申请日2017.01.23
公开(公告)日2017.06.13
IPC分类号C02F9/14
摘要
一种VB12废水零排放处理系统,包括与VB12废水管道依次相连的调节池、混凝沉淀池、第一输料泵、IC厌氧塔;所述的IC厌氧塔的产水口通过管道连接超滤进水罐、第二输料泵、管式超滤膜组件;所述的管式超滤膜组件的产水口通过管道连接超滤产水罐、第一增压泵、纳滤膜组件;纳滤膜组件的产水出口通过管道连接纳滤产水罐、第二增压泵、反渗透膜组件;所述的反渗透膜组件的浓水出口通过管道连接反渗透浓水罐、第三输料泵、MVR装置。本发明还包括一种VB12废水零排放处理系统处理工艺。本发明所述的VB12废水零排放处理系统及处理工艺,用于VB12废水处理,具体占地面积小、处理成本低、系统运行稳定和产水满足回用要求等优点。
摘要附图
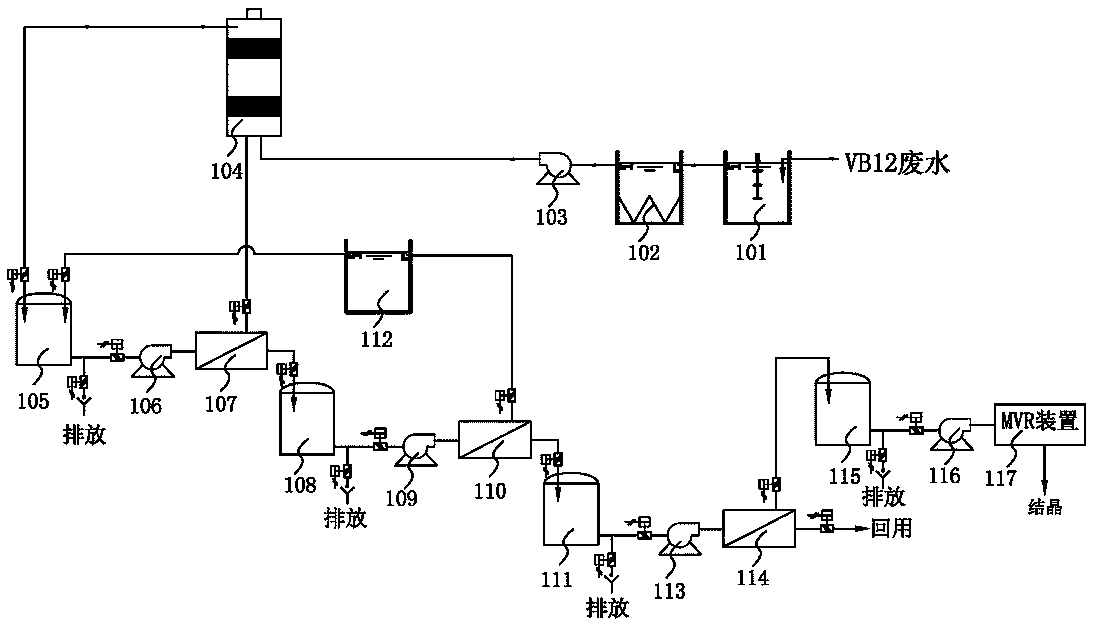
权利要求书
1.一种VB12废水零排放处理系统,其特征在于:包括与VB12废水管道相连的调节池,所述的调节池的出水口通过管道连接混凝沉淀池的进水口;混凝沉淀池的出水口通过管道连接第一输料泵的进水口;所述的第一输料泵的出水口通过管道连接IC厌氧塔进水口;所述的IC厌氧塔的产水口通过管道连接超滤进水罐进水口;所述的超滤进水罐的出水口过管道连接第二输料泵的进水口;所述的第二输料泵的出水口通过管道连接管式超滤膜组件的进水口;所述的管式超滤膜组件的产水口通过管道连接超滤产水罐的进水口;所述的超滤产水罐的出水口通过管道连接第一增压泵的进水口;所述的第一增压泵的出水口连接纳滤膜组件的进水口;所述的纳滤膜组件的产水出口通过管道连接纳滤产水罐的进水口;所述的纳滤产水罐的出水口通过管道连接第二增压泵的进水口;所述的第二增压泵的出水口通过管道连接反渗透膜组件的进水口;所述的反渗透膜组件的浓水出口通过管道连接反渗透浓水罐的进水口;所述的反渗透浓水罐的出水口通过管道连接第三输料泵进水口;所述的第三输料泵的出水口通过管道连接MVR装置的进水口;所述的管式超滤膜组件中的管式超滤膜截留分子量为1-25万道尔顿;所述的纳滤膜组件为耐压范围为0-100bar,具有梯形流道结构、耐高压有机纳滤膜组件;纳滤膜截留分子量为150-350道尔顿;所述的反渗透膜组件为耐压范围为0-90bar的耐高压有机反渗透膜组件。
2.根据权利要求1所述的一种VB12废水零排放处理系统,其特征在于:所述的纳滤膜组件的浓水出口通过管道连接A/O好氧池的进水口,所述的A/0好氧池的产水出口通过管道连接超滤进水罐的进水口。
3.根据权利要求1所述的一种VB12废水零排放处理系统,其特征在于:所述的管式超滤膜组件的浓水出口连接IC厌氧塔进水口。
4.根据权利要求1所述的一种VB12废水零排放处理系统,其特征在于:所述的管式超滤膜组件的德国MEMOS公司产的具有开放式错流流道、自支撑可更换膜壳管式超滤膜组件。
5.一种VB12废水零排放处理系统处理工艺,其特征在于,包括如下步骤:
步骤1:VB12废水通过废水管道排入调节池,通过调节池进行水量水质调节后,进入混凝沉淀池混凝沉淀;
步骤2:混凝沉淀产水进入IC厌氧塔中,进行厌氧反应,去除水体中的COD;
步骤3:IC厌氧塔的产水进行管式超滤膜过滤,通过管式超滤膜截留去除固体颗粒和悬浮物,得管式超滤产水和管式超滤浓水,所述的管式超滤膜组件中的管式超滤膜截留分子量为1-25万道尔顿;
步骤4:管式超滤产水进行纳滤过滤进行高倍浓缩,得纳滤产水和纳滤浓水;所述的纳滤过滤采用耐压范围为0-90bar的耐高压有机纳滤膜组件,纳滤膜截留分子量为150-350道尔顿,运行压力70-80bar,浓缩8-10倍;
步骤5:纳滤产水进行反渗透高倍浓缩,得反渗透产水和反渗透浓水;所述的反渗透浓缩采用的反渗透膜组件为耐压范围为0-90bar的耐高压有机反渗透膜组件,运行压力为70-80bar,浓缩8-10倍;
步骤6:反渗透产水回用,反渗透浓水则通过MVR装置蒸发浓缩后结晶成盐。
6.根据权利要求5所述的一种VB12废水零排放处理系统处理工艺,其特征在于,还包括将管式超滤浓水回流至IC厌氧塔中,补充IC厌氧中流水的活性污泥的步骤。
7.根据权利要求5所述的一种VB12废水零排放处理系统处理工艺,其特征在于,还包括将纳滤浓水通过A/O好氧反应,降低废水中的COD、氨氮、总氮,A/O好氧反应后的产水回流至超滤过滤中进行处理的步骤。
8.根据权利要求5所述的一种VB12废水零排放处理系统处理工艺,其特征在于,所述的管式超滤膜组件采用德国MEMOS公司产的具有开放式错流流道、自支撑可更换膜壳管式超滤膜组件。
说明书
一种VB12废水零排放处理系统及处理工艺
技术领域
本发明涉及VB12废水处理领域,特别涉及一种VB12废水零排放处理系统及处理工艺。
背景技术
维生素B12,简称VB12,我国是VB12生产大国,华北制药集团、石药集团、河北玉峰集团、宁夏多维药业等均是VB12生产企业。VB12生产过程中会产生大量废水,废水中含有培养基残渣、大分子蛋白、酮类、丙酸、二甲基苯并咪唑等难降解物质。
近年来,随着VB12清洁生产工艺水平的提升,废水中所含污染物的浓度增加,处理难度越来越大,处理要求越来越高,此外新上VB12项目的规模也越来越大,废水处理工程投资和占地显著增大,处理成本成倍增加,找到一条更为合理的废水处理及回用路线成为企业的重要目标。
发明内容
针对上述问题,本发明的目的在于提供一种具有处理成本低、占地面积小、产水可以回用的VB12废水零排放处理系统及处理工艺。
为达到上述目的,本发明所提出的技术方案为:一种VB12废水零排放处理系统,其特征在于:包括与VB12废水管道相连的调节池,所述的调节池的出水口通过管道连接混凝沉淀池的进水口;混凝沉淀池的出水口通过管道连接第一输料泵的进水口;所述的第一输料泵的出水口通过管道连接IC厌氧塔进水口;所述的IC厌氧塔的产水口通过管道连接超滤进水罐进水口;所述的超滤进水罐的出水口过管道连接第二输料泵的进水口;所述的第二输料泵的出水口通过管道连接管式超滤膜组件的进水口;所述的管式超滤膜组件的产水口通过管道连接超滤产水罐的进水口;所述的超滤产水罐的出水口通过管道连接第一增压泵的进水口;所述的第一增压泵的出水口连接纳滤膜组件的进水口;所述的纳滤膜组件的产水出口通过管道连接纳滤产水罐的进水口;所述的纳滤产水罐的出水口通过管道连接第二增压泵的进水口;所述的第二增压泵的出水口通过管道连接反渗透膜组件的进水口;所述的反渗透膜组件的浓水出口通过管道连接反渗透浓水罐的进水口;所述的反渗透浓水罐的出水口通过管道连接第三输料泵进水口;所述的第三输料泵的出水口通过管道连接MVR装置(机械式蒸汽再压缩装置)的进水口;所述的管式超滤膜组件中的管式超滤膜截留分子量为1-25万道尔顿;所述的纳滤膜组件为耐压范围为0-90bar的耐高压有机纳滤膜组件;纳滤膜截留分子量为150-350道尔顿;所述的反渗透膜组件为耐压范围为0-90bar的耐高压有机反渗透膜组件。
进一步的,所述的纳滤膜组件的浓水出口通过管道连接A/O好氧池的进水口,所述的A/0好氧池的产水出口通过管道连接超滤进水罐的进水口。
进一步的,所述的管式超滤膜组件的浓水出口连接IC厌氧塔进水口。
优选的,所述的管式超滤膜组件的德国MEMOS公司产的具有开放式错流流道、自支撑可更换膜壳管式超滤膜组件,可以有效防止膜管被堵塞,并且具有产水量大、通量稳定、清洗周期长,可以两个月清洗一次。
本发明还包括一种VB12废水零排放处理系统处理工艺,其特征在于,包括如下步骤:
步骤1:VB12废水通过废水管道排入调节池,通过调节池进行水量水质调节后,进入混凝沉淀池混凝沉淀;
步骤2:混凝沉淀产水进入IC厌氧塔中,进行厌氧反应,去除水体中的COD;
步骤3:IC厌氧塔的产水进行管式超滤膜过滤,通过管式超滤膜截留去除固体颗粒和悬浮物,得管式超滤产水和管式超滤浓水,所述的管式超滤膜组件中的管式超滤膜截留分子量为1-25万道尔顿;
步骤4:管式超滤产水进行纳滤过滤进行高倍浓缩,得纳滤产水和纳滤浓水;所述的纳滤过滤采用耐压范围为0-90bar的耐高压有机纳滤膜组件,纳滤膜截留分子量为150-350道尔顿,运行压力70-80bar,浓缩8-10倍;
步骤5:纳滤产水进行反渗透高倍浓缩,得反渗透产水和反渗透浓水;所述的反渗透浓缩采用的反渗透膜组件为耐压范围为0-90bar的耐高压有机反渗透膜组件,运行压力为70-80bar,浓缩8-10倍;
步骤6:反渗透产水回用,反渗透浓水则通过MVR装置蒸发浓缩后结晶成盐。
进一步的,还包括将管式超滤浓水回流至IC厌氧塔中,补充IC厌氧中流水的活性污泥的步骤。
进一步的,还包括将纳滤产水通过A/O好氧反应,降低废水中的COD、氨氮、总氮,A/O好氧反应后的产水回流至超滤过滤中进行处理的步骤。
优选的,所述的管式超滤膜组件采用德国MEMOS公司产的具有具有开放式错流流道、自支撑可更换膜壳管式超滤膜组件,可以防止膜管被堵塞,并且具有产水量大、通量稳定、清洗周期长,可以两个月清洗一次。
采用上述技术方案,本发明所述的VB12废水零排放处理系统及处理工艺,用于VB12废水处理,具体下述优点:
1)大大减少废水处理设施用地,节约土建投入;
2)废水中的无机盐经纳滤、反渗透高倍浓缩后,通过MVR装置结晶,有效降低了能源消耗、降低了处理成本;
3)IC厌氧反应和组合膜分离浓缩系统的配合,大大提高了系统的抗冲击负荷能力,有利于整体系统的稳定运行;
4)反渗透产水的排放水可稳定达到回用标准。