废水中含有部分难降解有机物,以及细菌、胶体、颗粒悬浮物、Ca2+和Mg2+及其他 高价离子、其他可溶性无机盐等,虽然达到了外排标准,但会造成大量的水资源浪 费,要实现这种工业废水资源化与循环利用,必需进一步去除废水中的残余有机物 和无机盐等。本发明提出了一种采用多级逆流倒极电渗析处理煤化工含盐废水的方 法,其特征在于经过常规处理达标排放的煤化工含盐废水,先采用臭氧催化氧化、 多介质过滤、膜过滤等技术处理,并采用多级逆流倒极电渗析脱盐,实现煤化工含 盐废水的深度处理与脱盐回用。其目的是利用多级逆流倒极电渗析与臭氧催化氧化、 多介质过滤和膜过滤等技术的耦合与协同作用,发挥不同技术优势和克服单一技术 的局限性。本发明提出的电渗析处理煤化工含盐废水的新方法,可避免常规超滤-反 渗透技术处理煤化工含盐废水时存在淡水回收率低、浓缩倍数低、处理成本高、膜 污染严重和系统运行不稳定等问题。该方法具有对原水适应性强、淡水回收率高、 浓水浓缩倍数高等特点,大幅度提高煤化工含盐废水的淡水回收率和减少浓水排放 量,该技术还适用于化工、油田、纺织、造纸等行业含盐废水的深度处理与脱盐回 用。
所述多级逆流倒极电渗析处理煤化工含盐废水的方法,其特点是,所述的多级 逆流倒极电渗析脱盐单元,采用煤化工含盐废水处理的专用电渗析器和电渗析膜堆 优化组合,可显著提高淡水回收率、降低浓水排放量、减小膜污染和提高系统运行 稳定性。
所述用于煤化工含盐废水处理的多级逆流倒极电渗析单元,其特点是,所述专 用电渗析器由电渗析膜堆单元、倒极控制单元、在线监测与过程控制单元等共同构 成。电渗析系统通过多个电渗析膜堆串联或并联,实现煤化工含盐废水的多级脱盐 或浓缩处理;通过膜堆间不同隔室的管路连接与溶液流向控制,使每组电渗析膜堆 的淡水与浓水流向相反,减小相邻淡水与浓水隔室间的浓差扩散,提高淡水脱盐率 和浓水浓缩倍数;通过PLC控制系统、整流器和自动控制阀(如电动阀、气动阀或 电磁阀)等,共同实现电渗析脱盐单元自动倒极,且倒极周期可根据煤化工含盐废 水水质和处理目标进行调节,减小电渗析过程的浓差极化和膜污染。采用所述的多 级逆流倒极电渗析单元处理煤化工含盐废水,可实现淡水产率大于85%,浓水浓缩 10倍以上。
所述多级逆流倒极电渗析单元,是指至少2个或2个以上电渗析膜堆串联及其 组合,提高淡水脱盐率和浓水浓缩倍数,可实现煤化工含盐废水脱盐率为80%-95%, 满足工业水回用标准,且脱盐率可根据处理目标进行调节。
本发明所述的抗污染离子交换膜是在离子膜表面覆盖与本体膜带相反电荷的薄 膜层,利用静电作用和减小膜表面粗糙度,抑制污染物在膜表面的吸附沉积。
本发明的多级逆流倒极电渗析处理煤化工含盐废水的方法,利用多介质过滤、 精密过滤和膜过滤等进一步处理经臭氧催化氧化后的出水,去除废水中残余的少量 胶体、悬浮物、菌体、大分子有机物等。其中,所述多介质过滤使用石英砂、活性 炭和粉煤灰作为过滤介质;所述膜过滤采用微滤、超滤和纳滤膜技术中的一种或几 种。通过优选膜组件及其组合,提高膜过滤出水水质,减小后续倒极电渗析脱盐过 程的膜污染。
所述臭氧催化氧化单元,采用高效催化剂来提高臭氧氧化效率,可促进难降解 有机物的氧化去除,大幅度降低煤化工含盐废水中残余的难降解有机物。具体地, 所述臭氧催化氧化在臭氧催化塔中进行,其中填充碳基复合型高效催化剂(如 KL-CO3),催化剂使用寿命为1-3年。所述臭氧催化氧化技术,具有催化氧化效率 高、不带入其他杂质、对高含盐工业废水中难降解有机物去除效果好等优点。该臭 氧催化氧化单元可弥补电渗析脱盐单元不能去除有机物的不足,提高电渗析产水水 质和减小电渗析膜污染。本发明提出采用臭氧催化氧化处理煤化工含盐废水,具有 催化氧化效率高、不带入其他杂质、对废水中难降解有机物去除效果好等优点。同 时不排除其他高级氧化技术如(电)芬顿、湿式氧化法、紫外催化氧化等的使用, 其目标是去除煤化工含盐废水中残余的有机物、硫化物和Fe2+等,使难降解有机物 发生开环和氧化降解、以及杀灭细菌等。
所述多级逆流倒极电渗析与臭氧催化氧化、多介质过滤、膜过滤等单元技术耦 合,可预先去除煤化工含盐废水中的细菌、颗粒悬浮物、胶体、大分子有机物、Ca2+和Mg2+及高价离子等,减小后续电渗析膜污染,膜清洗周期延长3-6个月。同时可 降低水处理运行成本和提高系统运行稳定性。
本发明提出了一种采用多级逆流倒极电渗析处理煤化工含盐废水的方法,并与 臭氧催化氧化、多介质过滤、膜过滤等技术耦合与协同作用,实现煤化工含盐废水 的深度处理与脱盐回用。具有淡水回收率高、浓水排放量低、运行成本低、系统运 行稳定等优点,可避免常规超滤-反渗透技术处理煤化工含盐废水时存在淡水回收率 低、浓缩倍数低、处理成本高、膜污染严重和系统运行不稳定等问题。其中产生淡 水可作为生产工艺水、循环冷却水或锅炉水等;少量浓水可进一步蒸发或用于洗煤、 冲渣等,不会对环境造成污染。
本发明与现有技术相比的优点在于:
(1)本发明采用多级逆流倒极电渗析用于煤化工含盐废水处理,与臭氧催化氧 化、多介质过滤、膜过滤等技术耦合与协同作用,实现煤化工含盐废水的深度处理 与脱盐回用,对原水适应范围广、抗冲击性强、系统运行稳定。
(2)本发明提出的煤化工含盐废水深度处理与脱盐回用处理工艺,具有淡水回 收率高、浓水浓缩倍数高、运行成本低等特点。系统产水率大于85%,而外排浓水 量小于15%。
(3)本发明提出的煤化工含盐废水深度处理与脱盐回用处理工艺,采用高效臭 氧氧化催化剂,可提高废水中难降解有机物的去除率,显著减小后续处理过程的膜 污染和提高产水水质。