申请日2015.09.08
公开(公告)日2015.12.09
IPC分类号C02F3/30
摘要
一种油页岩干馏废水的分段进水多级A/O-MBR处理方法,按以下步骤进行:(1)油页岩干馏废水引入分段进水多级A/O-MBR处理系统;分成三部分分别进入三个缺氧池;(2)在各缺氧池进行反硝化反应;(3)进入各好氧池进行亚硝化反应和硝化反应;(4)进入膜生物反应器;(5)经膜组件过滤后产生的清水排出,截留下的污泥混合液返回第一缺氧池。本发明的方法通过对第一好氧池和第二好氧池进行限氧曝气,可实现短程硝化;通过分段进水可充分利用原水中的COD进行反硝化,减少外加碳源投加量和混合液回流比,可节省曝气成本和反硝化所需碳源。
摘要附图
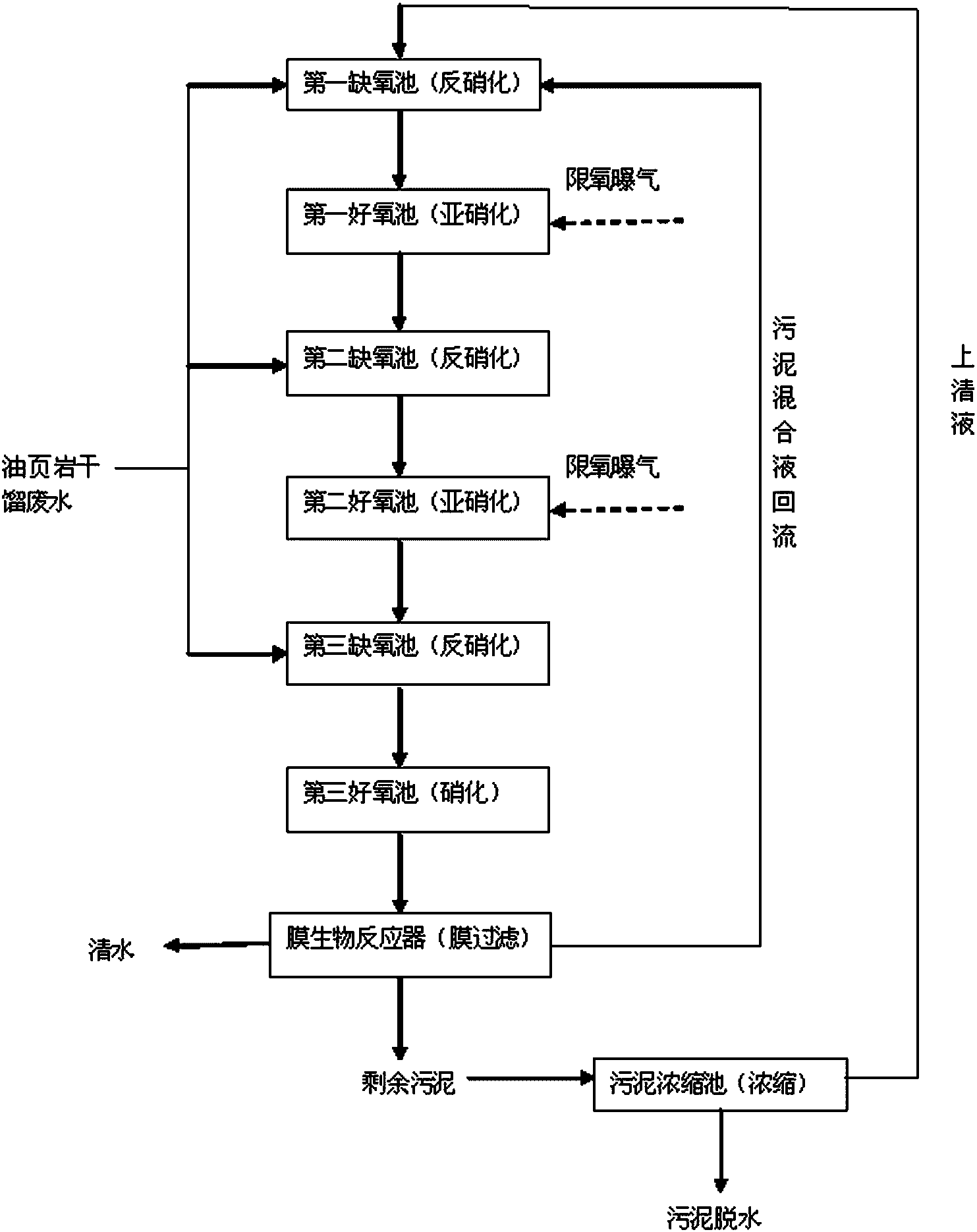
权利要求书
1.一种油页岩干馏废水的分段进水多级A/O-MBR处理方法,其特征在于按以下步骤进行:
(1)将经过预处理的油页岩干馏废水引入分段进水多级A/O-MBR处理系统;所述的分段进水多级A/O-MBR处理系统由第一缺氧池、第一好氧池、第二缺氧池、第二好氧池、第三缺氧池、第三好氧池和膜生物反应器依次串联组成,其中各缺氧池内均设有搅拌装置或潜水推进器,各好氧池内均设有曝气装置,膜生物反应器通过回流管与第一缺氧池连通;油页岩干馏废水被分为第一部分、第二部分和第三部分,分别进入第一缺氧池、第二缺氧池和第三缺氧池;其中各好氧池和缺氧池中的活性污泥浓度为3000~6000mg/L;
(2)在搅拌和温度10~30℃条件下,进入各缺氧池的油页岩干馏废水进行反硝化反应,各缺氧池内的溶解氧浓度≤0.3mg/L;
(3)反硝化反应后的油页岩干馏废水分别进入第一好氧池、第二好氧池和第三好氧池,通过曝气装置向各好氧池内进行曝气;控制第一好氧池和第二好氧池内溶解氧浓度在0.8~1.2mg/L,油页岩干馏废水中的氨氮在第一好氧池和第二好氧池内进行亚硝化反应;控制第三好氧池内物料的溶解氧含量在2~4mg/L;油页岩干馏废水中的氨氮和亚硝酸盐氮在第三好氧池内进行硝化反应;其中油页岩干馏废水中的氨氮在亚硝化反应后形成亚硝酸盐氮,油页岩干馏废水中的氨氮和亚硝酸盐氮在硝化反应后形成硝酸盐氮;
(4)第一好氧池内的氨氮在亚硝化反应后进入第二缺氧池,第二好氧池内的氨氮在亚硝化后进入第三缺氧池,第三好氧池内的氨氮在硝化反应后,进入膜生物反应器;
(5)膜生物反应器内设有曝气装置和反清洗装置,通过曝气装置控制膜生物反应器的溶解氧含量在2~4mg/L;在膜生物反应器内的污泥混合液经膜组件过滤后产生的清水排出,膜组件截留下的污泥混合液返回第一缺氧池,控制整个系统的回流比为200~400%;由油页岩干馏废水与活性污泥混合形成的污泥混合液在整个系统内循环。
2.根据权利要求1所述的一种油页岩干馏废水的分段进水多级A/O-MBR处理方法,其特征在于步骤(1)中,第一部分占全部油页岩干馏废水总体积的35~50%,第二部分占全部油页岩干馏废水总体积的25~35%。
3.根据权利要求1所述的一种油页岩干馏废水的分段进水多级A/O-MBR处理方法,其特征在于所述的经过预处理的油页岩干馏废水的氨氮浓度1000~4000mg/L,总氮浓度1050~4500mg/L,COD浓度1000~5000mg/L。
4.根据权利要求1所述的一种油页岩干馏废水的分段进水多级A/O-MBR处理方法,其特征在于所述的清水的氨氮浓度≤10mg/L,总氮含量≤300mg/L,COD浓度≤300mg/L。
5.根据权利要求1所述的一种油页岩干馏废水的分段进水多级A/O-MBR处理方法,其特征在于缺氧池总水力停留时间t1=24×(TN1-TN2)/(N3×V1),单位为小时;其中TN1为油页岩干馏废水中的总氮含量,单位为mg/L,TN2为清水中的总氮含量,单位为mg/L,N3为油页岩干馏废水的污泥浓度,单位为mg/L,V1为反硝化速率,选值0.08~0.2kgNO3-N/kgMLSS·d。
6.根据权利要求1所述的一种油页岩干馏废水的分段进水多级A/O-MBR处理方法,其特征在于各好氧池的pH在7.5~8.0之间,当pH不在此范围时,通过投加NaHCO3和HCl调控。
7.根据权利要求1所述的一种油页岩干馏废水的分段进水多级A/O-MBR处理方法,其特征在于所述的进入各缺氧池中的油页岩干馏废水的COD和总氮含量比(COD/TN)≥2;当COD和总氮含量比不足时,在油页岩干馏废水进入各缺氧池时,向缺氧池中补充碳源;所述的碳源选用甲醇和葡萄糖按质量比1:1混合制成的碳源混合液。
说明书
油页岩干馏废水的分段进水多级A/O-MBR处理方法
技术领域
本发明属于污水处理技术领域,特别涉及一种油页岩干馏废水的分段进水多级A/O-MBR处理方法。
背景技术
油页岩是一种重要的替代能源,可以用于提炼页岩油,中国的页岩油产量从2012年的年产约70万吨,上升至2014年的80万吨,产油量居世界首位。页岩油生产过程中会产生大量的油页岩干馏废水,该废水含有大量的COD、氨氮、挥发酚、石油类等污染物,是一种含高氨氮、高有机污染物、难处理的工业废水。
国内外对油页岩干馏废水处理的方法主要有物化法、化学法、生物法;其中物化法和化学法主要用于去除油页岩干馏废水中的石油类和酚类和提高废水可生化性(预处理)和进行废水的深度处理;生物法主要为延时曝气法、序批式活性污泥法(SBR)、膜生物反应器法(MBR)、缺氧/好氧法(A/O)、厌氧/缺氧/好氧法(A/A/O)、接触氧化法等,这些工艺有效的提高了废水中有机物和氨氮的去除效果,但在处理COD、氨氮、总氮含量高的油页岩干流废水时,往往存在着去除率低、运行管理复杂、处理效果不稳定、处理成本高等弊病。随着国家相关环保标准增加了对总氮指标的控制,现有的技术很难满足新标准的要求,为此,一些油页岩炼油厂开始持续投加高效微生物;或者是采用大回流比和延长水力停留时间、加强曝气等方法用以提高COD、氨氮、总氮去除效率。但这些方法极大的提高了污水处理工程的运行成本。因此开发更高效、节能、次生污染小、处理效果稳定的新技术来促进油页岩干馏废水治理行业的发展,是目前急需解决的问题。
发明内容
针对现有油页岩干馏废水处理技术存在的上述问题,本发明提供一种油页岩干馏废水的分段进水多级A/O-MBR处理方法,采用多级分段A/O系统和MBR系统处理油页岩干馏废水,在保证水质稳定的同时降低运行成本。
本发明的方法按以下步骤进行:
1、将经过预处理的油页岩干馏废水引入分段进水多级A/O-MBR处理系统;所述的分段进水多级A/O-MBR处理系统由第一缺氧池、第一好氧池、第二缺氧池、第二好氧池、第三缺氧池、第三好氧池和膜生物反应器依次串联组成,其中各缺氧池内均设有搅拌装置或潜水推进器,各好氧池内均设有曝气装置,膜生物反应器通过回流管与第一缺氧池连通;油页岩干馏废水被分为第一部分、第二部分和第三部分,分别进入第一缺氧池、第二缺氧池和第三缺氧池;其中各好氧池和缺氧池中的活性污泥浓度为3000~6000mg/L;
2、在搅拌和温度10~30℃条件下,进入各缺氧池的油页岩干馏废水进行反硝化反应,各缺氧池内的溶解氧浓度≤0.3mg/L;
3、反硝化反应后的油页岩干馏废水分别进入第一好氧池、第二好氧池和第三好氧池,通过曝气装置向各好氧池内进行曝气;控制第一好氧池和第二好氧池内溶解氧浓度在0.8~1.2mg/L,油页岩干馏废水中的氨氮在第一好氧池和第二好氧池内进行亚硝化反应;控制第三好氧池内物料的溶解氧含量在2~4mg/L;油页岩干馏废水中的氨氮和亚硝酸盐氮在第三好氧池内进行硝化反应;其中油页岩干馏废水中的氨氮在亚硝化反应后形成亚硝酸盐氮,油页岩干馏废水中的氨氮和亚硝酸盐氮在硝化反应后形成硝酸盐氮;
4、第一好氧池内的氨氮在亚硝化反应后进入第二缺氧池,第二好氧池内的氨氮在亚硝化后进入第三缺氧池,第三好氧池内的氨氮在硝化反应后,进入膜生物反应器;
5、膜生物反应器内设有曝气装置和反清洗装置,通过曝气装置控制膜生物反应器的溶解氧含量在2~4mg/L;在膜生物反应器内的污泥混合液经膜组件过滤后产生的清水排出,膜组件截留下的污泥混合液返回第一缺氧池,控制整个系统的回流比为200~400%;由油页岩干馏废水与活性污泥混合形成的污泥混合液在整个系统内循环。
上述的步骤1中,第一部分占全部油页岩干馏废水总体积的35~50%,第二部分占全部油页岩干馏废水总体积的25~35%。
上述的整个系统的回流比是指返回第一缺氧池的污泥混合液与进入系统的全部经过预处理的油页岩干馏废水的体积流量比。
上述的经过预处理的油页岩干馏废水的氨氮含量1000~4000mg/L,总氮含量1050~4500mg/L,COD浓度1000~5000mg/L。
上述的清水的氨氮浓度≤10mg/L,总氮含量≤300mg/L,COD浓度≤300mg/L。
上述的预处理是指将原始的油页岩干馏废水经过热交换降温、隔油和气浮预处理;其中热交换将温度由≥60℃降低至≤30℃,隔油和气浮将石油类的含量浓度降低至≤20mg/L。
上述方法中,缺氧池总水力停留时间t1=24×(TN1-TN2)/(N3×V1),单位为小时;其中TN1为油页岩干馏废水中的总氮含量,单位为mg/L,TN2为清水中的总氮含量,单位为mg/L,N3为油页岩干馏废水的污泥浓度,单位为mg/L,V1为反硝化速率,选值0.08~0.2kgNO3-N/kgMLSS·d。
上述方法中,各缺氧池和好氧池容积比为1比2,好氧池总水力停留时间t2=2×t1。
上述方法中,各好氧池的pH在7.5~8.0之间,当pH不在此范围时,通过投加NaHCO3和HCl调控。
上述方法中,进入各缺氧池中的油页岩干馏废水的COD和总氮含量比(COD/TN)≥2;当COD和总氮含量比不足时,在油页岩干馏废水进入各缺氧池时,向缺氧池中补充碳源;所述的碳源选用甲醇和葡萄糖按质量比1:1混合制成的碳源混合液。
上述方法中,定期将膜生物反应器内累积的剩余污泥排出,输送至污泥浓缩池,再经污泥脱水机脱水后外运,污泥浓缩池内形成的上清液输送至第一缺氧池。
上述方法中,经膜过滤后产生的清水直接排放,或按国家或地方的排放标准进行深度处理(如高级氧化、纳滤、吸附等方法)。
上述方法中,当膜生物反应器的膜阻力≥30kPa时,启动反清洗装置清洗膜组件。
通过采用前述技术方案,本发明具有以下积极有益效果:
(1)采用分段进水多级A/O-MBR生化处理工艺,根据进水水质特点,通过分别在三个缺氧池内分段进水,可以实现第一好氧池和第二好氧池硝化液直接进入第二缺氧池和第三缺氧池进行反硝化,从而达到充分利用原水中的COD进行反硝化,减少外加碳源投加量和混合液回流比的目的;
(2)可以对第一好氧池和第二好氧池进行限氧曝气,以实现第一好氧池和第二好氧池内亚硝态氮的累积,并可节省曝气成本10%以上;
(3)将第一好氧池和第二好氧池处理后含有亚硝态氮的出水分别直接依次流入第二缺氧池和第三缺氧池,在第二缺氧池和第三缺氧池内反硝化,实现了短程硝化反硝化和同步硝化反硝化,可节省反硝化所需碳源20%以上。