申请日2015.09.16
公开(公告)日2015.11.25
IPC分类号C02F103/10; C02F9/06
摘要
本发明公开了一种基于特种膜的油田废水处理工艺,包括第一阶段除油除悬浮物,第二阶段电化学装置氧化破胶,第三阶段利用核心SuperRO系统脱盐除COD等三个主要工段,采用纳米气浮装置进行除油和除悬浮物,再利用氧化能力最好的电化学装置对污废进行物化,提高了各物质间的传质效率,缩短反应时间和降低药品消耗,从而实现只需较为简单的预处理即可使废水直接进入膜系统,保障系统的运行稳定和使用寿命,大大降低了环保的建设成本和污水处理的运行费用。
摘要附图
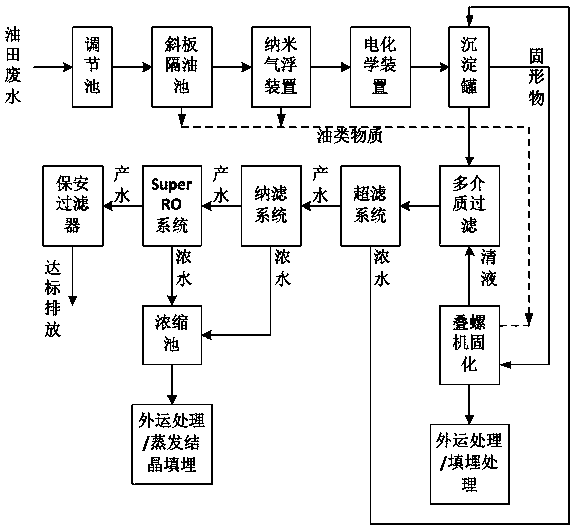
权利要求书
1.一种基于特种膜的油田废水处理工艺,其特征在于,包括如下步骤:
(1)将气田废水引入调节池中汇集;
(2)在斜板隔油池中对气田废水进行除油预处理,去除的油类物质进入叠螺机固化工序;
(3)预处理后的出水由纳米气浮装置进行气浮处理,去除的油类物质和悬浮物也进入叠螺机固化工序;
(4)气浮处理后的出水经电化学装置物化处理;
(5)物化处理后的出水在沉淀罐中沉积分离,并经多介质过滤,沉淀后的固形物也进入叠螺机固化工序;
(6)过滤后的出水进入超滤系统进行超滤处理,产生的浓水返回沉淀罐;
(7)超滤处理的出水进入纳滤系统进行纳滤处理,产生的浓水进入浓缩池聚集;
(8)纳滤处理的出水进入SuperRO系统进行脱盐和除COD处理,产生的浓水进入浓缩池聚集,其产水经保安过滤器后达标排放。
2.根据权利要求1所述的基于特种膜的油田废水处理工艺,其特征在于,所述叠螺机固化工序中,产生的清液返回再经多介质过滤,产生的残渣外运处理或填埋处理。
3.根据权利要求1所述的基于特种膜的油田废水处理工艺,其特征在于,所述浓缩池聚集的浓水外运处理,或经蒸发结晶后再填埋处理。
4.根据权利要求1所述的基于特种膜的油田废水处理工艺,其特征在于,所述SuperRO系统对COD的截留率不低于90%,对无机盐的截留率不低于97%。
说明书
基于特种膜的油田废水处理工艺
技术领域
本发明涉及污废处理技术领域,具体地讲,涉及的是一种基于特种膜的油田废水处理工艺。
背景技术
油田废水通常有油田采出水、压裂返排液、钻井废水、矿区雨水和生活污水等。
从地层中随原油一起开采出来的液体(采出液),既含有原油又含有污水,而经原油脱水分离出来的水称为“油田采出水”,是油田开发和生产中最主要的废水。主要是来自原油脱水站,及联合站内各种原油储罐的罐底水、将含盐量较高的原油用其他清水洗盐后的污水等。
由于原油产地地质条件、原油性质、注水性质以及原油集输和初加工的整个工艺不尽相同,我国部分油田采出水污水水质有较大的差异,但从总体上看,油田采出水都具有以下共同特点:含油量高,一般在1000mg/L以上,其回注堵塞地层,外排造成污染;悬浮物含量高,颗粒细小,沉降缓慢,容易造成地层堵塞;矿化度高,一般在1000mg/L以上,最高可达14×104mg/L,会加速腐蚀,给废水生化处理造成困难;含有Ca2+、Mg2+、HCO2+、Ba2+、Cr2+等结垢离子,容易在管道、容器中结垢;含有原油和采油过程中的各种化学药剂、有机物,COD高,会利于微生物繁殖,造成腐蚀和堵塞;常见有铁细菌、腐生菌、硫酸盐还原菌等微生物,容易腐蚀管线,堵塞地层;污水中溶解有O2、H2S、CO2等多种气体,易导致管线结垢,加剧金属设备的腐蚀。
压裂是油气井增产的主要措施之一,为各油田普遍采用。常规压裂施工所采用的压裂液体系,以水基压裂液为主。压裂返排液是在增产作业返排的过程中产生的,其中不仅有原油、压入的聚合有机物、陶粒砂(或石英砂)、还含有地层中的渗入水、渗入的岩屑、地层中的各种腐生菌尤其是危害明显的SRB菌。压裂液废水有以下特点:成分复杂,主要成份是高浓度胍胶/冻胶、高分子聚合物以及油类,其次是SRB硫酸盐还原菌、硫化物和总铁等,总铁、总硫含量都在20mg/L左右,COD浓度高,一般从数千到上万mg/L不等,废液中石油类含量在10~1000mg/L之间;粘度大、乳化程度高,返排液的黏度一般是水的3~10倍,其中放喷液体的粘度很高,平均为10~20mpa.s,在其处理过程中,所投加的化学药剂在压裂返排液中很难扩散,传质作用缓慢,造成反应体系时间很长,处理效果差,若压裂所用为复合型压裂液,乳化更严重,放出的返排液乌黑、黏稠,静沉出水困难;悬浮物含量高达几千mg/L,由于压裂返排液组分的复杂性及其性质的独特性决定了其处理难度更大,给油气田生产和环境带来很大影响;水质水量变化,排放不连续,每口井排放量在100~200m3之间。
在石油、天然气开采钻探过程中,相对于废渣、废气和噪声污染,产生的钻井废液(包括废钻井液和钻井废水)同样是主要的污染源。钻井废水包括钻井废液及钻井过程产生的污水。主要有以下特点:污染物成分复杂,主要包括钻屑、石油、粘度控制剂(如粘土)、加重剂、粘土稳定剂、腐蚀剂、防腐剂、杀菌剂、润滑剂、地层亲和剂、消泡剂、重金属等;污染负荷高,COD高达几万,色度深,悬浮物含量高,并含有多种重金属,若不经处理直接排放,将对环境造成污染;水质、水量不稳定,由于钻井作业的临时性、分散性、流动性特点,使很多处理工艺受到限制,钻井废液处理难度很大;废液数量较多,如:四川地区平均每口井有300~400m3。
由上述可知,无论是采出水、压裂液,还是钻井废水,成分均较为复杂,主要包含石油类、悬浮物、胶体、有机物及盐类等,共性特点如下:①石油类物质种类多、含量高,含油量一般为1000mg/L左右,少部分油田污水含油量高达3000-5000mg/L,污水中含油的存在形式可分为悬浮状、分散状、乳化状和溶解状四种形态;SS含量高,悬浮颗粒微小,粒径一般为1~100μm,废水总SS为300~5000mg/L;有机物含量较高,一般油田废水COD基本在800~6000mg/L(钻井及压裂液可能好几万),废水中可能存在一定量环状芳烃类衍生物及聚合物,性质稳定,不易被氧化去除;矿化度高,无机盐种类多,含多种盐类,采出水高达几万甚至十几万毫克/升,大量的结垢盐分容易造成管线结垢。
现有技术中,气田废水治理工艺主要有回注、处理达标外排及资源化回用三种。
一、回注工艺
目前,回注仍是油田废水处理的主要办法。注水水质必须根据注入层物性指标进行优选确定。通常要求:在运行条件下注入水不应结垢;注入水对水处理设备、注水设备和输水管线腐蚀性要小;注入水不应携带超标悬浮物,有机淤泥和油;注入水注入油层后不使粘土发生膨胀和移动,与油层流体配伍性良好。过程主要为采出水依次经原水罐、沉降罐、一级过滤器、二级过滤器、精细过滤器和净化水罐达到注水标准。其优点在于运行费用相对较低,管理相对成熟,缺点在于一次性工程投资较高,对周边油田、周边段油藏有直接影响以及对周边地下水有直接影响,并且随社会经济发展,在政策上也有更多的限制。
二、达标外排
要实现达标排放,主要的处理任务是去除悬浮颗粒、油类、盐分和有机物。主要有两种工艺形式,其一是废水经预处理除去油和悬浮物后,采用高级氧化,如Fe/C微电解、芬顿等直接物化,然后排放。其存在的问题有①运行费用太高,依据不同的水质,一般运行费用高达100元/吨水以上;②对盐分没有去除,不能真正达到地方环保要求;③引入大量新的化学药剂,造成二次污染。
其二是废水经预处理除去油和悬浮物后,采用高级氧化,如Fe/C微电解、芬顿等直接物化,然后经过蒸发工序,最后排放。其存在的问题是①引入蒸发可解决盐分问题,但直接蒸发投资和运行费用太高;②蒸发冷凝液可能COD不达标;③引入大量新的化学药剂,造成二次污染。
总的来说,达标外排处理均是针对其中的S2-、COD等特征污染物。针对油田水脱COD研究开发了中和、絮凝沉降、氧化、Fe/C微电解、H2O2/Fe2+催化氧化、吸附、多种处理技术联合工艺。目前全球重视环境程度的提高,以及淡水资源越来越短缺,未来的发展方向为不外排、不浪费,尽量资源化回用。
发明内容
为克服现有技术存在的上述问题,本发明提供一种高效、不易污堵、使用寿命长、使用方便成本低的基于特种膜的油田废水处理工艺。
为了实现上述目的,本发明采用的技术方案如下:
一种基于特种膜的油田废水处理工艺,包括如下步骤:
(1)将气田废水引入调节池中汇集;
(2)在斜板隔油池中对气田废水进行除油预处理,去除的油类物质进入叠螺机固化工序;
(3)预处理后的出水由纳米气浮装置进行气浮处理,去除的油类物质和悬浮物也进入叠螺机固化工序;
(4)气浮处理后的出水经电化学装置物化处理;
(5)物化处理后的出水在沉淀罐中沉积分离,并经多介质过滤,沉淀后的固形物也进入叠螺机固化工序;
(6)过滤后的出水进入超滤系统进行超滤处理,产生的浓水返回沉淀罐;
(7)超滤处理的出水进入纳滤系统进行纳滤处理,产生的浓水进入浓缩池聚集;
(8)纳滤处理的出水进入SuperRO系统进行脱盐和除COD处理,产生的浓水进入浓缩池聚集,其产水经保安过滤器后达标排放。
其中,所述叠螺机固化工序中,产生的清液返回再经多介质过滤,产生的残渣外运处理或填埋处理。
并且,所述浓缩池聚集的浓水外运处理,或经蒸发结晶后再填埋处理。
具体地,所述纳米气浮装置为加压射流溶气平流式组合气浮机。所述SuperRO系统对COD的截留率不低于90%,对无机盐的截留率不低于97%。
与现有技术相比,本发明具有以下有益效果:
本发明采用纳米气浮装置进行除油和除悬浮物,再利用氧化能力最好的电化学装置对污废进行物化,提高了各物质间的传质效率,缩短反应时间和降低药品消耗,从而实现只需较为简单的预处理即可使废水直接进入膜系统,保障系统的运行稳定和使用寿命,大大降低了环保的建设成本和污水处理的运行费用,而且本发明构思新颖,设计巧妙,简单易用,具有广泛的应用前景,适合推广应用。