申请日2015.03.31
公开(公告)日2016.11.23
IPC分类号C02F9/04
摘要
本发明提供了一种煤化工废水中酚油联合脱除系统及处理工艺,其包括除油系统、萃取系统、反萃系统和净化系统及其相应的工艺过程。其中萃取过程包括如下步骤:(1)萃取焦油,废弃物焦油得以回收利用;(2)萃取脱酚,废水苯酚去除率达99.7%以上;(3)中间层的回收利用。萃取剂、酚类得以充分回收利用,避免废水二次污染。本发明提供的煤化工废水处理系统及其处理工艺能同步脱除、回收废水中废弃物焦油和苯酚,实现萃取剂最大程度的循环利用。本发明对工厂原设备改动小、成本低,运行稳定,处理后出水总酚去除率大于94%,COD去除率大于98%,满足污水后续蒸氨处理要求。
摘要附图
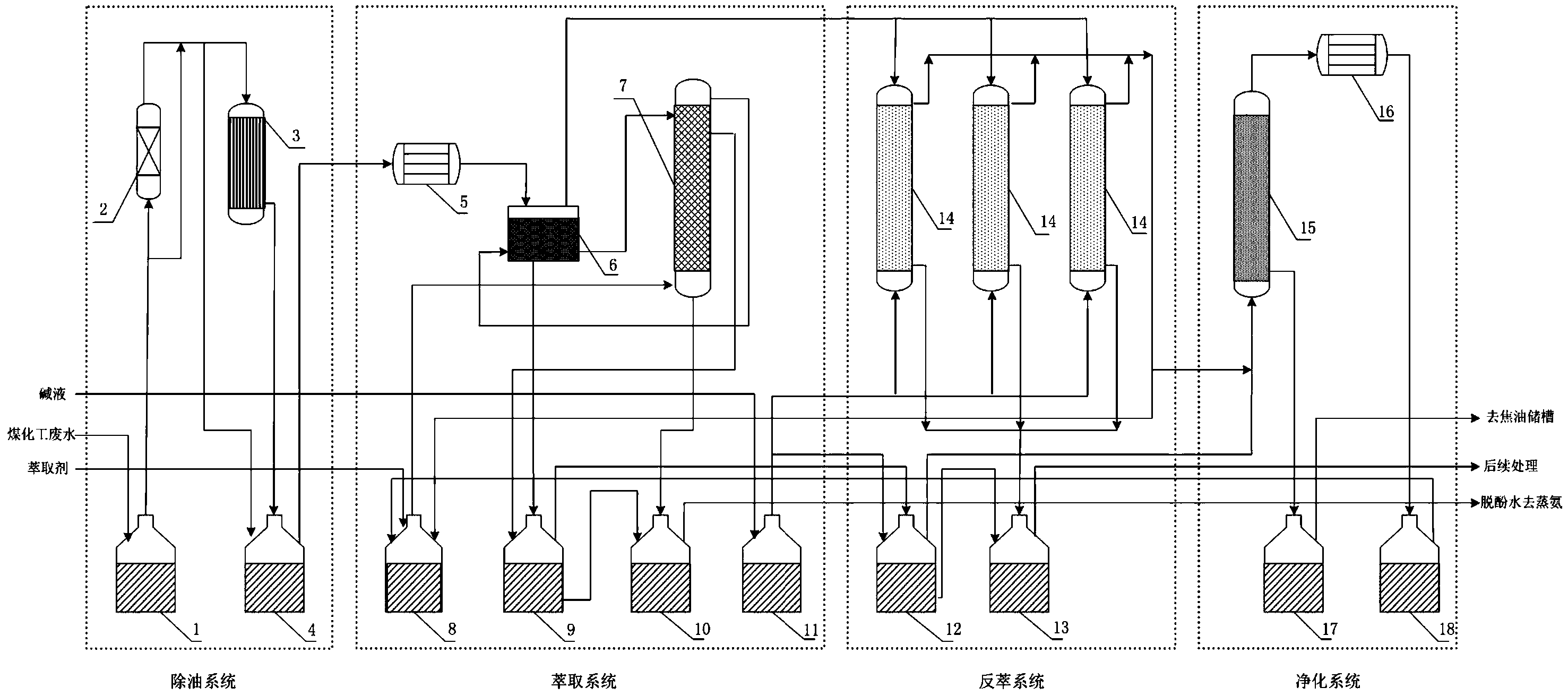
权利要求书
1.一种煤化工废水中酚油联合脱除系统,其特征在于,所述系统依次包括除油系统、萃取系统、反萃系统和净化系统。
2.根据权利要求1所述的系统,其特征在于,所述除油系统依次包括煤化工废水储槽(1)、焦炭过滤器(2)、陶瓷膜过滤器(3)和脱油废水中间槽(4)。
3.根据权利要求1或2所述的系统,其特征在于,所述萃取系统包括换热器(5)、萃取槽(6)、萃取塔(7)、萃取剂中间槽(8)、中间层处理反应器(9)、脱酚水中间槽(10)和碱液配制槽(11),其中换热器(5)出料口与萃取槽(6)进料口相连,萃取槽(6)底部出料口与萃取塔(7)塔顶进料口相连,萃取槽(6)的中间层出料口与中间层处理反应器(9)进料口相连,萃取塔(7)塔顶出料口与萃取槽(6)萃取剂入口相连,萃取塔(7)的中间层出料口与中间层处理反应器(9)进料口相连,萃取塔(7)塔底出料口与脱酚水中间槽(10)进料口相连,萃取剂中间槽(8)出料口与萃取塔(7)萃取剂入口相连,中间层处理反应器(9)水相出口与脱酚水中间槽(10)进料口相连。
4.根据权利要求1-3任一项所述的系统,其特征在于,所述反萃系统包括反萃塔(14)、富酚有机相中间槽(12)和酚钠中间槽(13),其中反萃塔(14)塔底出料口与酚钠中间槽(13)进料口相连,富酚有机相中间槽(12)水相出料口与酚钠中间槽(13)进料口相连;
优选地,所述反萃塔(14)的个数为1个、2个或3个。
5.根据权利要求1-4任一项所述的系统,其特征在于,所述净化系统包括萃取剂净化塔(15)、塔顶冷凝器(16)、焦油中间槽(17)和净化萃取剂中间槽(18),其中萃取剂净化塔(15)塔顶出料口与塔顶冷凝器(16)进料口相连,塔顶冷凝器(16)出口与净化萃取剂中间槽(18)进料口相连,萃取剂 净化塔(15)塔底出料口与焦油中间槽(17)相连。
6.根据权利要求1-5任一项所述的系统,其特征在于,所述除油系统中脱油废水中间槽(4)出料口与换热器(5)入口相连,萃取槽(6)顶部出料口与反萃塔(14)塔顶进料口相连,中间层处理反应器(9)出料口与富酚有机相中间槽(12)进料口相连,碱液配制槽(11)出料口与反萃塔(14)塔底进料口和富酚有机相中间槽(12)进料口相连,反萃塔(14)塔顶出料口与萃取剂中间槽(8)进料口相连,反萃塔(14)塔顶出料口与萃取剂净化塔(15)塔底进料口相连,富酚有机相中间槽(12)有机相出料口与萃取剂净化塔(15)塔底进料口相连,净化萃取剂中间槽(18)出料口与萃取剂中间槽(8)进料口相连。
7.一种如权利要求1-6任一项所述系统的处理工艺,其特征在于,所述处理工艺依次包括除油过程、萃取过程、反萃过程和净化过程。
8.根据权利要求7所述的处理工艺,其特征在于,所述除油过程为预处理过程,其包括以下步骤:煤化工废水进入煤化工废水储槽(1),依次流经焦炭过滤器(2)和陶瓷膜过滤器(3)进入脱油废水中间槽(4);
优选地,所述萃取过程包括以下步骤:
(1)萃取脱焦油:脱油废水中间槽(4)的废水经换热器(5)降温后进入萃取槽(6)脱焦油和酚,萃取槽(6)槽底排出的废水进入萃取塔(7),萃取槽(7)中富焦油和酚有机相进入反萃塔(14),萃取槽(6)中间层液体进入中间层处理反应器(9);
(2)萃取脱酚:萃取槽(6)槽底排出的废水进入萃取塔(7),萃取剂由萃取剂中间槽(8)进入萃取塔,萃取塔(7)塔顶富酚有机相进入萃取槽(6),萃取塔(7)中间层液体进入中间层处理反应器(9),萃取塔(7)塔底废水进入脱酚水中间槽(10);
(3)中间层液体的处理:中间层处理反应器(9)脱出的油相进入富酚有机相中间槽(12),中间层处理反应器(9)脱出的水相进入脱酚水中间槽(10);
优选地,所述反萃过程包括以下步骤:萃取槽(6)中富焦油和酚有机相进入反萃塔(14),反萃塔(14)塔底产品进入酚钠中间槽(13),反萃塔(14)塔顶有机相进入萃取剂中间槽(8)和萃取剂净化塔(15),碱液配置槽(11)中碱液进入反萃塔(14)和富酚有机相中间槽(12),富酚有机相中间槽(12)分离出的富酚钠水相进入酚钠中间槽(13),富酚有机相中间槽(12)分离出的有机相进入萃取剂净化塔(15);
优选地,所述净化过程包括以下步骤:反萃塔(14)塔顶有机相和富酚有机相中间槽(12)分离出的有机相进入萃取剂净化塔(15)再生萃取剂,萃取剂净化塔(15)塔顶排出的萃取剂经塔顶冷凝器(16)冷凝后进入净化萃取剂中间槽(18),再泵入萃取剂中间槽(8),萃取剂净化塔(15)塔底排出的焦油进入焦油中间槽(17)。
9.根据权利要求7或8所述的处理工艺,其特征在于,所述萃取过程步骤(1)中脱油废水中间槽(4)的废水经换热器(5)降温至20~50℃;
优选地,所述萃取过程步骤(1)中萃取槽(6)中萃取剂为萃取塔(7)塔顶富酚有机相;
优选地,所述萃取过程步骤(2)萃取剂中间槽(8)中萃取剂为专利CN103848468A公布的酚氨废水萃取剂;
优选地,所述萃取过程步骤(2)萃取塔(7)中油水相体积比为1:1~5;
优选地,所述萃取过程步骤(2)萃取塔(7)中萃取温度为20~30℃。
10.根据权利要求7-9任一项所述的处理工艺,其特征在于,所述反萃过程碱液配置槽(11)中碱液为氢氧化钠水溶液;
优选地,所述反萃过程碱液配置槽(11)中氢氧化钠水溶液的质量浓度为10~30%;
优选地,所述反萃过程中反萃塔(14)塔顶有机相和富酚有机相中间槽(12)分离出的有机相间歇进入萃取剂净化塔(15)。
11.根据权利要求7-10任一项所述的处理工艺,其特征在于,所述净化过程中萃取剂净化塔(15)2~5天进行一次再生萃取剂的操作;
优选地,所述净化过程中萃取剂净化塔(15)塔顶温度为120~180℃;
优选地,所述净化过程中萃取剂净化塔(15)塔顶压力为0.05~0.25MPa;
优选地,所述净化过程中萃取剂净化塔(15)塔底温度为110~150℃;
优选地,所述净化过程中萃取剂净化塔(15)塔底压力为0.10~0.20MPa。
说明书
一种煤化工废水中酚油联合脱除系统及处理工艺
技术领域
本发明属于水处理技术领域,特别涉及一种煤化工废水中酚油联合脱除系统及处理工艺。
背景技术
煤化工废水是炼焦、煤气净化及化工产品精制等过程产生的工业废水,主要含有挥发酚、多环芳烃及氧、硫、氮等杂环化合物,是一种高COD、高酚值、高氨氮且很难处理的工业有机废水。其主要来自于剩余氨水、煤气净化过程中产生的废水和焦油、粗苯等的精制过及其它场合产生的废水。煤化工废水是含有大量难降解有机污染物的工业废水,超标排放对环境造成严重的污染。
由于该水质水量变化大、成分复杂,所以处理煤化工废水的工艺也众多。国内多采用预处理除油,气提法除氨,萃取法去除酚、氰,生物法处理等工序。
专利CN10332067A公布了一种处理焦化剩余氨水的新方法。该发明由五个工序组成:蒸氨脱酸、气提脱酚、萃取脱酚、氧化处理以及废水利用。
专利CN101597124A公开了一种处理含煤化工煤气化废水的方法,该方法包括单塔加压汽提脱除酸性气体和氨、测线抽出气三级分凝、二异丙醚萃取酚、溶剂回收过程,并得到粗酚产品。该发明溶剂回收塔和溶剂汽提塔回收萃取剂,得到粗酚,并实现了煤气化废水单塔联合脱除酸性气体和氨的过程。
但上述各工艺仅仅是脱焦油,未对煤化工废水中含量较大的焦油进行回收利用。而且未解决萃取工艺中一直存在重大问题,即萃取中间层的存在。萃取中间层的产生会浪费大量萃取剂及可回收的酚类等资源,可导致工厂不能正常作业,严重时甚至需要停产整治。
发明内容
为了克服上述现有技术的不足,本发明提供了一种煤化工废水中酚油联合脱除工艺。在原有工艺基础上添加焦油回收系统和中间层回收系统,改进工序,解决现有萃取工艺中产生大量中间层并无法利用的难题,提高萃取剂、苯酚等的回收利用率,联合回收废水中含量较高的副产品焦油类,从而降低废水处理成本,减少污染物排放量,使出水的COD含量达到后续处理要求。
为达此目的,本发明采用以下技术方案:
一种煤化工废水中酚油联合脱除系统,所述系统依次包括除油系统、萃取系统、反萃系统和净化系统。
所述除油系统依次包括煤化工废水储槽、焦炭过滤器、陶瓷膜过滤器和脱油废水中间槽,煤化工废水储存在煤化工废水储槽中,焦炭过滤器和陶瓷膜过滤器用于脱除煤化工废水中的固体污染物和部分固体焦油。
所述萃取系统包括换热器、萃取槽、萃取塔、萃取剂中间槽、中间层处理反应器、脱酚水中间槽和碱液配制槽,其中换热器出料口与萃取槽进料口相连,萃取槽底部出料口与萃取塔塔顶进料口和相连,萃取槽的中间层出料口与中间层处理反应器进料口相连,萃取塔塔顶出料口与萃取槽萃取剂入口相连,萃取塔的中间层出料口与中间层处理反应器进料口相连,萃取塔塔底出料口与脱酚水中间槽进料口相连,萃取剂中间槽出料口与萃取塔萃取剂入口相连,中间层处理反应器水相出口与脱酚水中间槽进料口相连。
所述反萃系统包括反萃塔、富酚有机相中间槽和酚钠中间槽,其中反萃塔塔底出料口与酚钠中间槽进料口相连,富酚有机相中间槽水相出料口与酚钠中间槽进料口相连。
优选地,所述反萃塔的个数为1个、2个或3个,在工艺过程中可为1个反萃塔、2个反萃塔并联或3个反萃塔并联。
所述净化系统包括萃取剂净化塔、塔顶冷凝器、焦油中间槽和净化萃取剂中间槽,其中萃取剂净化塔塔顶出料口与塔顶冷凝器进料口相连,塔顶冷凝器出口与净化萃取剂中间槽进料口相连,萃取剂净化塔塔底出料口与焦油中间槽相连。
所述除油系统中脱油废水中间槽出料口与换热器入口相连,萃取槽顶部出料口与反萃塔塔顶进料口相连,中间层处理反应器出料口与富酚有机相中间槽进料口相连,碱液配制槽出料口与反萃塔塔底进料口和富酚有机相中间槽进料口相连,反萃塔塔顶出料口与萃取剂中间槽进料口相连,反萃塔塔顶出料口与萃取剂净化塔塔底进料口相连,富酚有机相中间槽有机相出料口与萃取剂净化塔塔底进料口相连,净化萃取剂中间槽出料口与萃取剂中间槽进料口相连。
以上所述煤化工废水中酚油联合脱除系统的处理工艺,所述处理工艺包括除油过程、萃取过程、反萃过程和净化过程。
所述除油过程为预处理过程,其包括以下步骤:煤化工废水进入煤化工废水储槽,依次流经焦炭过滤器和陶瓷膜过滤器进入脱油废水中间槽,焦炭过滤器和陶瓷膜过滤器脱除煤化工废水中的固体污染物和部分固体焦油,脱除物进行焚烧处理,处理后的废水进入脱油废水中间槽。
所述萃取过程包括以下步骤:
(1)萃取脱焦油:脱油废水中间槽的废水经换热器降温后进入萃取槽,用萃取法将废水中的焦油和酚萃取出。所用的萃取剂由萃取塔萃取出的富酚有机相循环补给,萃取槽槽底排出的废水进入萃取塔,萃取槽中萃取出的富焦油和酚有机相进入反萃塔,萃取槽中间层液体进入中间层处理反应器。
(2)萃取脱酚:萃取槽槽底排出的废水进入萃取塔,所用萃取剂来自萃取剂中间槽并进入萃取塔逆流萃取废水中的酚类。萃取塔塔顶富酚有机相作为萃取剂循环补给给萃取槽,萃取塔中间层液体进入中间层处理反应器,萃取塔塔底脱酚废水进入脱酚水中间槽,待进一步的后续处理。
(3)中间层液体的处理:中间层处理反应器分离油水两相,脱出的油相进入富酚有机相中间槽,中间层处理反应器脱出的水相进入脱酚水中间槽。
所述反萃过程包括以下步骤:萃取过程萃取槽排出的富焦油和酚有机相进入反萃塔,经反萃脱除有机相中的酚,其所使用的碱液来自碱液配置槽。反萃塔塔底粗酚产品进入酚钠中间槽,反萃塔塔顶有机相进入萃取剂中间槽和萃取剂净化塔,碱液配置槽中碱液进入反萃塔和富酚有机相中间槽。富酚有机相中间槽定期由碱液配置槽补入碱液同步反萃,富酚有机相中间槽分离出的富酚钠水相进入酚钠中间槽,富酚有机相中间槽分离出的有机相进入萃取剂净化塔。
所述净化过程包括以下步骤:反萃塔塔顶有机相和富酚有机相中间槽分离出的有机相间歇进入萃取剂净化塔再生萃取剂,2~5天进行一次该操作。萃取剂净化塔塔顶排出的萃取剂经塔顶冷凝器后进入净化萃取剂中间槽,再泵入萃取剂中间槽,实现萃取剂循环利用。萃取剂净化塔塔底排出的焦油进入焦油中间槽再转入焦油储罐进行回收利用。
所述萃取过程步骤(1)中脱油废水中间槽的废水经换热器降温至20~50℃,例如20℃、23℃、25℃、27℃、30℃、33℃、35℃、37℃、40℃、43℃、45℃、47℃或50℃等。
所述萃取过程步骤(1)中萃取槽中萃取剂为萃取塔塔顶富酚有机相,使富酚有机相得到循环利用。
所述萃取过程步骤(2)萃取剂中间槽中萃取剂为专利CN103848468A公布的煤化工废水萃取剂,该萃取剂按质量分数含有以下组分:
中性含磷类萃取剂4~25%
酸性含磷类萃取剂0.5~10%
助溶剂0.5~5%
稀释剂60~95%
因萃取剂的配方已为公开的现有技术,此处不再对其具体成分进行赘述。
所述萃取过程步骤(2)萃取塔中油水相体积比1:1~5,例如1:1、1:1.5、1:2、1:2.5、1:3、1:3.5、1:4、1:4.5或1:5等。
所述萃取过程步骤(2)萃取塔中萃取温度为20~30℃,例如20℃、21℃、22℃、23℃、24℃、25℃、26℃、27℃、28℃、29℃或30℃等。
所述反萃过程碱液配置槽中碱液为氢氧化钠水溶液。
所述反萃过程碱液配置槽中氢氧化钠水溶液的质量浓度为10~30%,例如10%、13%、15%、17%、20%、23%、25%、27%或30%等。
所述反萃过程中反萃塔塔顶有机相和富酚有机相中间槽分离出的有机相间歇进入萃取剂净化塔。
所述净化过程中萃取剂净化塔2~5天进行一次再生萃取剂的操作,例如2天、3天、4天或5天等。
所述净化过程中萃取剂净化塔塔顶温度为120~180℃,例如120℃、125℃、130℃、135℃、140℃、145℃、150℃、155℃、160℃、165℃、170℃、175℃或180℃等。
所述净化过程中萃取剂净化塔塔顶压力为0.05~0.25MPa,例如0.05MPa、0.07MPa、0.10MPa、0.13MPa、0.15MPa、0.17MPa、0.20MPa、0.23MPa或0.25MPa等。
所述净化过程中萃取剂净化塔塔底温度为110~150℃,例如110℃、115℃、120℃、125℃、130℃、135℃、140℃、145℃或150℃等。
所述净化过程中萃取剂净化塔塔底压力为0.10~0.20MPa,例如0.10MPa、0.11MPa、0.12MPa、0.13MPa、0.14MPa、0.15MPa、0.16MPa、0.17MPa、0.18MPa、0.19MPa或0.20MPa等。
与现有技术相比,本发明具有以下有益效果:
(1)回收焦油产品,充分利用废水资源。现有煤化工废水处理工艺多采用过滤等技术将焦油与废水中固废物同步滤除,未见有效回收焦油的工艺,且脱除污染物较难处理。本工艺将“萃取塔”中富酚萃取剂循环至“萃取槽”,利用废萃取剂携带分离煤化工废水中的焦油,最终在“萃取剂净化塔”脱除粗焦油产品。避免了焦油产品的浪费现象,增加了废水处理中产品的产出。
(2)萃取剂回收利用率高。乳化中间层的产生在萃取工艺中是不可避免的,从萃取槽、萃取塔中移除的乳化中间层含有大量有机溶剂。本工艺利用中间层处理反应器装置将乳化油水两相彻底分离,萃取剂回收率达99.5%以上。即有效降低了因溶剂损耗而产生的处理成本,又避免废水二次污染。
(3)萃取剂性能优异,处理废水效果佳。煤化工废水经四过程处理后废水中焦油回收率>94%,苯酚去除率>99%,COD去除率>98%。排出水满足后续蒸氨处理工艺要求。