申请日2016.06.21
公开(公告)日2016.11.23
IPC分类号C01D7/12; C01D3/04; C01C1/16
摘要
本发明公开了一种提钒废水的后处理方法,该方法包括(1)向提钒废水中加入氯化钠至提钒废水相对于氯化钠饱和;后并加入氨水,通入二氧化碳反应;(2)将步骤(1)的反应液过滤,得到的第一废水和第一固体,所述第一固体烘干煅烧得到碳酸钠;(3)第一废水经蒸发浓缩得到NH3和含有固体氯化钠的固液混合物,该固液混合物经固液分离得到固体氯化钠和第二废水,所述NH3用于配制步骤(1)所述的氨水;(4)第二废水降温后得到含有氯化铵的固液混合物,该固液混合物经固液分离得到固体氯化铵和第三废水;所述第三废水返回步骤(1)中和提钒废水合并后循环使用。本发明不仅使提钒废水变废为宝,而且整个工艺绿色环保,回收效率高,不产生任何有害副产品。
摘要附图
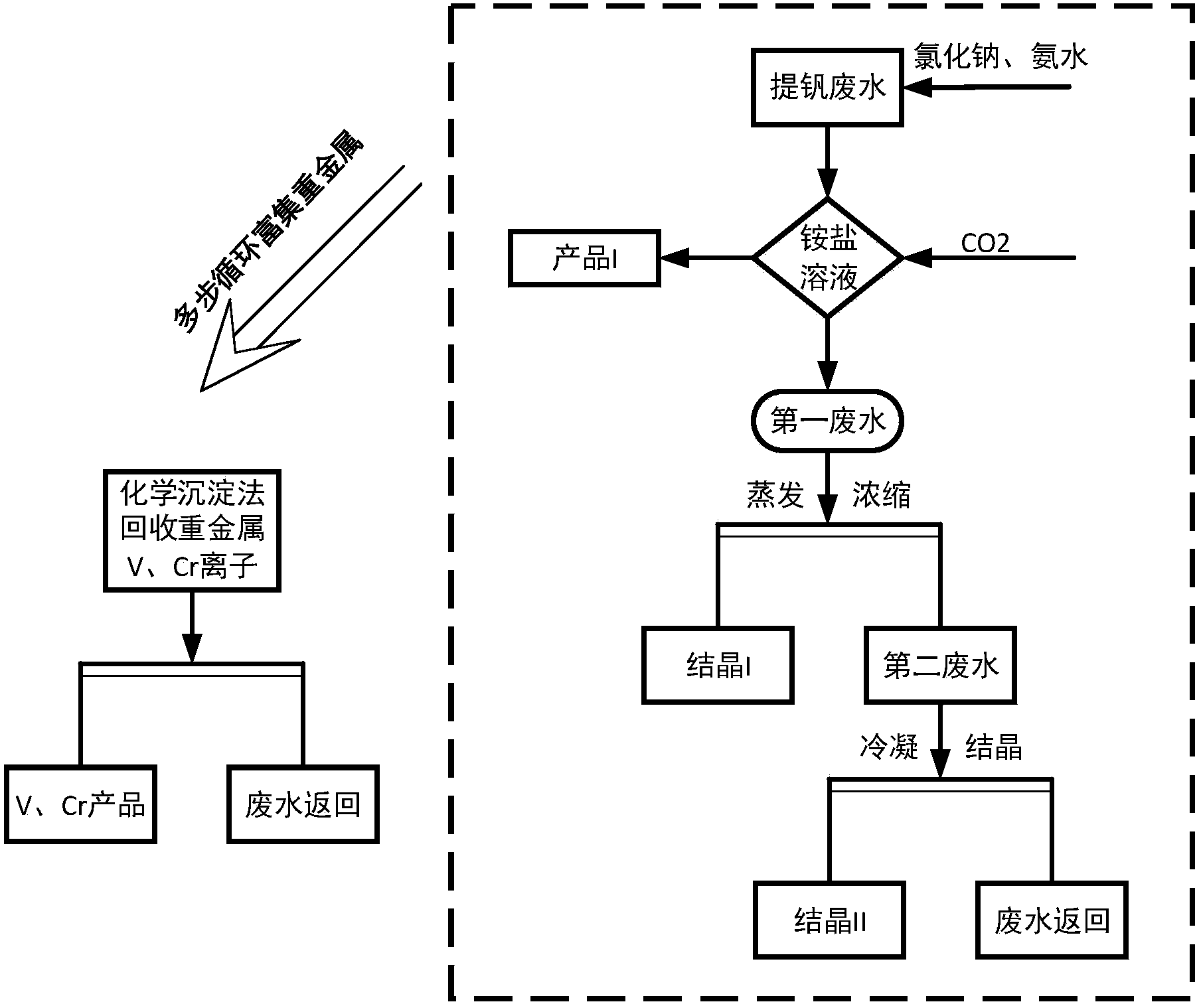
权利要求书
1.一种提钒废水的后处理方法,包括如下的步骤:
(1)向提钒废水中加入氯化钠至提钒废水相对于氯化钠饱和;后加入氨水得到铵盐溶液,后向铵盐溶液内通入二氧化碳;
(2)步骤(1)的反应液经过滤得到第一废水和第一固体,所述第一固体烘干煅烧得到碳酸钠。
2.根据权利要求1所述的方法,其特征在于,所述后处理方法进一步包括如下步骤:
(3)第一废水经蒸发浓缩得到NH3和含有固体氯化钠的固液混合物,该固液混合物经固液分离得到固体氯化钠和第二废水,所述NH3用于配制步骤(1)所述的氨水。
3.根据权利要求2所述的方法,其特征在于,所述后处理方法进一步包括如下步骤:
(4)第二废水降温后得到含有氯化铵的固液混合物,该固液混合物经固液分离得到固体氯化铵和第三废水;所述第三废水返回步骤(1)中和提钒废水合并后循环使用。
4.根据权利要求3所述的方法,其特征在于,所述第三废水或提钒废水中V浓度达到2-3g/L时或Cr浓度达到1-3g/L时,采用化学沉淀法沉淀V和Cr,得到相应的含有V或Cr的产品和第四废水,第四废水返回步骤(1)中和提钒废水合并后循环使用。
5.根据权利要求1所述的方法,其特征在于,步骤(1)中所述氨水的浓度为20%-30%,每升提钒废水中氨水添加量为0.1-0.2L。
6.根据权利要求1所述的方法,其特征在于,步骤(1)中所述二氧化碳通气量为40-200L/h。
7.根据权利要求1所述的方法,其特征在于,步骤(1)中所述反应时间为3-6h。
8.根据权利要求1所述的方法,其特征在于,步骤(2)中所述煅烧温度为160-180℃。
9.根据权利要求3所述的方法,其特征在于,步骤(4)中第二废水冷凝温度为0-10℃。
说明书
一种提钒废水的后处理方法
技术领域
本发明涉及提钒废水的资源化领域,特别涉及一种联碱法与化学沉淀法联合处理提钒废水并资源化利用的工艺方法。
背景技术
钒是一种重要的战略资源。我国是钒资源大国,其中石煤、粘土钒矿是我国特有的优势粘土钒矿资源,其约占国内总钒量的87%。目前,国内主要的提钒工艺有钠化焙烧法、钙化焙烧法、无盐焙烧法和直接湿法浸出法。其中,钠化焙烧法因其工艺简单,钒转化率高,而被国内外普遍采用。但此工艺方法后续提钒工艺会产生大量废水,废水中含有高浓度的钠盐、氨氮及重金属V、Cr等,造成资源浪费及环境污染。研究粘土钒矿钠化焙烧废水处理的工艺,对当前粘土钒矿提钒工业具有重大的现实意义,也是实现粘土钒矿提钒工业清洁生产及可持续发展的必由之路。
目前处理粘土钒矿钠化焙烧提钒废水常规方法有物理吸附法、化学沉淀法、离子交换法和生物处理法等方法,但是这些方法大多存在着药剂成本高,运行成本高,处理后渣量大,对设备腐蚀程度大,回收利用成本高且不能完全回收利用等缺点。因此,如何高效率、低成本、绿色环保地处理粘土钒矿提钒废水,使提钒废水达到全面资源化利用,对钒业的可持续发展具有深远的意义。
发明内容
本发明目的主要是提供一种提钒废水资源化利用的工艺方法,达到废水污染物零排放,并克服现有提钒废水处理方法成本高,废水难以利用等问题,提供一种高效率、低成本、绿色处理提钒废水的工艺方法。
本发明提供的一种提钒废水资源化利用的工艺方法,包括如下的步骤:
(1)向提钒废水中加入氯化钠至提钒废水相对于氯化钠饱和;后并加入氨水,并通入二氧化碳反应得到铵盐溶液,后向铵盐溶液内通入二氧化碳;
(2)将步骤(1)的反应液经过滤,得到的第一废水和第一固体,所述第一固体烘干煅烧得到碳酸钠。
通过上述的步骤可以回收提钒废水中的钠盐。
优选的,所述提钒废水中包括Na+1.0-10.0g/L,K+0.5-2.0g/L,Ca 0.1-0.5g/L,Cl-10-100g/L,NH4+3-50g/L。
优选的,所述方法进一步包括如下的步骤:
(3)第一废水经蒸发浓缩得到NH3和含有固体氯化钠的固液混合物,该固液混合物经固液分离得到固体氯化钠和第二废水,所述NH3用于配制步骤(1)所述的氨水。
通过上述的步骤可以实现氯化钠以及氨的回收利用。
优选的,所述方法进一步包括:
(4)第二废水降温后得到含有氯化铵的固液混合物,该固液混合物经固液分离得到固体氯化铵和第三废水;所述第三废水返回步骤(1)中和提钒废水合并后循环使用。
通过上述的步骤可以实现氯化铵的回收利用以及金属离子的富集。
优选的,所述第三废水或提钒废水中V浓度达到2-3g/L时或Cr浓度达到1-3g/L时,采用化学沉淀法沉淀V或Cr,得到相应的含有V或Cr的产品和第四废水,第四废水返回步骤(1)中和提钒废水合并后循环使用。
优选的,所述第三废水或提钒废水中V浓度达到2-3g/L时,采用铵盐沉钒法回收V得到V2O5。
优选的,所述第三废水或提钒废水中Cr浓度达到1-3g/L时,采用水合肼化学沉淀法回收Cr得到Cr2(SO4)3。
优选的,步骤(1)中氨水的浓度为20%-30%,每升提钒废水中氨水添加量为0.1-0.2L。
优选的,步骤(1)中二氧化碳通气量为40-200L/h。
优选的,步骤(1)中反应时间为3-6h。
优选的,步骤(2)中煅烧温度为440-500℃。
优选的,步骤(3)中废水作为提钒焙烧烟气冷却循环水并利用烟气热量蒸发浓缩。
优选的,所述步骤(4)中第二废水冷凝温度为0-10℃。
本发明利用联碱法处理钠盐,氨氮废水,利用提钒焙烧尾气热量浓缩废水,采用热法回收钠盐及铵盐,通过多次循环浓缩的废水使重金属离子V、Cr富集,提高了废水中重金属离子V,Cr的浓度,可降低回收成本。
本发明采用铵盐沉钒及水合肼法回收铬可以获得产品纯度高的产品,且回收工艺不产生新的盐干扰全流程,回收重金属V、Cr后的废水可返回作为初始原料。本发明工艺简单,工艺连续性好,废水污染物零排放,绿色环保,应用前景广阔。