申请日2017.11.05
公开(公告)日2018.02.09
IPC分类号B01D25/21; C02F11/12
摘要
本发明涉及一种多腔室污泥高干度脱水装置,包括动力机构(1)、滤板机构、和机架(14),所述的动力机构(1)和滤板机构安装于机架(14)上,所述的滤板机构包括头板(6)、尾板(9)和多块中间滤板(8),所述的头板(6)和与其相邻的中间滤板(8)之间、相邻的中间滤板(8)之间、尾板(9)和与其相邻的中间滤板(8)之间均形成多个压滤腔室;污泥进入所述多个压滤腔室内,通过所述动力机构(1)作用于所述滤板机构,实现压滤脱水。采用本发明,具有易损件少、能耗低,脱水后污泥含水率较低的优点。
摘要附图
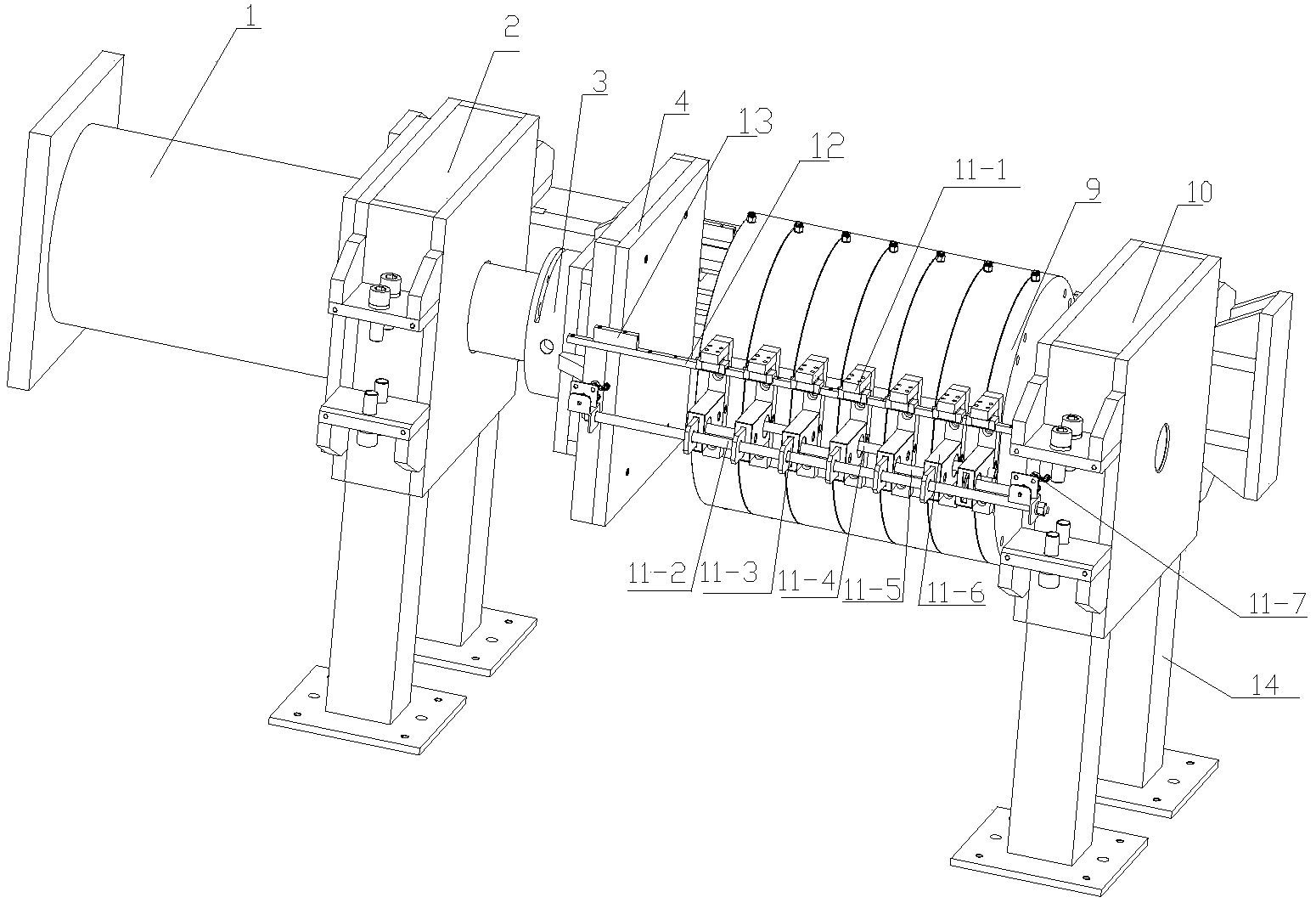
权利要求书
1.一种多腔室污泥高干度脱水装置,包括动力机构(1)、滤板机构、和机架(14),其特征在于:所述的动力机构(1)和滤板机构安装于机架(14)上,所述的滤板机构包括头板(6)、尾板(9)和多块中间滤板(8),所述的头板(6)和与其相邻的中间滤板(8)之间、相邻的中间滤板(8)之间、尾板(9)和与其相邻的中间滤板(8)之间均形成多个压滤腔室;污泥进入所述多个压滤腔室内,通过所述动力机构(1)作用于所述滤板机构,实现压滤脱水。
2.根据权利要求1所述的多腔室污泥高干度脱水装置,其特征在于:所述的中间滤板(8)为凹凸模滤板,中间滤板(8)的凸板嵌入到相邻滤板(8)凹槽内,形成压滤腔室。
3.根据权利要求1所述的多腔室污泥高干度脱水装置,其特征在于:所述脱水装置还包括高压气体组件包括高压气泵(5-1)、气体主管(5-2)和多个气体支管(5-3),所述多个气体支管(5-3)均与所述气体主管(5-2)相连通,所述多个气体支管(5-3)与所有的中间滤板(8)、头板(6)和尾板(9)上的相应进气孔(8-5)连接。
4.根据权利要求1或3所述的多腔室污泥高干度脱水装置,其特征在于:所述多块中间滤板(8)分成若干个滤板组,相邻两个滤板组之间设置一套滤板自调平衡模块,所述滤板自调平衡模块包括凸球头板(7-1)、凹球头板(7-2)和软管(7-3),所述的凸球头板(7-1)横截面的边缘为半球形,所述的凹球头板(7-2)的内壁边缘为球面,所述凸球头板(7-1)与凹球头板(7-2)配合,所述凸球头板(7-1)与凹球头板(7-2)中间开孔,所述的软管(7-3)安装在孔内,所述的凸球头板(7-1)固定在滤板(8)上,凹球头板(7-2)安装在相邻的另一个块中间滤板(8)上。
5.根据权利要求2所述的多腔室污泥高干度脱水装置,其特征在于:所述的滤板位移控制机构包括支架(11-1)、导杆(11-2)、卡位阀板(11-3)和限位阀体(11-6),所述支架(11-1)固定安装在相应中间滤板(8)上,所述限位阀体(11-6)安装在相应的支架(11-1)上,所述卡位阀板(11-3)设置在所述导杆(11-2)上,相邻两个限位阀体(11-6)之间设置有限位柱,在限位时所述卡位阀板(11-3)插入所述限位阀体(11-6)以锁住所述限位柱。
6.根据权利要求5所述的多腔室污泥高干度脱水装置,其特征在于:所述导杆(11-2)与所述滤板机构平行设置,并由导杆驱动气缸(11-7)驱动其运动,实现所述卡位阀板(11-3)插入和拔出所述卡位阀板(11-3)。
7.根据权利要求5所述的多腔室污泥高干度脱水装置,其特征在于:所述限位柱包括内螺栓(11-4)和外螺栓(11-5),限位阀体(11-6)开设有大小不同的两个通孔,其中直径小的孔为螺栓孔,该螺栓孔与内螺栓或外螺栓的螺纹啮合,另一个孔直径超过螺栓头部尺寸,相邻的限位阀体(11-6)上的两个通孔位置相反,所述的卡位阀板(11-3)插入限位阀体(11-6)内,卡位阀板(11-3)根据限位阀体(11-6)对应开设卡孔,所述的卡孔尺寸要求大于螺栓公称直径而小于螺栓头部尺寸,所述的内螺栓(11-4)和外螺栓(11-5)分别安装在限位阀体(11-6)的螺栓孔内。
8.根据权利要求1或2所述的多腔室污泥高干度脱水装置,其特征在于:所述中间滤板(8)包括滤板体(8-6)、衬板(8-3)、加强衬布(8-2)和滤布(8-1),所述的衬板(8-3)和加强衬布(8-2)固定在所述滤板体(8-6)两侧上,所述滤布(8-1)设置在加强衬布(8-2)外侧上,所述的衬板(8-3)上开设有多个通孔和多条通水槽。
9.根据权利要求8所述的多腔室污泥高干度脱水装置,其特征在于:所述的滤板体(8-6)为凹凸模形状,一端结构为凸模结构,另一端为凹模结构,在所述的凸模结构上安装有密封件(15)及刮泥环(16),相邻滤板体(8-6)的凸模结构与凹模结构配合,凸模结构、凹模结构及密封件组成了一个大小可调节的压滤腔室,在所述的滤板体(8-6)上部开设有进气孔(8-5)和通气槽(8-4),下部开设有通水槽(8-7)和出水孔(8-8)。
10.根据权利要求5或6所述的多腔室污泥高干度脱水装置,其特征在于:所述的中间滤板(8)通过支架(11-1)在线性导轨(12)上滑动,所述的线性导轨(12)安装在机架(14)上,所述的线性导轨的端部还安装有限位块(13)。
说明书
多腔室污泥高干度脱水装置
技术领域
本发明涉及污水污泥处理领域,具体地说是一种多腔室污泥高干度脱水装置。
背景技术
污泥高含水率是制约污泥处理处置的瓶颈,含水率高的污泥不仅体积庞大,而且所含的大量有机质、重金属和有害微生物也容易腐化或释放到环境中,引起二次污染,对污泥后续的填埋、焚烧、资源化利用等都造成不利的影响。因此,污泥深度脱水减量化是污泥处理首要目的,减量化是实现污泥其它“三化”的基础,污泥越干,对后续处理处置越有利。
早期污泥常用的脱水设备有板框压滤机、转鼓离心机和带式过滤压滤机,经这些设备脱水后,污泥含水率一般在75%-80%,这些污泥因含水率过高,而造成运输不便且成本较高,而且无法在填埋场直接处置致使干化时间长,污泥中含有的大量有机物及丰富的氮磷钾等营养物,易腐烂产生恶臭造成环境污染。
目前市场上运用较多的污泥深度脱水设备是隔膜板框压滤机,但在脱水时,效率较低,压榨压力仅为1.6MPa,其压榨由高压水泵将污水注入隔膜板框内部,鼓胀隔膜来减小滤室面积,隔膜板框靠板框的塑性变形来挤压;隔膜板框压缩比小,相对工作周期长。另外,市面上常见的弹性压榨板框在结构构造上,过滤板都是一个整体的注塑模件,过滤板容易受损变形,而且损坏后的过滤板需要整体更换,使得维护成本较高,更重要的是,由于结构特点及压榨压力不高,当前采用该隔膜板框压滤机可能将市政污泥压榨脱水至60%左右,比之前的板框压滤机含水率降低不少,主要原因是因为隔膜鼓胀对污泥产生二次压榨,即污泥压滤腔室为可变腔室,但是该设备需要添加绝干泥量30%左右的石灰和铁盐,从而大大增加了污泥的量,而且添加的石灰及氯化铁等会对污泥后续的处理处置带来不利的影响,违背污泥处理处置的减量化及无害化原则。
当前还有一种超高压弹性压榨污泥脱水机,该设备主要包括高压油缸、超高压滤板、配板、弹簧介质、专用滤布、尾板、推板、主梁等组成,该超高压压榨板框包括滤框、滤板、滤布、工作室、弹簧和活塞板,弹簧设置于滤框和滤板之间,活塞板设置在工作室和滤板之间,使得滤板通过活塞板对工作室产生压缩作用。压榨板脱水过程主要分为两级,第一级是由进料泵将物料输送到滤室,进料的同时借助进料泵的压力进行固液分离,即一次过滤脱水;第二级是弹性压榨,设备的一端固定,另一端通过液压油缸施加外界压力,通过弹性传力装置(弹簧)压缩滤室空间对物料进行压榨进行二次脱水。通过对污泥进行超高压压榨,压榨压力在5MPa左右,高压油泵需要提供25-30MPa左右的压力,可将污泥含水率降至50%左右。同样,该超高压弹性压榨机通过设置弹簧来实现对污泥压榨腔室体积的改变来实现超高压挤压,由于弹簧经常完成伸长-压缩等过程,需要承受交变载荷,弹簧容易发生疲劳破坏,弹簧是一种易损件,而且每组板框之间需要10-20个高强度弹簧,50-100块板框则需要将近1000-2000个高强度弹簧,而且,对弹簧进行挤压时还需要克服弹簧初始的弹力作用,二次压榨时污泥所受到实际的压榨压力要比超高压油泵提供给的压力小。例如,进料压力为1MPa时,弹簧必须提供大于1MPa弹力,使得滤板和滤框之间能保持腔室的最大化,当进料压榨结束时,高压泵对污泥进行第二次高压压榨时,必须要克服弹簧开始所具有的弹力,此部分压力为消耗的压力,从而导致高压泵对污泥所产生的压力要小于实际上的压力。
目前市场还有一种超高压隔膜板框压滤机,该设备为在原先的隔膜板框压滤机上的升级,通过在隔膜内注射10MPa的水对污泥提供将近10MPa的压力,也是为二级压榨过程,即开始通过进料压力,然后在隔膜内注射高压液体,对隔膜进行鼓胀进一步对污泥进行压榨脱水,经过该设备脱水后市政污泥含水率可降至50%左右。该设备存在一个主要问题是隔膜在如此高的压力及大变形下,影响隔膜的使用寿命之问题。
通过以上分析,可以看出,要实现污泥的深度脱水必须要实现污泥压榨腔室体积的可变性,同时对污泥进行高压压榨。不管是隔膜板框压滤机还是超高压弹性压榨机都具有污泥压榨腔室的可变性,但是目前污泥深度脱水设备存在以下几个主要问题:(1)普通的隔膜板框压滤机的污泥压榨压力较小,超高压隔膜板框压滤机压榨压力足够,但是隔膜的寿命不高;(2)超高压弹性压榨机依靠弹簧来是实现污泥压榨腔室体积的变化,弹簧易损坏而且会消耗大量的压榨压力;(3)压力越大,在紧贴在滤板上的污泥就越结实,容易形成一层密实的污泥层,该污泥层粘结在滤布上,增大水分排出阻力,影响脱水效果;(4)由于污水污泥具有的高压缩性、高含水率及污水污泥含有毛细水、吸附水及内部水导致的污泥脱水困难的特点,完全采用机械压力很难对污泥进行高深度脱水,使得污泥含水率达到一个较低的水平;(5)所有的压力直接来自于高压油缸的压力,没有经过任何力的放大机构,导致油缸压力及油缸体积过大,对设备密封及的可靠性提出了更高的要求。
发明内容
有鉴于此,本发明针对上述现有技术存在的易损件多,能耗高,油缸压力要求高、脱水后污泥含水率仍较高的技术问题,提出一种易损件少、能耗低,脱水后污泥含水率较低的多腔室污泥高干度脱水装置。
本发明的技术解决方案是,提供一种以下结构的一种多腔室污泥高干度脱水装置,包括动力机构、滤板机构、和机架,所述的动力机构和滤板机构安装于机架上,所述的滤板机构包括头板、尾板和多块中间滤板,所述的头板和与其相邻的中间滤板之间、相邻的中间滤板之间、尾板和与其相邻的中间滤板之间均形成多个压滤腔室;污泥进入所述多个压滤腔室内,通过所述动力机构作用于所述滤板机构,实现压滤脱水。
可选的,所述的中间滤板为凹凸模滤板,中间滤板的凸板嵌入到相邻滤板凹槽内,形成压滤腔室。
可选的,所述脱水装置还包括高压气体组件包括高压气泵、气体主管和多个气体支管,所述多个气体支管均与所述气体主管相连通,所述多个气体支管与所有的中间滤板、头板和尾板上的相应进气孔连接。
可选的,所述多块中间滤板分成若干个滤板组,相邻两个滤板组之间设置一套滤板自调平衡模块,所述滤板自调平衡模块包括凸球头板、凹球头板和软管,所述的凸球头板横截面的边缘为半球形,所述的凹球头板的内壁边缘为球面,所述凸球头板与凹球头板配合,所述凸球头板与凹球头板中间开孔,所述的软管安装在孔内,所述的凸球头板固定在滤板上,凹球头板安装在相邻的另一个块中间滤板上。
可选的,所述的滤板位移控制机构包括支架、导杆、卡位阀板和限位阀体,所述支架固定安装在相应中间滤板上,所述限位阀体安装在相应的支架上,所述卡位阀板设置在所述导杆上,相邻两个限位阀体之间设置有限位柱,在限位时所述卡位阀板插入所述限位阀体以锁住所述限位柱。
可选的,所述导杆与所述滤板机构平行设置,并由导杆驱动气缸驱动其运动,实现所述卡位阀板插入和拔出所述卡位阀板。
可选的,所述限位柱包括内螺栓和外螺栓,限位阀体开设有大小不同的两个通孔,其中直径小的孔为螺栓孔,该螺栓孔与内螺栓或外螺栓的螺纹啮合,另一个孔直径超过螺栓头部尺寸,相邻的限位阀体上的两个通孔位置相反,所述的卡位阀板插入限位阀体内,卡位阀板根据限位阀体对应开设卡孔,所述的卡孔尺寸要求大于螺栓公称直径而小于螺栓头部尺寸,所述的内螺栓和外螺栓分别安装在限位阀体的螺栓孔内。
可选的,所述中间滤板包括滤板体、衬板、加强衬布和滤布,所述的衬板和加强衬布固定在所述滤板体两侧上,所述滤布设置在加强衬布外侧上,所述的衬板上开设有多个通孔和多条通水槽。
可选的,所述的滤板体为凹凸模形状,一端结构为凸模结构,另一端为凹模结构,在所述的凸模结构上安装有密封件及刮泥环,相邻滤板体的凸模结构与凹模结构配合,凸模结构、凹模结构及密封件组成了一个大小可调节的压滤腔室,在所述的滤板体上部开设有进气孔和通气槽,下部开设有通水槽和出水孔。
可选的,所述的中间滤板通过支架在线性导轨上滑动,所述的线性导轨安装在机架上,所述的线性导轨的端部还安装有限位块。
采用以上结构,本发明具有以下优点:(1)通过相邻凹凸模滤板及密封件之间的配合以及滤板位移控制机构,可形成体积任意可变的封闭腔体,适合不同压缩特性的污泥,不存在采用弹簧、隔膜等易损件,提高设备可靠性及使用寿命;(2)单纯的机械方式脱水存在一个极限脱水率,还有部分水分是机械方法所不能去除的,本方案采用了高压气体发生器及组件,通过高压气体作用,将污泥内机械方式难以脱除的水分通过高压气流方式带走,即实现机械压榨及气流双效作用,从而进一步降低污泥的水分,达到污泥深度减量化目的;(3)采用滤板自平衡模块,在一定数量的滤板后设置该自平衡调节模块,当滤板受力不均时,滤板倾斜一定角度,与前端连接的滤板的凸球头板会自动调整到垂直状态,即自适应调节平衡,可保证整个装置的滤板都处于有足够压力的状态