申请日2015.12.30
公开(公告)日2016.05.25
IPC分类号C02F3/30; C02F101/16
摘要
本发明公开了一种废水同步硝化反硝化脱氮的装置以及废水同步硝化反硝化脱氮方法。该装置和方法中所用的生物反应器在反应池空间中设置隔板,隔板上端作为溢流口,隔板底端连通,隔板两侧形成上升通道和下降通道,从而形成循环通道,在上升通道底部设置曝气系统,进入的废水经过曝气混合进行硝化反应,至少部分废水经过溢流口沿着下降通道下降,下降通道中设置玄武岩纤维填料,废水中的大量微生物易粘附在玄武岩纤维上生长使得硝化细菌和反硝化细菌在玄武岩纤维上富集,下降的废水到达反应池底部再曝气混合,通过隔板底部进入上升通道,以此进行高速循环处理。本发明装置和方法实现了硝化反硝化在同一反应池中的同步处理。
摘要附图
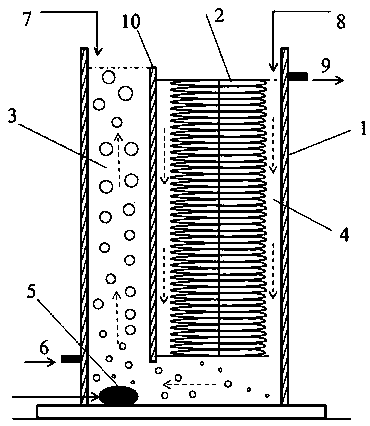
权利要求书
1.一种废水同步硝化反硝化脱氮装置,包括生物反应器,其特征在于,在生物反应器内的反应池空间中设置隔板,隔板上端作为溢流口,隔板底端连通,隔板两侧的反应池空间分别形成上升通道和下降通道,从而在生物反应器内形成循环通道,其中在上升通道底部设置曝气系统,废水进水口设置在上升通道底部,进入的废水经曝气与下降通道过来的水分混合,从而进行高效硝化反应,上升通道的废水经过溢流口一部分沿着下降通道下降,一部分经设置在反应池下降通道顶部的出水口流出;下降通道中设置玄武岩纤维填料,该填料全部浸没在废水中,玄武岩纤维填料由纤维束构成,该纤维束是以一定直径的玄武岩纤维单丝构成,废水中的大量微生物易粘附在玄武岩纤维上生长繁殖,使硝化细菌和反硝化细菌在玄武岩纤维上得以富集,下降通道的废水到达反应池底部,通过隔板底部与上升通道底部的进水充分混合上升,以此进行高速循环处理。
2.如权利要求1所述的废水同步硝化反硝化脱氮装置,其特征在于,所述玄武岩纤维填料采用纤维束垂直悬挂的方式,或者采用纤维束环绕固定芯材布置的方式构成。
3.如权利要求1所述的废水同步硝化反硝化脱氮装置,其特征在于,所述玄武岩纤维填料是固定在隔板上的下降通道一侧。
4.如权利要求1所述的废水同步硝化反硝化脱氮装置,其特征在于,玄武岩纤维填料单丝直径为10~20μm。
5.一种废水同步硝化反硝化脱氮方法,其特征在于,所述方法包括将废水输送入生物反应器的反应池中,其中所述反应池的空间中设置隔板,隔板上端作为溢流口,隔板底端连通,隔板两侧的反应池空间分别形成上升通道和下降通道,从而在生物反应器内形成循环通道;在上升通道底部设置曝气系统,废水进水口设置在上升通道底部,通过进水口进入的废水经过曝气与下降通道过来的水充分混合从而进行高效硝化反应,反应池的出水口设置在下降通道顶部,上升通道的废水经过溢流口一部分沿着下降通道下降,一部分经设置在反应池下降通道顶部的出水口流出;在下降通道中设置了玄武岩纤维填料,该填料全部浸没在废水中,玄武岩纤维填料由纤维束构成,该纤维束以一定直径的玄武岩纤维单丝构成,废水中的大量微生物易粘附在玄武岩纤维上生长繁殖,使硝化细菌和反硝化细菌在玄武岩纤维上得以富集,下降的废水经过富集有硝化细菌和反硝化细菌的玄武岩纤维,同时进行硝化和反硝化反应;废水在经过同步硝化反硝化处理后到达反应池底部,与上升通道底部的进水充分混合上升,以此进行高速循环处理。
6.如权利要求5所述的废水同步硝化反硝化脱氮方法,其特征在于,在曝气过程中,通过曝气系统控制使得反应器曝气区的溶解氧浓度为1.0~5.0mg/L。
7.如权利要求5所述的废水同步硝化反硝化脱氮方法,其特征在于,控制反应器的反应温度为20~35℃,pH值为6~9。
8.如权利要求5所述的废水同步硝化反硝化脱氮方法,其特征在于,控制反应器内游离的污泥浓度为2.0~6.0g/L,其中通过设置沉淀池污泥回流的方式保证反应器内污泥浓度的稳定,控制污泥回流比范围为50%~100%。
9.如权利要求5所述的废水同步硝化反硝化脱氮方法,其特征在于,待处理废水主要为金霉素废水,其氨氮浓度为280~470mg/L,总氮浓度为400~650mg/L,COD浓度为2000~3000mg/L。
10.如权利要求5所述的废水同步硝化反硝化脱氮方法,其特征在于,按照碳氮质量比为4:1~10:1补加所需有机碳源,有机碳源是甲醇、乙醇、乙酸钠、葡萄糖、面粉等中的一种。
说明书
一种废水同步硝化反硝化脱氮方法及装置
技术领域
本发明属于废水处理技术领域,具体涉及一种废水同步硝化反硝化脱氮方法及装置。
背景技术
随着经济的快速发展,化工、印染、医药等行业排放的废水量越来越大,且水质越来越复杂。特别是国内一些较大的发酵类制药企业,生产中产生的废水中包含发酵残余的培养基、丝菌体和发酵过程中产生的各种复杂的代谢产物,如碳水化合物、蛋白质、有机酸;还有提取过程中产生的有机溶媒、酸碱、硫酸盐和少量抗生素等。由于含有生物发酵代谢产生的生物难降解有机物质,以及少量对微生物具有毒害和抑制作用的抗生素,色度高,成分复杂,水质水量变化大,是一种难处理的高浓度有机废水。该类废水采用一般的物化预处理与生化结合或者仅有的生化处理极难达到处理效果,迫切需要开发经济有效的金霉素废水处理技术。
生物脱氮是一种较为成熟可靠的方法,负责脱氮的微生物主要是硝化菌和反硝化菌。在实际工程应用中,两种菌体的生长环境完全不同,因此一般都将硝化和反硝化过程分开,例如,目前大多数项目采用缺氧-好氧(A/O)工艺存在脱氮效果不好、污水处理装备占地面积大,投资运行成本高等缺点。
近几年,国内外逐渐有研究者将硝化菌和反硝化菌置于同一个反应器内混合培养,同步进行硝化反硝化反应,不仅能克服传统工艺的不足,提高脱氮效率,还能大大节省成本,因此同步硝化反硝化脱氮过程开始成为污水治理领域的热点。但是该过程结果不尽人意,实际工程应用尚待验证。国内进行了一些相关的研究工作,专利CN102050521B公开了一种同步硝化反硝化处理含氨污水的方法,首先培养脱氮颗粒污泥,然后以该脱氮颗粒污泥采用同步硝化反硝化过程处理含氨污水。这种方法对有机污染物的去除率较高,但是该方法需要首先驯化、培养硝化颗粒污泥,分离筛选好氧反硝化菌,再将二者混合制备脱氮颗粒污泥,前期实际操作过程较为复杂,在实际工程应用中存在放大难题。专利CN104609565A公开了一种含氨废水的同步硝化反硝化处理方法,该方法中需设置分离膜进行硝化、反硝化分区反应,能保证硝化、反硝化反应的各自有效发生,但是经过长时间运行,分离膜易被悬浮物堵塞,影响效果。
尽管目前同步硝化反硝化脱氮技术有了较大的突破,但依然存在去除率低,运行不稳定等缺点,且该技术针对高浓度的医药废水脱氮尚未有相关案例报道,并且大多现有的工艺都单单针对氨氮去除有效,总氮去除依然不理想,严重限制了该工艺的实际应用。因此,采取简单有效的措施保证硝化和反硝化同步高效且长期稳定地进行,对该工艺的工程应用十分重要。
发明内容
本发明的目的在于克服现有技术的缺点,提供一种硝化反硝化同步进行的废水处理装置和方法。
具体来说,本发明采用了以下技术方案:
一种废水同步硝化反硝化脱氮装置,包括生物反应器,其特征在于,在生物反应器内的反应池空间中设置隔板,隔板上端作为溢流口,隔板底端连通,隔板两侧的反应池空间分别形成上升通道和下降通道,从而在生物反应器内形成循环通道,其中在上升通道底部设置曝气系统,废水进水口设置在上升通道底部,进入的废水经曝气与下降通道过来的水分混合,从而进行高效硝化反应,上升通道的废水经过溢流口一部分沿着下降通道下降,一部分经设置在反应池下降通道顶部的出水口流出;下降通道中设置玄武岩纤维填料,该填料全部浸没在废水中。玄武岩纤维填料由纤维束构成,该纤维束是由一定直径的玄武岩纤维单丝构成,废水中的大量微生物易粘附在玄武岩纤维上生长繁殖,使硝化细菌和反硝化细菌在玄武岩纤维上得以富集,下降通道的废水到达反应池底部,通过隔板底部与上升通道底部的进水充分混合上升以此进行高速循环处理。
在上述装置中,所述玄武岩纤维填料采用纤维束垂直悬挂的方式,或者采用纤维束环绕固定芯材布置的方式构成。
优选地,所述玄武岩纤维填料是固定在隔板上的下降通道一侧。
本发明还公开了一种废水同步硝化反硝化脱氮方法,其特征在于,所述方法包括将废水输送入生物反应器的反应池中,其中所述反应池的空间中设置隔板,隔板上端作为溢流口,隔板底端连通,隔板两侧的反应池空间分别形成上升通道和下降通道,从而在生物反应器内形成循环通道;在上升通道底部设置曝气系统,废水进水口设置在上升通道底部,通过进水口进入的废水经过曝气与下降通道过来水充分混合从而进行高效硝化反应,反应池的出水口设置在下降通道顶部,上升通道的废水经过溢流口一部分沿着下降通道下降,一部分经设置在反应池下降通道顶部的出水口流出;在下降通道中悬挂了玄武岩纤维填料,该填料全部浸没在废水中。玄武岩纤维填料由纤维束构成,该纤维束是由一定直径的玄武岩纤维单丝构成,废水中的大量微生物易粘附在玄武岩纤维上生长繁殖,使硝化细菌和反硝化细菌在玄武岩纤维上得以富集,下降的废水经过富集有硝化细菌和反硝化菌的玄武岩纤维,同时进行硝化和反硝化反应;废水在经过同步硝化反硝化处理后到达反应池底部,与上升通道底部的进水充分混合上升,以此进行高速循环处理。
在以上装置和方法中,优选地,玄武岩纤维填料单丝直径为10~20μm。
优选地,在曝气过程中,通过曝气系统控制使得反应器曝气区的溶解氧浓度为1.0~5.0mg/L。
在另一优选方案中,控制反应器的反应温度为20~35℃,pH值为6~9。
另一方面,控制反应器内游离的污泥浓度为2.0~6.0g/L,其中通过设置沉淀池污泥回流的方式保证反应器内污泥浓度的稳定,控制污泥回流比范围为50%~100%。
作为一个优选实施方案,待处理废水的氨氮浓度为280~470mg/L,总氮浓度为400~650mg/L,COD浓度为2000~3000mg/L。
还优选,按照碳氮质量比为4:1~10:1补加所需有机碳源,有机碳源是甲醇、乙醇、乙酸钠、葡萄糖、面粉等中的一种。
与现有技术相比,本发明具有以下突出特点:
1、反应器中设置玄武岩纤维,活性污泥易粘附在玄武岩纤维上,纤维上的污泥长期聚集,反应器中设置了曝气装置使得污泥表面呈好氧状态,聚集大量的硝化菌,污泥内部因供氧不足呈厌氧或缺氧状态,富集反硝化细菌。因此,通过控制合适的溶氧量,反应器内同时进行硝化反应和反硝化反应,即同步硝化反硝化反应。硝化菌利用废水中的氨氮进行硝化反应,产生的硝氮或亚硝氮可以进入污泥内部作为反硝化菌的营养物质,将硝氮或亚硝氮转化成氮气。由于产物抑制作用的削减,有助于提高硝化反应的效果,硝化反硝化互相促进,实现了总氮的高效脱除。因此,与传统的脱氮工艺相比,硝化反应与反硝化作用可于同一个反应器中进行,降低了分设硝化池和反硝化池的复杂程度,缩减了设备的占地面积,节约了投资成本。此外,同步硝化反硝化可明显缩短水力停留时间,提高污水的处理效率,也大大提高了装置的运行效率。
2、硝化反应发生时会消耗碱度,所以通常需要添加碱液维持适宜硝化菌生长的环境,而当硝化反硝化同步在一个反应器进行时,反硝化反应会产生碱度,弥补部分硝化反应所需的碱度,减少外加碱液的消耗,节省运行成本。
3、反应器内填充的纤维材料呈束状,与污水的接触面积大。对于一般的废水而言,除了氨氮,还含有其他难以降解的悬浮物质,这些利用常规的生化法难以去除的物质可能随着废水的循环流动被吸附固定在玄武岩纤维上,可一定程度地降低剩余污泥的产生量。
4、反应器设置隔板,玄武岩纤维两端固定,挡板底端连通,上端作为溢流口,污水进入反应器在曝气的作用下充分流动混合,从通道上升至溢流口溢出,部分污水沿着通道下降,即在反应池内进行快速循环流动,活性污泥颗粒粒径比常规硝化池内得到的活性污泥粒径大,反应器内污水的黏度不会随着污泥浓度的升高而过分增大,使溶解氧得到有效利用。此外,这种高速流动不仅保证了硝化反应的高效率,而且还会引起玄武岩纤维的摇摆,当玄武岩纤维的微生物负荷过高时,表层部分富集硝化菌的污泥脱落,进入反应器曝气区,硝化细菌数量增加,从而提升了曝气区的硝化反应效率。