申请日2015.09.09
公开(公告)日2017.03.22
IPC分类号C02F9/10; C02F101/16; C02F103/16
摘要
本发明公开了一种含氯化铵废水的回收利用工艺。该工艺包括:向含氯化铵废水中加入碱性物质形成浆液,并对浆液加热收集氨气;以及利用氨气与二氧化碳气体对金属氯化物溶液进行沉淀反应固液分离,得到金属碳酸盐和/或金属碱式碳酸盐以及沉淀废液;将沉淀废液返回用作含氯化铵的废水。该工艺通过将含氯化铵的废水回收得到氨气,并将其与二氧化碳用于沉淀金属氯化物溶液从而得到金属碳酸盐和/或金属碱式碳酸盐,而产生废水再次循环利用。该工艺将废水治理与金属冶炼分离工艺相结合,不但处理了复杂的氨氮废水,实现了氨的循环利用,而且获得了金属碳酸盐和/或金属碱式碳酸盐产品;且二氧化碳气体也可从工业废气得到,减少温室气体排放。
摘要附图
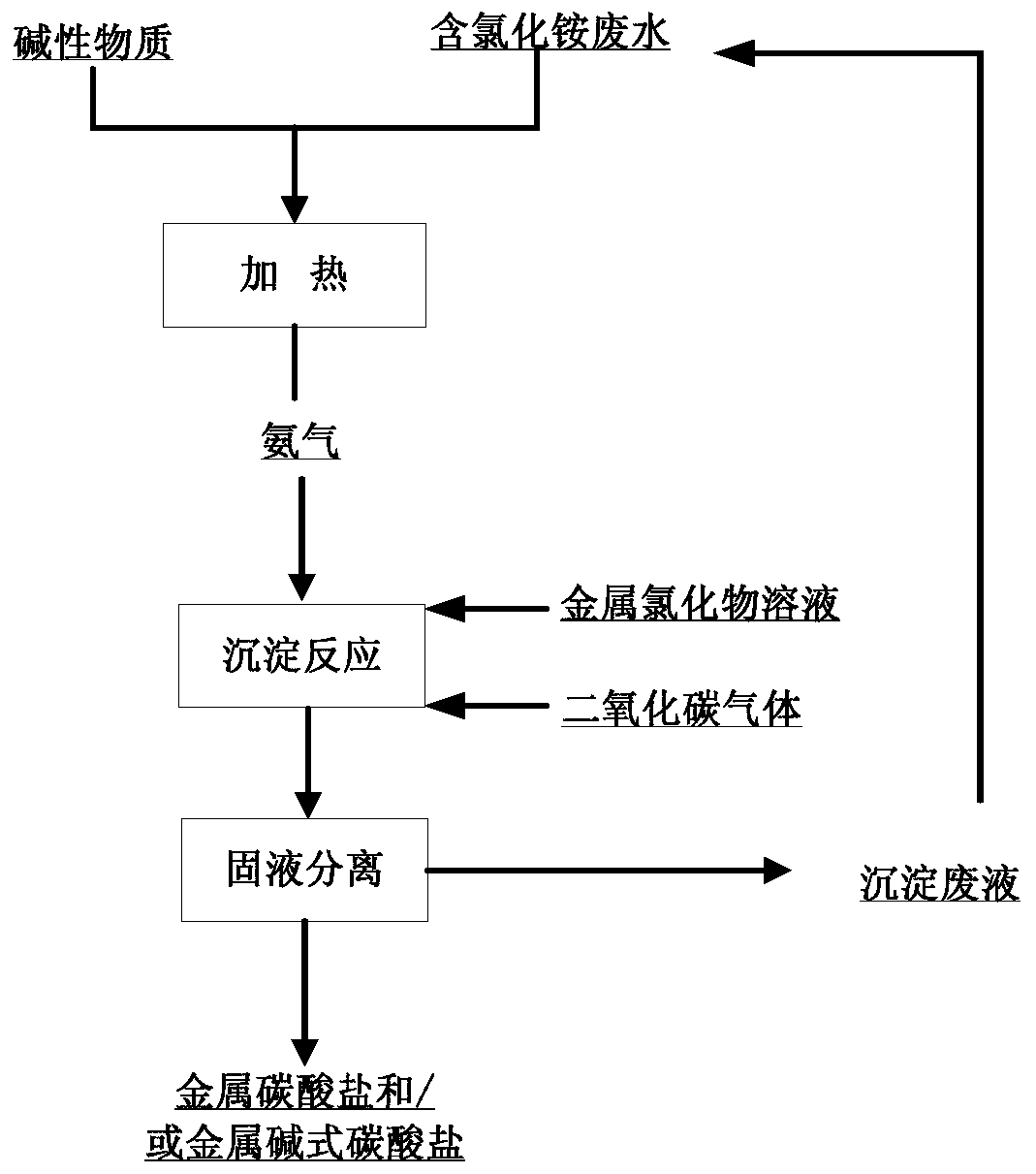
权利要求书
1.一种含氯化铵废水的回收利用工艺,其特征在于,所述工艺包括:
步骤S1,向所述含氯化铵废水中加入碱性物质形成浆液,并对所述浆液加热收集氨气;以及
步骤S2,利用所述氨气与二氧化碳气体对金属氯化物溶液进行沉淀反应,固液分离后得到金属碳酸盐和/或金属碱式碳酸盐以及沉淀废液;
其中,将所述沉淀废液返回所述步骤S1用作所述含氯化铵废水。
2.根据权利要求1所述的工艺,其特征在于,所述步骤S1包括:
步骤S11,用所述碱性物质将所述含氯化铵废水的pH值调节至3.0~6.0,得到固液混合物;
步骤S12,对所述固液混合物进行过滤,得到滤液;以及
步骤S13,在加热条件下,向所述滤液中继续加入所述碱性物质以收集所述氨气。
3.根据权利要求1所述的工艺,其特征在于,所述步骤S2包括:
将所述氨气和二氧化碳通入所述金属氯化物溶液中,并控制反应过程的pH值在2.0~10.0范围内,得到浆液;
对所述浆液进行固液分离,得到所述金属碳酸盐和/或金属碱式碳酸盐以及所述沉淀废液。
4.根据权利要求1至3中任一项所述的工艺,其特征在于,所述碱性物质为氢氧化钙、氧化钙、氧化镁、氢氧化镁、轻烧白云石、氢氧化钠、氢氧化钾中的一种或几种,优选所述碱性物质为氧化钙或氢氧化钠。
5.根据权利要求1至3中任一项所述的工艺,其特征在于,加入的所述碱性物质以OH-计,所述OH-的摩尔数与所述含氯化铵废水中的NH4+的摩尔数之比为1.02~1.5:1。
6.根据权利要求1至3中任一项所述的工艺,其特征在于,所述含氯化铵废水还包括金属冶炼分离及沉淀过程产生的含有钙和/或镁离子的氯化铵废水。
7.根据权利要求1至3中任一项所述的工艺,其特征在于,在所述步骤S1中向所述含氯化铵废水中加入所述碱性物质的过程中,还包括对所述含氯化铵废水进行加热的步骤,其中,所述加热的温度为70~98℃。
8.根据权利要求1至3中任一项所述的工艺,其特征在于,所述金属氯化物溶液包括碱金属氯化物溶液、碱土金属氯化物溶液、过渡金属氯化物溶液、氯化镓溶液、氯化锗溶液、氯化锡溶液以及氯化锑溶液中的任一种。
9.根据权利要求8所述的工艺,其特征在于,所述过渡金属氯化物为稀土氯化物、镍氯化物、钴氯化物、铜氯化物及锌氯化物中的任一种。
10.根据权利要求1所述的工艺,其特征在于,所述二氧化碳气体从金属碳酸盐生产工艺中的气体和/或、金属碳酸盐焙烧窑气和/或锅炉烟气中回收得到。
说明书
含氯化铵废水的回收利用工艺
技术领域
本发明涉及冶炼和工业环境保护技术领域,具体而言,涉及一种含氯化铵废水的回收利用工艺。
背景技术
冶炼分离生产过程中,通常采用碳酸氢铵沉淀法将各种金属的氯化物溶液制备成金属碳酸盐,制备过程中会产生大量氯化铵废水,尤其通过洗涤工艺会产生大量低浓度氯化铵废水。由于氯化铵废水中氨氮和氯离子的存在,其废水若直接排放,则会对水体产生严重污染。氨氮消耗水体的溶解氧,加速水体的富营养化过程;而且,氨氮还会在水中微生物作用下转变为硝态氮和亚硝态氮,对人体有毒害作用。另外,氯化铵的大量排放会对土壤氯离子浓度和pH值带来不良影响。
而碳酸氢氨沉淀工序中产生的含氯化铵的氨氮类废水,通常成分比较复杂,含有大量Ca、Mg、Fe、Al、Si等杂质离子,氨氮含量相对较低,处理相对困难。在工业含盐废水的循环回收处理的研究和应用上,目前研究较多的是采用电渗析、膜分离法、蒸发结晶法、离子交换法、化学沉淀法以及折点氯化法等。
其中,电渗析法和膜分离法都是基于膜上对氯化铵进行浓缩的方法,这些方法对废水水质要求苛刻,对钙含量较高的废水必须进行预处理,废水中复杂的金属阳离子易造成膜污染。
蒸发结晶方法是指含盐废水经蒸发浓缩,达到过饱和状态,使盐在废水中形成晶核,继而逐步生成晶状固体进而实现分离;此方法对设备的耐腐蚀性要求高、投资大、能耗高、运行费用高,因此一般只有处理氨氮浓度极高的废水才具有经济可行性。而且氯化铵市场饱和,大量回收的氯化铵堆积滞销。
离子交换法是采用对NH4+具有强的选择吸附能力的天然沸石对截留,从而去除水中的氨氮,当沸石交换容量饱和后,沸石需要频繁再生,造成操作困难。
化学沉淀法除氨氮是通过在废水中投加镁的化合物和磷酸或磷酸氢盐,生成磷酸铵镁沉淀;该工艺操作简便,但需要投加大量磷、镁药剂,增加了处理成本,且处理后产生弱碱性废水,虽然解决了氨氮问题,但没有解决废水达标排放和综合利用的实质性问题。
折点氯化法是将一定量的氯气或次氯酸钠加入到废水中,使氨氮被氧化为N2,从而达到去除氨氮的目的;该方法处理效率高,但由于处理成本较高,只适用于低浓度氨氮废水的深度处理。
目前,我国大部分冶炼企业由于废水处理技术水平及处理成本的限制面临着严重的环保压力。目前公布的处理氯化铵废水的专利多采用电渗析、膜分离法、蒸发结晶法、离子交换法等多种技术进行组合,一次性投资高、工艺流程长、操作复杂、运行费用较高;而且,其复杂的设备具有对废水水质要求严格等缺点,回收利用成本高,水难以全部回收利用,对含杂质离子复杂、含钙镁离子较高的氯化铵废水不太适用,因而在工业上的应用受到了限制。
因此,在含氯化铵废水的综合回收利用方面,仍需要对现有技术进行改进,以提供一种廉价、环保且处理后的废水能够进行循环利用的废水处理工艺。
发明内容
本发明的主要目的在于提供一种含氯化铵废水的回收利用工艺,以解决现有技术中的废水处理成本高且处理后的废水仍不满足环保要求的技术问题。
为了实现上述目的,根据本发明的一个方面,提供了一种含氯化铵废水的回收利用工艺,该工艺包括:步骤S1,向含氯化铵废水中加入碱性物质形成浆液,并对浆液加热收集氨气;以及步骤S2,利用氨气与二氧化碳气体对金属氯化物溶液进行沉淀反应,固液分离,得到金属碳酸盐和/或金属碱式碳酸盐以及沉淀废液;其中,将沉淀废液返回步骤S1用作含氯化铵废水。
进一步地,步骤S1包括:步骤S11,用碱性物质将含氯化铵的废水的pH值调节至3.0~6.0,得到固液混合物;步骤S12,对固液混合物进行过滤,得到滤液;以及步骤S13,在加热条件下,向滤液中继续加入碱性物质以收集氨气。
进一步地,步骤S2包括:将氨气和二氧化碳通入金属氯化物溶液中,并控制反应过程的pH值在2.0~10.0范围内,得到浆液;对浆液进行固液分离,得到金属碳酸盐和/或金属碱式碳酸盐以及沉淀废液。
进一步地,碱性物质为氢氧化钙、氧化钙、氧化镁、氢氧化镁、轻烧白云石、氢氧化钠、氢氧化钾中的一种或几种,优选碱性物质为氧化钙或氢氧化钠。
进一步地,加入的碱性物质以OH-计,OH-的摩尔数与含氯化铵废水中的NH4+的摩尔数之比为1.02~1.5:1。
进一步地,含氯化铵废水还包括金属冶炼分离及沉淀过程产生的含有钙和/或镁离子的氯化铵废水。
进一步地,在步骤S1中向含氯化铵废水中加入碱性物质的过程中,还包括对含氯化铵废水进行加热的步骤,其中,加热的温度为70~98℃。
进一步地,金属氯化物溶液包括碱金属氯化物溶液、碱土金属氯化物溶液、过渡金属氯化物溶液、氯化镓溶液、氯化锗溶液、氯化锡溶液以及氯化锑溶液中的任一种。
进一步地,过渡金属氯化物为稀土氯化物、镍氯化物、钴氯化物、铜氯化物及锌氯化物中的任一种。
进一步地,二氧化碳气体从金属碳酸盐生产工艺中的气体和/或、金属碳酸盐焙烧窑气和/或锅炉烟气中回收得到。
应用本发明的技术方案,向含氯化铵废水中加入碱性物质,利用碱性物质加入废水中产生的反应热和外加热使氨汽化,利用氨气与二氧化碳使得金属氯化物溶液发生沉淀反应得到金属碳酸盐和/或金属碱式碳酸盐产品,而产生的含氯化铵废水再次循环处理;产生氨气的同时产生的氯化物浆液可经固液分离后,对滤液和固体渣分别进行回收利用。本发明工艺流程短,将废水治理与金属冶炼分离工艺相结合,不但处理了复杂的氨氮废水,实现了氨的循环利用,而且获得了金属碳酸盐和/或金属碱式碳酸盐产品;此外,上述沉淀反应步骤中所用到的二氧化碳气体还可以充分利用金属碳酸盐生产工艺、金属碳酸盐焙烧工艺以及锅炉烟气中含有的二氧化碳气体,减少温室气体排放。