申请日2014.12.19
公开(公告)日2015.05.27
IPC分类号C02F103/24; C02F9/14
摘要
本实用新型涉及制革废水处理系统,包括平行设置的含硫废水处理系统和含铬废水处理系统,其中含硫废水处理系统包括顺次相接的第一格栅机、初沉池和第一SBR反应池,含铬废水处理系统包括顺次相接的第二格栅机、暂存池和第二SBR反应池,所述第二SBR反应池的上清液出水管接入所述初沉池;第一SBR反应池之后顺次连接有生物微电解池、高能物理氧化处理设备,高能物理氧化处理设备的出水口接入清水池或污水厂接管,清水池之后顺次连接有砂缸过滤器、炭缸过滤器、滤芯、超滤装置、纳滤系统和反渗透系统,纳滤系统的出水口连接直排水管,反渗透系统的出水口连接回用水管。该系统具有更高的制革废水处理效果,且处理后的废水能够实现不同的出水标准。
摘要附图
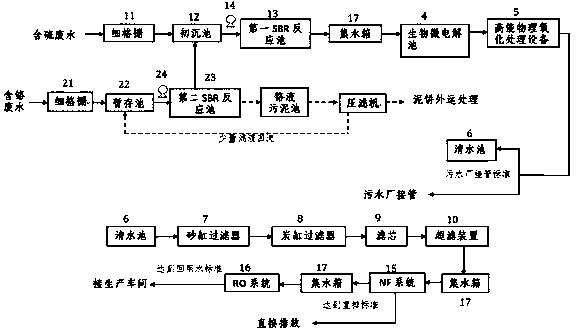
权利要求书
1.一种制革废水处理系统,其特征在于:包括平行设置的含硫废水处理系统和含铬废水处理系统,其中含硫废水处理系统包括顺次相接的第一格栅机(11)、初沉池(12)和第一SBR反应池(13),含铬废水处理系统包括顺次相接的第二格栅机(21)、暂存池(22)和第二SBR反应池(23),所述第二SBR反应池(23)的上清液出水管接入所述初沉池(12),所述第一SBR反应池(13)和第二SBR反应池(23)的排泥管分别外接污泥处理系统;第一SBR反应池(13)之后顺次连接有生物微电解池(4)、高能物理氧化处理设备(5),高能物理氧化处理设备(5)的出水口接入清水池(6)或污水厂接管,清水池(6)之后顺次连接有砂缸过滤器(7)、炭缸过滤器(8)、滤芯(9)、超滤装置(10)、纳滤系统(15)和反渗透系统(16),所述纳滤系统(15)的出水口连接直排水管,所述反渗透系统(16)的出水口连接回用水管。
2.根据权利要求1所述的制革废水处理系统,其特征在于:所述第一SBR反应池(13)和第二SBR反应池(23)分别独立地配置或共同配置有加药箱和曝气装置。
3.根据权利要求2所述的制革废水处理系统,其特征在于:所述加药箱包括FeCl2、HCl加药箱,NaOH加药箱,PAM加药箱。
4.根据权利要求1所述的制革废水处理系统,其特征在于:所述初沉池(12)和第一SBR反应池(13)之间设置有第一提升泵(14),所述第一SBR反应池(13)预设有高液位。
5.根据权利要求1所述的制革废水处理系统,其特征在于:所述暂存池(22)和第二SBR反应池(23)之间设置有第二提升泵(24),所述第二SBR反应池(23)预设有高液位。
6.根据权利要求1所述的制革废水处理系统,其特征在于:所述生物微电解池(4)、纳滤系统(15)或反渗透系统(16)之前设置有集水箱(17)。
说明书
一种制革废水处理系统
技术领域
本实用新型涉及制革废水处理系统,具体涉及采用SBR反应池的制革废水处理系统,并能够使废水达到污水厂接管、直排或回用水标准。
背景技术
制革废水是一种成分复杂、高浓度的有机废水,含有大量石灰、染料、蛋白质、盐类、油脂、氨氮、硫化物、铬鞣剂、中和剂和毛、碎皮、油渣、肉渣、泥砂等物质;CODCr、BOD5、硫化物、悬浮物非常高,是一种较难治理的工业废水。根据制革厂的加工工序及分质分流要求,制革废水主要分为含硫废水、含铬废水及其它综合废水。含硫废水及含铬废水中分别含有高浓度的硫化物和重金属铬,不利于污水的达标处理,若将含硫、含铬废水与其他综合废水一起混合后进行处理,会增大废水后续处理的负担,造成污水处理成本过大。含硫废水的预处理方法有酸化法、化学沉淀法和氧化法,含铬废水预处理一般采用碱沉淀法。传统的预处理方法是采用多级反应池串联运行,具有占地面积大、管网布置繁琐、化学药剂消耗量大、污泥产生量大、运行管理困难等缺点。基于上述运行现状,迫切需要对现有制革废水处理系统作出改进,提高废水的处理效果,并使废水达到不同的出水标准,满足不同企业的废水后处理要求。
实用新型内容
本实用新型所要解决的技术问题是针对上述现有技术提供一种改进的制革废水处理系统,能够提高制革废水的预处理效果,降低后续废水处理负担,使废水能够达到不同的出水标准。
本实用新型解决上述问题所采用的技术方案为:一种制革废水处理系统,包括平行设置的含硫废水处理系统和含铬废水处理系统,其中含硫废水处理系统包括顺次相接的第一格栅机、初沉池和第一SBR反应池,含铬废水处理系统包括顺次相接的第二格栅机、暂存池和第二SBR反应池,所述第二SBR反应池的上清液出水管接入所述初沉池,所述第一SBR反应池和第二SBR反应池的排泥管分别外接污泥处理系统;第一SBR反应池之后顺次连接有生物微电解池、高能物理氧化处理设备,高能物理氧化处理设备的出水口接入清水池或污水厂接管,清水池之后顺次连接有砂缸过滤器、炭缸过滤器、滤芯、超滤装置、纳滤系统和反渗透系统,所述纳滤系统的出水口连接直排水管,所述反渗透系统的出水口连接回用水管。
优选地,所述第一SBR反应池和第二SBR反应池分别独立地配置或共同配置有加药箱和曝气装置。所述加药箱包括FeCl2、HCl加药箱,NaOH加药箱,PAM(聚丙烯酰胺)加药箱。
优选地,所述初沉池和第一SBR反应池之间设置有第一提升泵,所述第一SBR反应池预设有高液位,第一提升泵受高液位控制,当第一SBR反应池满至高液位时,第一提升泵停止工作。
优选地,所述暂存池和第二SBR反应池之间设置有第二提升泵,所述第二SBR反应池预设有高液位,第二提升泵受高液位控制,当第二SBR反应池满至高液位时,第二提升泵停止工作。
进一步地,所述生物微电解池、纳滤系统或反渗透系统之前设置有集水箱,以便于在不同装置之间实现污水的存储。
上述制革废水处理系统的具体工艺为:
含硫废水通过第一格栅机和初沉池去除毛皮、碎肉、泥沙等大颗粒物质后进入第一SBR反应池。第一SBR反应池包括进水、反应、沉淀、排水排泥等阶段,主要用于去除含硫废水中的硫化物,第一SBR反应池配备FeCl2、HCl加药箱,NaOH加药箱,PAM加药箱及曝气装置。操作时先由第一提升泵从初沉池抽水泵入第一SBR反应池,当第一SBR反应池满至高液位时,第一提升泵停止工作;进水结束后,向第一SBR反应池内加入FeCl2、HCl,通过pH计控制pH在6.0~7.0,同时曝气工作6h; 然后,加入NaOH、PAM,控制pH在7.5~8.5,同时曝气工作1h;反应结束后自然沉淀1h,第一SBR反应池上清液排入后面的集水箱待后处理,底层污泥则排入污泥处理系统。
含铬废水通过第二格栅机将水中的毛皮、肉块等大颗粒悬浮物除去后送入暂存池,再泵入第二SBR反应池。第二SBR反应池包括进水、反应、沉淀、排水排泥等阶段,主要用于去除含铬废水中的铬,第二SBR反应池也配备FeCl2、HCl加药箱,NaOH加药箱,PAM加药箱及曝气装置,加药箱与曝气装置可与第一SBR反应池共用。第二SBR反应池在pH 6.0~7.0条件下投加FeCl2,曝气一段时间后加入NaOH,并调节pH至8.5~10,接着曝气反应1h,静止沉淀一段时间后,上清液送入初沉池与含硫废水混合一起进入第一SBR反应池作进一步处理,底层污泥排入污泥处理系统。
收集于第一SBR反应池之后的集水箱的废水通过提升泵送入生物微电解池进行微电解反应及生物氧化降解反应,本发明中生物微电解池内布置有微电解转笼,微电解转笼中装填了生物微电解球(ME球),污水浸没ME球后在表面形成生物膜,水体中的多肽链有机物被微生物氧化分解,同时由微生物厌氧阶段产生的氢气、甲酸等形成原位电池,进一步对污染物进行微电解氧化降解。
经生物微电解池处理后的废水进入高能物理氧化处理设备进行更深度的氧化降解以及杀菌消毒。高能物理氧化处理设备内安装了高能粒子氧化反应池,在外加电场下,粒子发射场表面的粒子束在达到一定能量时对水溶液进行轰击,产生的强氧化性物质(羟基自由基和氢质子等)对水体中的污染物进行无选择的强氧化反应和强氧化还原反应,使长链分子结构物质得以断链、开环,将NH2·、OH·、CH3·从大分子有机物中分离开来,生成小分子物质;其次,轰击水分子产生的H·能与水体中的NH2·、OH·、CH3·结合生成NH3、H2O和CH4,有效地降低了水体中的氨氮,并大大降低了COD。经高能物理氧化处理设备处理的废水可直接送入清水池或接管污水厂。
进一步地,将清水池中的废水抽入砂缸过滤器及炭缸过滤器去除悬浮颗粒物,并通过滤芯作进一步处理,之后送入超滤系统超滤,滤液注入集水箱。设置的砂缸过滤器、炭缸过滤器和滤芯有助于减少后续超滤膜处理系统的负荷,提高作业效率。接着,将集水箱中的废水泵入纳滤系统,经纳滤处理后出水可达到直排标准,或者将纳滤处理后的废水送入另一集水箱,并将该集水箱中的水泵入反渗透系统进行反渗透过滤,处理后的滤液可作为回用水直接接入车间进行中水回用。
与现有技术相比,本实用新型的优点在于:
(1)将制革生产过程中分流的含硫废水和含铬废水分开预处理,根据不同杂质形式和杂质含量进行相应的去除处理,能够显著提高预处理效果,缓减后续污水处理负担。所采用的SBR反应池以时间分割的操作方式替代空间分割的操作方式,集均化、反应、沉淀等功能于一体,大大减少了处理工艺单元的占地面积以及相应管件的设置,简化了管网布置,便于控制管理。
(2)在预处理之后顺次设置有不同出水标准的处理设备,按需要分别实现了污水厂接管标准、直排标准、回用水标准,满足了不同制革厂家的污水处理需要。
(3)微电解转笼工艺集合了生物氧化降解和原电池微电解氧化降解,高能物理氧化分解技术利用高能粒子束对水溶液进行轰击,产生大量的强氧化性物质,对水体中的各类有机物进行强氧化降解,两种技术结合后具有极高的污染物去除率。