申请日2015.12.24
公开(公告)日2016.06.29
IPC分类号C02F3/30
摘要
本实用新型公开了一种自循环废水生物处理反应装置,解决了现有的废水生物处理设施存在的占地面积大、投资大、运行成本高等问题。技术方案包括顶面开口的外筒和内筒,所述外筒被径向设置的多块溢流隔板均匀分隔成多个交错布置的外好氧区和外缺氧区,所述外好氧区底部的外筒筒壁上设外曝气头、污泥入口和进水口,所述外缺氧区底部的内筒筒壁上设有内筒进水孔;所述内筒经环形溢流板分隔成内筒内层的内好氧区和内筒外层的内缺氧区,所述内好氧区底部设有内曝气头,所述内缺氧区顶部内筒筒壁上设有与外界相通的出水管。本实用新型结构简单紧凑,运行可靠、占地面积少、节省材料、维护量少、投资成本低。
摘要附图
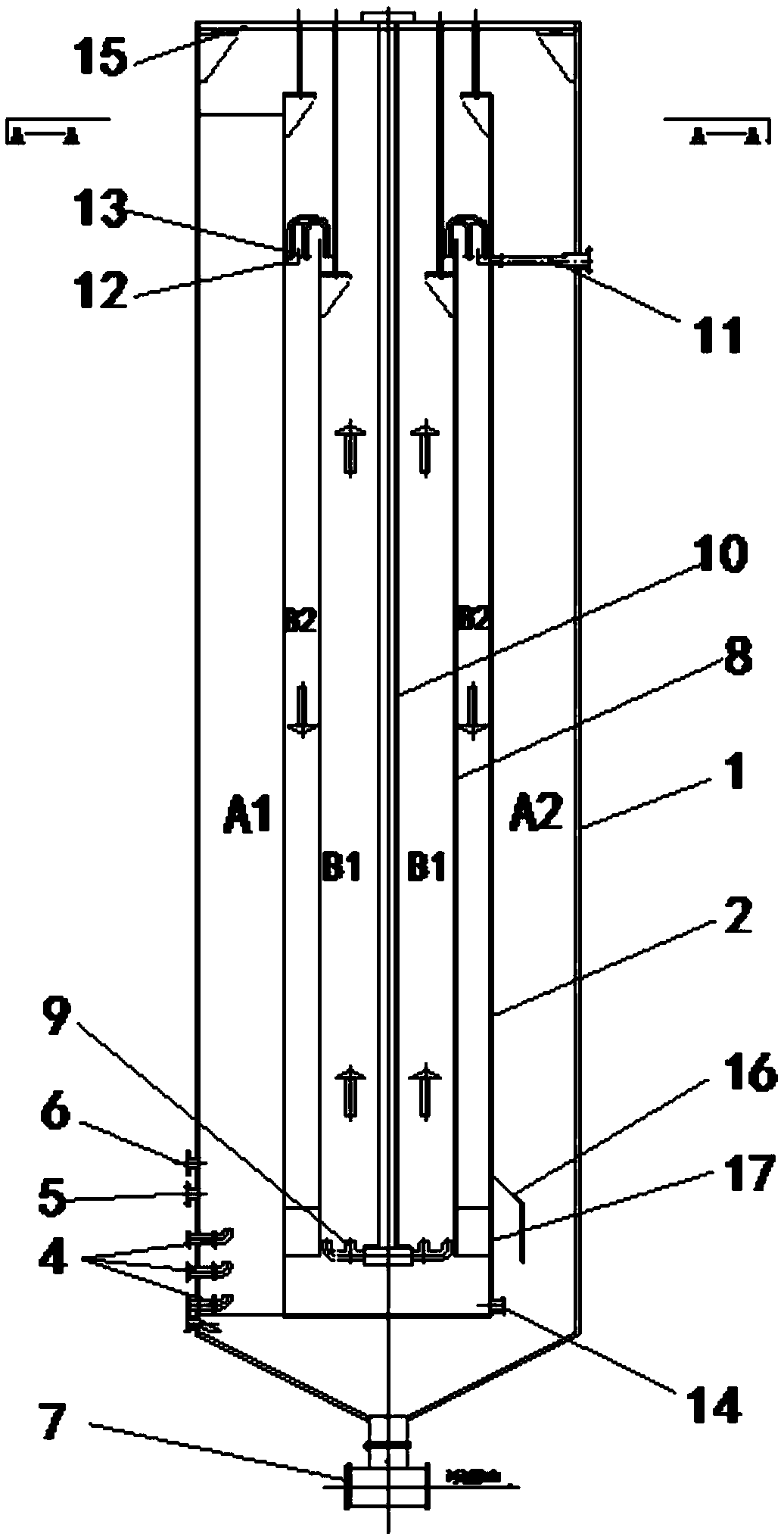
权利要求书
1.一种自循环废水生物处理反应装置,包括顶面开口的外筒和内筒,其特征在于,所述外筒被径向设置的多块溢流隔板均匀分隔成多个交错布置的外好氧区和外缺氧区,所述外好氧区底部的外筒筒壁上设外曝气头、污泥入口和进水口,所述外缺氧区底部的内筒筒壁上设有内筒进水孔,所述外好氧区和外缺氧区的底部相通;所述内筒经环形溢流板分隔成内筒内层的内好氧区和内筒外层的内缺氧区,所述内好氧区底部设有内曝气头,所述内缺氧区顶部内筒筒壁上设有与外界相通的出水管,所述内好氧区和内缺氧区底部相通。
2.如权利要求1所述的自循环废水生物处理反应装置,其特征在于,所述出水管的入口处设有环形的出水槽,所述环形的出水槽的进水口处设有齿型溢流堰。
3.如权利要求1所述的自循环废水生物处理反应装置,其特征在于,所述内筒进水孔的上方设有折流板。
4.如权利要求1所述的自循环废水生物处理反应装置,其特征在于,所述外好氧区底部的外筒筒壁设有多层外曝气头,所述外曝气头上方设污泥入口,所述污泥入口的上方设进水口。
5.如权利要求1-4任一项所述的自循环废水生物处理反应装置,其特征在于,所述外筒底面的污泥排出口经管道与所述污泥入口连接。
6.如权利要求1-4任一项所述的自循环废水生物处理反应装置,其特征在于,所述内曝气头与输气管连接,所述输气管经螺杆吊装在外筒顶部。
7.如权利要求1-4任一项所述的自循环废水生物处理反应装置,其特征在于,所述内筒经螺杆吊装在外筒顶部。
8.如权利要求1-4任一项所述的自循环废水生物处理反应装置,其特征在于,所述环形溢流板经螺杆吊装在外筒顶部。
9.如权利要求1所述的自循环废水生物处理反应装置,其特征在于,所述出水管的入口处高度比外筒的最高水位低0.5-1.5米。
说明书
自循环废水生物处理反应装置
技术领域
本实用新型涉及废水处理领域,具体的说是一种自循环废水生物处理反应装置。
背景技术
现有的废水生物处理工艺多采用功能单一的生物反应池进行串联组合,特别是对难处理的有机废水,如焦化废水,其生物处理由最初的一级简易活性污泥处理工艺发展到现在的多级好氧-缺氧/厌氧处理工艺。随着焦化废水生物处理工艺路线的延长,焦化废水停留时间由当初简易活性污泥法的20多个小时,延长到目前处理工艺的80个小时以上,有的甚至近200小时。如此长的处理工艺路线导致水处理过程中存在以下问题:
⑴工艺流程长、设备多、设施占地面积大、投资大;
⑵现有焦化废水生物处理系统对总氮去除效果差,在反硝化单元需补充碳源,运行成本高;
⑶针对低COD、低C/N的焦化区域焦化废水以及生活污水,现有处理技术受碳源不足的制约,无法正常启动运行;
⑷现有焦化废水生物处理系统污泥量大、碱源消耗大;
⑸现有焦化废水生物处理设施封闭性差,暴露于大气环境下的水面面积大,水体的VOC挥发量大,对大气污染程度高;
⑹现有焦化废水生物处理技术工艺路线长、焦化废水停留时间长,不便操作、控制及管理;
⑺现有焦化废水生物处理设施维护工作量大,维护成本高;
⑻现有焦化废水生物处理设施管线长、接点多,跑、冒、滴、漏现象严重。
发明内容
本实用新型的目的是为了解决上述技术问题,提供一种结构简单紧凑,运行可靠、占地面积少、维护量少、投资成本和运行成本低的自循环废水生物处理反应装置。
技术方案包括顶面开口的外筒和内筒,所述外筒被径向设置的多块溢流隔板均匀分隔成多个交错布置的外好氧区和外缺氧区,所述外好氧区底部的外筒筒壁上设外曝气头、污泥入口和进水口,所述外缺氧区底部的内筒筒壁上设有内筒进水孔,所述外好氧区和外缺氧区的底部相通;所述内筒经环形溢流板分隔成内筒内层的内好氧区和内筒外层的内缺氧区,所述内好氧区底部设有内曝气头,所述内缺氧区顶部内筒筒壁上设有与外界相通的出水管,所述内好氧区和内缺氧区底部相通。
所述出水管的入口处设有环形的出水槽,所述环形的出水槽的进水口处设有齿型溢流堰。
所述内筒进水孔的上方设有折流板。
所述外好氧区底部的外筒筒壁设有多层外曝气头,所述外曝气头上方设污泥入口,所述污泥入口的上方设进水口。
所述外筒底面的污泥排出口经管道与所述污泥入口连接。
所述内曝气头与输气管连接,所述输气管经螺杆吊装在外筒顶部。
所述内筒经螺杆吊装在外筒顶部。
所述环形溢流板经螺杆吊装在外筒顶部。
所述出水管的入口处高度比外筒的最高水位低0.5-1.5米。
针对背景技术中存在的问题,发明人对现有的短程硝化反硝化工艺进行改进:短程硝化反硝化的核心是如何将硝化过程控制在亚硝酸阶段,本实用新型根据亚硝酸菌具有类似碳氧化菌的饱食—饥饿的特性,即能适应溶解氧周期性的波动,而硝酸菌不能适应此波动的原理,提出通过控制曝气量以调控焦化废水中的溶解氧(DO),利用亚硝酸菌和硝酸菌对DO的亲和力不同这一特性,将硝酸菌淘洗出系统,从而实现短程硝化反硝化过程。因而对焦化废水采用高溶解氧曝气处理、低溶解氧反应、缺氧反应的过程能够实现上述过程,通过上述至少一次反应周期的循环,从而实现亚硝酸菌和异养型反硝化菌等优势菌群的培养,以及硝酸菌等菌群的淘汰,提高出水总氮去除率,减少污泥消耗和碱源消耗,对于低COD、低C/N的焦化区域焦化废水也同样适用,上述循环仅涉及到三个反应过程,因此缩短工艺流程、降低设备投资和运行成本。
进一步的,废水及污泥在各阶段中不同溶解氧浓度下的停留时间对出水总氮去除率具有影响,所述焦化废水在高溶解氧曝气处理阶段的停留时间为8-12h,控制该步骤中混合液(焦化废水与污泥混合后形成的混合液)的溶解氧浓度DO>4mg/L,在高溶解氧的曝气下,在污泥中微生物的作用下,进行氨氮的硝化分解、反硝化和有机物的降解;在低溶解氧反应阶段的停留时间为2-3h,控制该步骤中的混合液的溶解氧浓度DO<2mg/L,焦化废水和污泥在低溶解氧条件下进行好氧生物反应,随着反应的进行,溶解在混合液中的氧耗尽,从而进入下一阶段的反应;在缺氧反应阶段的停留时间为7-9h。通过焦化废水停留时间和混合液的溶解氧浓度的控制可以尽可能多的使硝酸菌被抑制并洗出系统,同时有利于亚硝酸菌和异养型反硝化菌等优势菌群的培养,从而提高废水总氮去除率。以检测出水总氮去除率作为指标,上述高溶解氧曝气处理、低溶解氧反应、缺氧反应的循环过程可根据需要进行两次或两次以上。
进一步的,本实用新型工艺在本实用新型特别研制的自循环生物处理反应器中进行,将多个反应阶段集中到一个反应器中,可满足多次循环的要求,大大减少了占地面积、池容小,操作控制难度小。
本实用新型的自循环生物处理反应器具有以下特点:内筒和外筒的结构各自满足完整的自循环过程,在外筒中,外筒通过径向设置的溢流隔板分为多个相邻的底部相通的外好氧区和外缺氧区,使含有焦化废水和污泥的混合液在外好氧区和外缺氧区间流动;在外好氧区中设置外曝气头,该外曝气头设置在污泥入口和进水口的下方,在提供条件要求的溶解氧浓度的基础上,还为污泥和焦化废水提供混合流动的动力,在气流作用下,含焦化废水和污泥的混合液可以由外好氧化向外缺氧区流动,并且,由于外好氧区和外缺氧区相邻设置,因此外好氧区的混合液经高溶解氧曝气处理后,可通过溢流的方式将混合液中的大部分气体排出,而进入外缺氧区,通过低溶解氧反应后,混合液中的氧被反应消耗,进入外缺氧区下段后从而可自然进行缺氧反应,而外筒中外厌氧区和外好氧区的的底部相通结构,气流作用又可以使上述混合液形成一个固定流向,上述反应过程可不断循环。
由于多个溢流隔板将外筒分隔成多个外好氧区和外缺氧区,因此焦化废水和淤泥可被分成多份同时处理,混合反应效果好。
在外缺氧区底部的内筒筒壁上设有内筒进水孔,在压差的作用下,部分混合液可以通过内筒进水孔将外筒的外缺氧区内的混合液引入内筒内,由于内筒进水孔的上方设有折流板的存在,形成了污泥和废水的沉降分散区域,从而降低了进入内筒的混合液中的污泥浓度,提高污泥在外筒内的循环量,减少内筒污泥的堆积。所述内筒被环形溢流板分隔成内筒内层的内好氧区和内筒外层的内缺氧区,所述内好氧区内筒底部设有内曝气头,同时在内曝气头喷出的含氧的气体作用下,混合液先进入内筒内层的内好氧区进行高溶解氧曝气处理,然后溢流通过环形溢流板进入内筒外层的内缺氧区上段进行低溶解氧反应,再继续下行进入内筒外层的内缺氧区下段进行缺氧反应,由于内好氧区和内缺氧区底部相通,气流作用可以使上述混合液形成一个固定流向,上述反应过程可不断循环。
所述内缺氧区顶部内筒筒壁上设有与外界相通的出水管,该出水管入口高度低于外筒的最高水位,优选所述出水管的入口处高度比外筒的最高水位低0.5-1.5米,因此可在内、外筒形成压力差,使内筒内反应后的混合液由出水管引出。
所述输气管、内筒、环形溢流板均分别经螺杆吊装在外筒顶部,通过螺杆调整所述输气管的高度,从而相应调整内曝气头的高度,控制内好氧区与内缺氧区之间混合液的循环量,回流比控制在100-150%,若回流比小于100%,则相应调低内曝气头的高度;通过螺杆调整所述内筒的高度,以控制外好氧区与外缺氧区混合液的循环量,达到回流比为100-150%,若回流比小于100%,相应调高内筒,从而提升出水口高度,减少进内筒废水量;若回流量过高,相应调低内筒,增加进内筒废水量。通过螺杆调整环形溢流板在内筒液面中的深度,以控制内筒内混合液中的污泥浓度为3-6g/L,当污泥浓度过低时,可适当调高环形溢流板,反之,则调低环形溢流板。
上述反应工艺全部在一个反应器内进行,各反应阶段的反应时间、溶解氧浓度、混合液的循环量均可灵活控制,操作非常简便可靠,实验表明,采用本发明方法不仅可以将硝酸菌淘洗出系统,有效保留亚硝酸菌,且无需连续补充碱源。
有益效果:
⑴本实用新型中进水口与曝气气流入水点在同一区域,形成泥水的混合液的自循环过程,有利于提高气液混合效率、强化传质效果;内筒和外筒之间实现独立的自循环过程,进一步提高混合效率,通过交替改变混合液中的溶解氧浓度及污泥在不同阶段下的停留时间,从而实现亚硝酸菌和异养型反硝化菌等优势菌群的培养,以及硝酸菌等菌群的淘汰,提高总氮转化率。
⑵现有焦化废水A/O脱氮工艺经历了硝化和反硝化过程,工艺过程复杂、流程长、设备多;采用本实用新型减少了硝酸菌将氧化成及反硝化菌将还原成的过程,短缩了工艺过程、降低了设备投资和占地面积。
⑶本实用新型通过高、低溶解氧曝气,可以培养出异养硝化好氧反硝化菌优势菌群,它以有机物作为碳源,无论是硝化阶段还是反硝化阶段,都能有效降解废水中的有机物,总氮及COD的去除率高。
⑷现有焦化废水A/O脱氮工艺中,需不断补充碱源,以调节废水中的pH,同时为自养菌提供电子受体。本实用新型通过高、低溶解氧曝气-缺氧过程,抑制了自养亚硝酸菌,有利于异养亚硝酸菌的生长,低碱度的环境更有利于提高该菌种的活性,因此不需不断的补充碱源,减少了碱源的添加量。
⑸本实用新型反应器设施封闭性高,暴露于大气环境下的水面面积小,减轻了因水体中VOC的挥发对大气环境的污染,对环境友好。
⑹设备外表面面积小,便于设备保温处理。设备内部无运动部件,不需维护,设施操作、控制及管理方便,维护工作量小,维护成本低。
⑺本实用新型结构简单紧凑,运行可靠、占地面积少、节省材料、维护量少、投资成本低,废水处理效果好。