申请日2014.06.12
公开(公告)日2014.10.22
IPC分类号C02F3/34
摘要
一种浮泥自动破碎循环的自养脱氮颗粒污泥反应器,包括反应器本体和和外部控制装置,反应器本体自下而上设有排泥布水单元、反应单元、浮泥破碎单元、碎泥收集单元、碎泥循环单元和出水单元,排泥布水单元设有进水口、曝气头和排泥口;浮泥破碎单元包括气体收集室、喷射管和挡板;碎泥循环单元设有导流隔板、降流管;出水单元包括溢流孔、设置在碎泥循环单元外圈的出水槽、与外界连通的出水口;外部控制装置包括液位继电器和控制阀。本发明的有益效果是:利用曝气余气和自养脱氮产气蕴含的能量来脱除上浮颗粒污泥表面的气泡,破除颗粒污泥内部气囊;实现了上浮颗粒污泥的“收集-破碎-沉降-返回”多重功能。
摘要附图
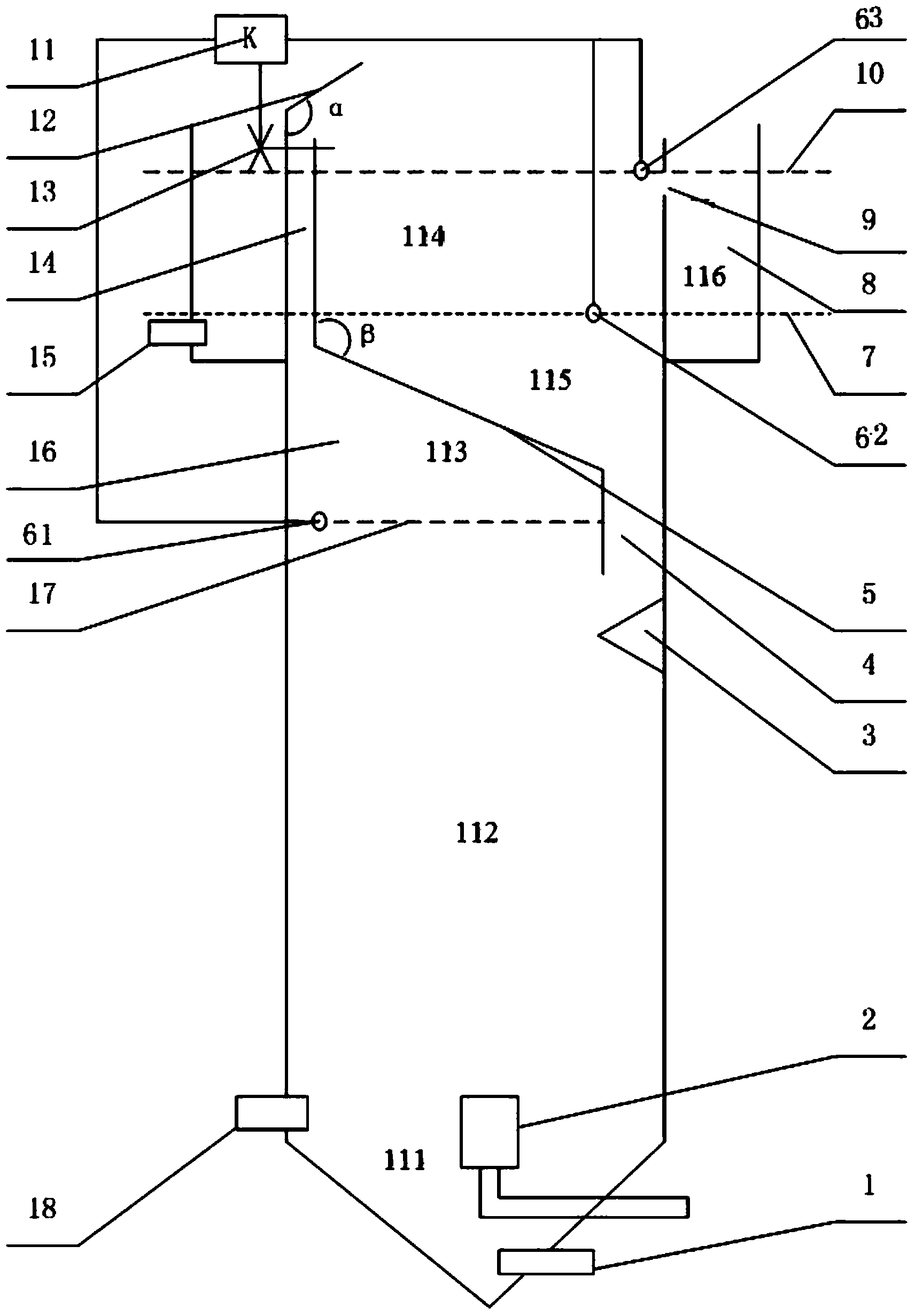
权利要求书
1.一种浮泥自动破碎循环的自养脱氮颗粒污泥反应器,其特征 在于:包括反应器本体和和外部控制装置,所述的反应器本体自下而 上设有排泥布水单元、反应单元、浮泥破碎单元、碎泥收集单元、碎 泥循环单元和出水单元,所述的排泥布水单元设有进水口、曝气头和 排泥口,所述的进水口和所述的排泥口设置在反应器本体的底部,所 述的曝气头的出气口指向反应器本体的内部;所述的浮泥破碎单元包 括气体收集室、喷射管和挡板,所述的喷射管设置在所述的气体收集 室内,并且所述的喷射管的下端进口与浮泥破碎单元连通、上端出口 连有挡板;所述的碎泥循环单元设有导流隔板、降流管,所述的降流 管的上端进口与碎泥循环单元连通、下端出口与反应单元连通;所述 的浮泥破碎单元与碎泥收集单元之间通过导流隔板隔开;所述的出水 单元包括溢流孔、设置在碎泥循环单元外圈的出水槽、与外界连通的 出水口,所述的溢流孔位于所述的出水单元的上端,并且所述的溢流 孔与所述的碎泥循环单元连通;所述的外部控制装置包括液位继电器 和控制阀,所述的液位继电器的三个端点分别处于浮泥破碎单元与反 应单元之间的液面、碎泥收集单元和碎泥循环单元之间的液面、出水 单元最高处液面位置,并与控制阀相连。
2.如权利要求1所述的一种浮泥自动破碎循环的自养脱氮颗粒 污泥反应器,其特征在于:包所述的反应器本体呈圆柱状,高径比 为3~4:1。
3.如权利要求2所述的一种浮泥自动破碎循环的自养脱氮颗粒 污泥反应器,其特征在于:所述的降流管的下端出口正下方的反应器 内侧壁上设有锥形导流板。
4.如权利要求3所述的一种浮泥自动破碎循环的自养脱氮颗粒 污泥反应器,其特征在于:所述的浮泥破碎单元和碎泥循环单元与碎 泥收集单元的高度比为2:1,三单元的体积比为1:1:1。
5.如权利要求4所述的一种浮泥自动破碎循环的自养脱氮颗粒 污泥反应器,其特征在于:所述的喷射管的直径为0.2~0.5cm,喷射 管长度与反应器本体高度比为1:5~7,并高于出水单元最高处液面的 长度为2~5cm。
6.如权利要求5所述的一种浮泥自动破碎循环的自养脱氮颗粒 污泥反应器,其特征在于:所述的降流管与喷射管的直径比为8~10:1, 降流管长度与反应器本体高度比为1:8~10,并低于浮泥破碎单元与反 应单元之间的液面的长度为3~5cm。
7.如权利要求3所述的一种浮泥自动破碎循环的自养脱氮颗粒 污泥反应器,其特征在于:所述的降流管下端设有锥形导流板,降流 管与锥形导流板之间的距离为3~5cm。
8.如权利要求7所述的一种浮泥自动破碎循环的自养脱氮颗粒 污泥反应器,其特征在于:所述的溢流孔上沿与出水单元最高处液面 等高,并且溢流孔的满孔流量等于进水口的满孔流量。
9.如权利要求1所述的一种浮泥自动破碎循环的自养脱氮颗粒 污泥反应器,其特征在于:所述的导流隔板的竖直夹角β为135°。
10.如权利要求1所述的一种浮泥自动破碎循环的自养脱氮颗粒 污泥反应器,其特征在于:所述的挡板与喷射管之间的夹角α为 120~135°。
说明书
一种浮泥自动破碎循环的自养脱氮颗粒污泥反应器
技术领域
本发明涉及一种浮泥自动破碎循环的自养脱氮颗粒污泥反应器。
背景技术
近年来含氨废水过量排放,造成了水体富营养化等一系列生态环 境问题。含氨废水的高效低耗处理一直是污水处理领域的难题。
一体式全程自养脱氮工艺(式(1))具有无需外加有机碳源、脱 氮负荷高、基建成本低,结构紧凑,装置运行和控制简单等优点,并 且能有效避免由于亚硝酸盐累积造成的抑制。
NH3+0.85O2→0.11NO3-+0.44N2+1.43H2O+0.14H+ (1)
但是目前的全程自养脱氮反应器常存有严重的颗粒污泥上浮问 题,这会导致厌氧氨氧化菌大量流失,且污泥流失后难以收集。反应 器内菌体不能有效持留会直接影响其脱氮性能,不利于反应器潜能的 发挥和工艺的长期稳定运行,这是目前高效全程自养脱氮反应器工业 化应用的一个瓶颈。
发明内容
本发明所述的一种浮泥自动破碎循环的自养脱氮颗粒污泥反应 器,其特征在于:包括反应器本体和和外部控制装置,所述的反应器 本体自下而上设有排泥布水单元、反应单元、浮泥破碎单元、碎泥收 集单元、碎泥循环单元和出水单元,所述的排泥布水单元设有进水口、 曝气头和排泥口,所述的进水口和所述的排泥口设置在反应器本体的 底部,所述的曝气头的出气口指向反应器本体的内部;所述的浮泥破 碎单元包括气体收集室、喷射管和挡板,所述的喷射管设置在所述的 气体收集室内,并且所述的喷射管的下端进口与浮泥破碎单元连通、 上端出口连有挡板;所述的碎泥循环单元设有导流隔板、降流管,所 述的降流管的上端进口与碎泥循环单元连通、下端出口与反应单元连 通;所述的浮泥破碎单元与碎泥收集单元之间通过导流隔板隔开;所 述的出水单元包括溢流孔、设置在碎泥循环单元外圈的出水槽、与外 界连通的出水口,所述的溢流孔位于所述的出水单元的上端,并且所 述的溢流孔与所述的碎泥循环单元连通;所述的外部控制装置包括液 位继电器和控制阀,所述的液位继电器的三个端点分别处于浮泥破碎 单元与反应单元之间的液面、碎泥收集单元和碎泥循环单元之间的液 面、出水单元最高处液面位置,并与控制阀相连。
进一步,所述的反应器本体呈圆柱状,高径比为3~4:1。
进一步,,所述的降流管的下端出口正下方的反应器内侧壁上设 有锥形导流板。
进一步,所述的浮泥破碎单元和碎泥循环单元与碎泥收集单元的 高度比为2:1,三单元的体积比为1:1:1。
进一步,所述的喷射管的直径为0.2~0.5cm,喷射管长度与反应 器本体高度比为1:5~7,并高于出水单元最高处液面的长度为2~5cm。
进一步,所述的降流管与喷射管的直径比为8~10:1,降流管长度 与反应器本体高度比为1:8~10,并低于浮泥破碎单元与反应单元之间 的液面的长度为3~5cm。
进一步,所述的降流管下端设有锥形导流板,降流管与锥形导流 板之间的距离为3~5cm。
进一步,所述的溢流孔上沿与出水单元最高处液面等高,并且溢 流孔的满孔流量等于进水口的满孔流量。
进一步,所述的导流隔板的竖直夹角β为135°。
进一步,所述的挡板与喷射管之间的夹角α为120~135°。
针对这些问题,本发明提出了一种浮泥自动破碎循环的自养脱氮 颗粒污泥反应器。巧妙利用曝气余气和自养脱氮产气蕴含的能量来脱 除上浮颗粒污泥表面的气泡,破除颗粒污泥内部气囊,恢复上浮颗粒 污泥的沉降性能并将其返回到反应区。在一个反应装置内实现了上浮 颗粒污泥的“收集-破碎-沉降-返回”多重功能,保证了反应器的高效脱 氮性能。
本发明所述的一种浮泥自动破碎循环的自养脱氮颗粒污泥反应 器可用PVC板或钢板制作,其运行方式如下:含氨氮废水经进水口 进入反应器,经曝气头引入空气充氧,废水中的部分NH4+由颗粒污 泥表面的亚硝酸细菌转化为NO2-,产生的NO2-随后与残留的NH4+由 颗粒污泥内部的厌氧氨氧化菌转化为N2。曝气余气和反应产生的N2上升经导流隔板下缘收集。控制阀处于关闭状态,使气体在集气室中 不断聚集,导致浮泥破碎单元与反应单元之间的液面不断下降。反应 后的废水经降流管流入碎泥循环单元,碎泥收集单元和碎泥循环单元 之间的液面不断上升淹没整个碎泥收集单元,澄清出水从溢流孔流入 出水槽中,然后从出水口流出反应器。液面不断下降,直到液位继电 器端点A脱离水面,此时碎泥收集单元和碎泥循环单元之间的液面 上升至出水单元最高处液面位置,浸没液位继电器端点C,液位继电 器工作,控制阀打开。由于浮泥破碎单元与反应单元之间的液面与大 气存在较大压差,浮泥破碎单元与反应单元之间的液面快速上升,将 上浮颗粒污泥带到喷射管下端口。通过反应区与喷射管横截面的急剧 变化,产生高速液流从喷射管上端口喷出,液流在通过喷射管时形成 强大的剪切力,脱除上浮颗粒污泥表面的气泡。上浮颗粒污泥随高速 液流撞击挡板,对颗粒污泥内部的气囊产生巨大的瞬时挤压,污泥破 碎落入碎泥收集单元中。沉降至导流隔板上缘,随下降废水经降流管 回到反应单元中。此时出水单元最高处液面下降至碎泥收集单元和碎 泥循环单元之间的液面处,液位继电器端点B脱离水面,液位继电 器工作,控制阀关闭。以此往复,在一个反应装置内成功实现了上浮 颗粒污泥的“收集-破碎-沉降-返回”的自动循环,无需外加动力。剩余 污泥从排泥口排出反应器。
本发明专利的优点主要体现在:①巧妙利用曝气余气和自养脱氮 产气蕴含的能量来脱除上浮颗粒污泥表面的气泡,破除颗粒污泥内部 气囊,无需外源动力,节能经济;②恢复上浮颗粒污泥的沉降性能的 同时能使破碎后的污泥返回到反应区中,有效持留菌体,保证高效脱 氮性能;③利用液位继电器联合控制阀的设计,在一个反应装置内成 功实现了上浮颗粒污泥的“收集-破碎-沉降-返回”自动循环,而且成本 低。