申请日2016.02.26
公开(公告)日2016.06.15
IPC分类号C11C3/04; C10L1/02
摘要
本发明涉及一种强化剩余污泥微生物富集产脂制备生物柴油的方法,包括以下几个步骤:(1)将剩余污泥放入培养基中,加入FeCl3后搅拌发酵;(2)发酵结束后分离、冷干得到污泥干粉;(3)采用均质-酸热-有机溶剂法提取步骤(2)所得污泥干粉中的微生物油脂;(4)将步骤(3)所得微生物油脂进行三氟化硼甲酯化法转化,即得生物柴油。与现有技术相比,本发明碳源转化率高、生物柴油制备效率佳、生产成本低,为剩余污泥的处理提供一条新的具有高附加值的资源化途径。
摘要附图
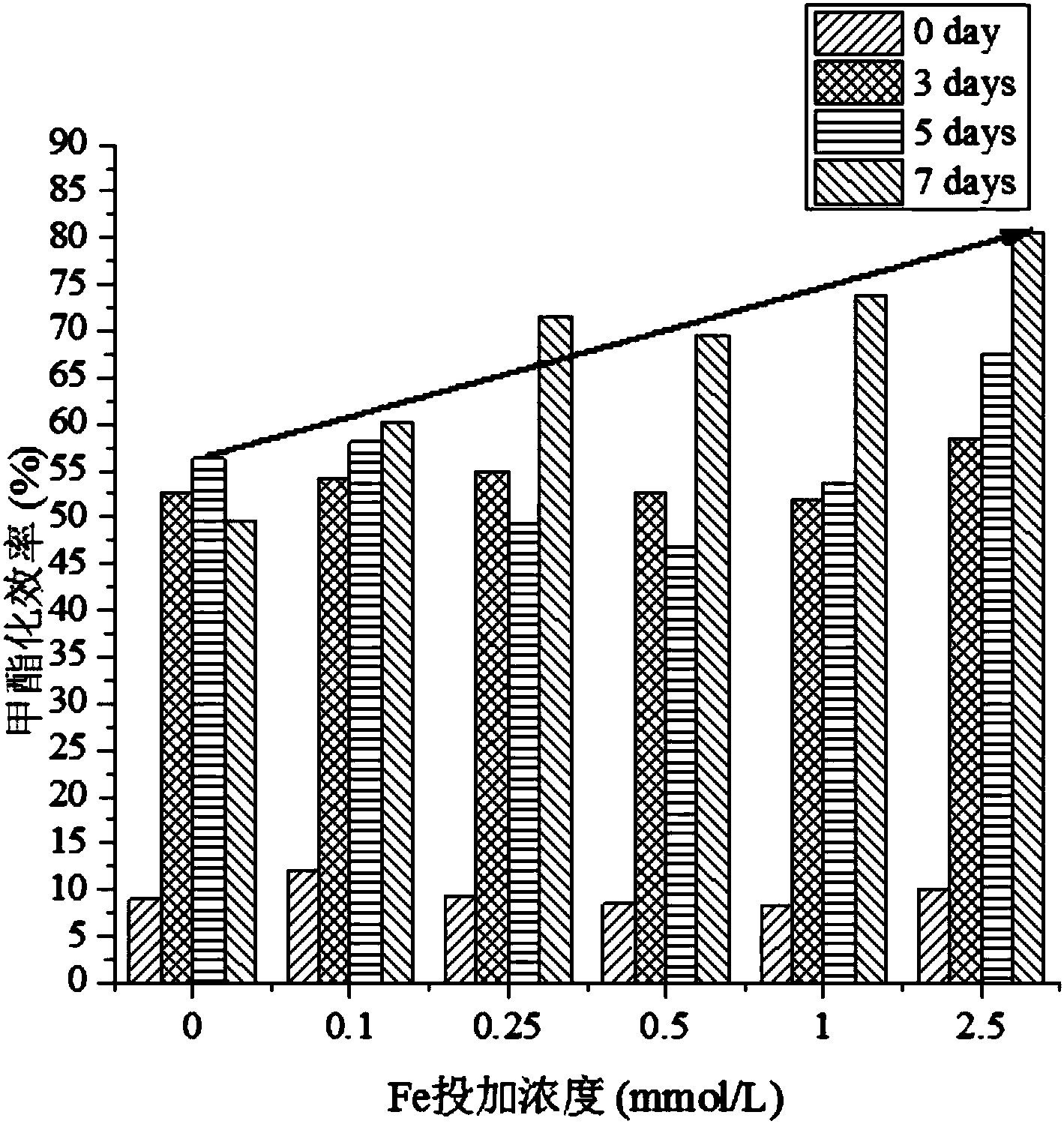
权利要求书
1.一种强化剩余污泥微生物富集产脂制备生物柴油的方法,其特征在于,该方法包括以下几个步骤:
(1)将剩余污泥放入培养基中,加入铁源后搅拌发酵;
(2)发酵结束后分离、冷干得到污泥干粉;
(3)采用均质-酸热-有机溶剂法提取步骤(2)所得污泥干粉中的微生物油脂;
(4)将步骤(3)所得微生物油脂进行三氟化硼甲酯化法转化,即得生物柴油。
2.根据权利要求1所述的一种强化剩余污泥微生物富集产脂制备生物柴油的方法,其特征在于,所述的剩余污泥为来源于采用生物法处理污水的污水处理厂。
3.根据权利要求1所述的一种强化剩余污泥微生物富集产脂制备生物柴油的方法,其特征在于,所述的铁源为FeCl3。
4.根据权利要求1所述的一种强化剩余污泥微生物富集产脂制备生物柴油的方法,其特征在于,所述的培养基包括碳源、氮源、缓冲液和痕量金属,其中碳源包括葡萄糖、木糖或蔗糖中的一种或几种,氮源为(NH4)2SO4,碳源与氮源的质量比为(70~150):1,碳源的浓度为30~60g/L,缓冲液包括K2HPO4和NaH2PO4﹒2H2O,其含量分别为1~2g/L和1~3g/L,痕量金属的添加量为3~10mL,培养基的pH为2.0~5.0,剩余污泥最终接种浓度MLVSS为2~3g/L。
5.根据权利要求4所述的一种强化剩余污泥微生物富集产脂制备生物柴油的方法,其特征在于,所述的痕量金属按以下比例配制而成:1L蒸馏水添加1~2mL质量分数25%的盐酸、50~100mgZnCl2、80~150mgMnCl2﹒4H2O、50~100mgH3BO3、100~300mgCoCl2﹒6H2O、10~50mgCuCl2﹒2H2O、10~50mgNiCl2﹒6H2O、10~50mgNaMoO4﹒2H2O。
6.根据权利要求1所述的一种强化剩余污泥微生物富集产脂制备生物柴油的方法,其特征在于,所述发酵的温度为25~35℃,搅拌的转速为150~200rpm,发酵时间为5~7天。
7.根据权利要求1所述的一种强化剩余污泥微生物富集产脂制备生物柴油的方法,其特征在于,所述铁源的添加量为使培养基中Fe3+的浓度为0.1~2.5mmol/L。
8.根据权利要求1所述的一种强化剩余污泥微生物富集产脂制备生物柴油的方法,其特征在于,步骤(2)所述的分离采用离心分离,被分离发酵液体积为30~50mL,转速为3000~5000rpm,离心时间为10~20min,所述的冷干为在-50~-80℃下冷冻1~2h,然后在冷干机内冷干18~24h,冷干机内温度为-50~-80℃。
9.根据权利要求1所述的一种强化剩余污泥微生物富集产脂制备生物柴油的方法,其特征在于,步骤(3)所述采用均质-酸热-有机溶剂法提取污泥干粉中的微生物油脂包括以下几个步骤:
(a)向管中加入玻璃珠至约与下端线平,制得均质小管;
(b)称取污泥干粉至均质小管中,记录重量,然后向其中加入甲醇,加入的污泥干粉的重量与甲醇的体积比为(0.1~0.2)g:(0.5~1.0)mL混合均匀后所得溶液于0~5℃温度下放置6~24h;
(c)用均质器在最高档下均质5~10s,然后用氯仿将均质小管中溶液转移至空瓶中;
(d)往空瓶中加入浓度为3~5mol/L的盐酸,加入盐酸的体积与空瓶中甲醇的体积比为(10~20):(0.5~1)在多管震荡器上以2500rpm的转速震荡30~60min,100℃沸水浴10~15min,-20℃速冷30~60min,然后将混合溶液转移至离心管内;
(e)在离心管内加入等体积混合的甲醇与氯仿混合液,加入体积与离心管内甲醇体积比为(20~30):(0.5~1),在多管震荡器上以2500~3000rpm的转速震荡30~60min,以4000~5000rpm的转速离心10~15min,然后取氯仿层待用,重复本步骤,并将氯仿层合并;
(f)加入与步骤(e)所得氯仿层等体积的质量分数为0.1~0.25%的NaCl溶液,混匀后离心,萃取氯仿层,40℃旋转蒸发10~15min,即得微生物油脂。
10.根据权利要求1所述的一种强化剩余污泥微生物富集产脂制备生物柴油的方法,其特征在于,步骤(4)所述微生物油脂进行三氟化硼甲酯化法转化,包括以下步骤:
(Ⅰ)将微生物油脂置于氮吹仪下吹扫,得到脂质置于容器中;
(Ⅱ)在容器中加入浓度为0.3~0.7mol/L的氢氧化钠甲醇溶液,加入的氢氧化钠甲醇溶液体积与脂质的质量之比为(8~10)mL:(0.02~0.04)g,然后导入氮气将容器中的空气排尽,然后将容器置于多管震荡器上震荡5~10min,然后于80℃恒温水槽中水浴30~60min,直至油滴消失,期间每30s~60s缓慢摇动容器,以防止氢氧化钠形成固态附着在瓶壁上,水浴完毕待顶空瓶冷却至室温;
(Ⅲ)往容器中加入0.5~1mol/L的盐酸甲醇溶液和10~15%(m/v)BF3甲醇溶液,盐酸甲醇溶液与BF3甲醇溶液的加入体积与脂质的质量之比均为(8~10)mL:(0.02~0.04)g;导入干燥氮气将容器中空气排掉,然后将容器置于多管震荡器上震荡5~10min,然后于80℃恒温水槽中水浴30~60min,冷却至室温;
(Ⅳ)加入饱和氯化钠溶液和色谱级异辛烷,饱和氯化钠溶液的加入量与脂质的加入量之比为(2~4)mL:(0.02~0.04)g,色谱级异辛烷的加入量与脂质的加入量之比为(8~20)mL:(0.02~0.04)g;将该溶液置于多管震荡器上震荡10~15min后,于4000~5000rpm下离心15~20min,取上层异辛烷相即为生物柴油。
说明书
一种强化剩余污泥微生物富集产脂制备生物柴油的方法
技术领域
本发明涉及污泥资源化领域,具体涉及一种强化剩余污泥微生物富集产脂制备生物柴油的方法。
背景技术
现今世界,人类对燃料(fuel)的需求与日俱增,而常规燃料主要来源于石油、天然气等不可再生能源。世界正在面临严峻的能源危机。为应对这一危机,自2008年以来,以生物柴油(biodiesel)作为传统燃料的研究成为了能源研究领域的一大热点。新的研究表明,初沉和二沉污泥含有脂类物质,因此可作为用于生物柴油生产的潜在的原料。然而在污水处理厂正常的操作条件下,由于受进水低碳、高氮条件的影响,剩余污泥中微生物不能有效地将碳源以脂质的形式储存在自身体内,因此直接对剩余污泥进行提取油脂制备生物柴油,油脂含量和生物柴油产量低,生物柴油制备效率不佳导致提取成本过高。基于此,提高剩余污泥油脂含量将会大大加强其作为生产生物柴油原料的竞争力。
经研究表明,在最佳pH和最佳C/N的培养条件下,发酵至第5天左右通过改进酸热油脂提取法使得最终制备的生物柴油的制备效率较原始污泥大幅度提高,甲酯化效率和单位质量干污泥生物柴油制备效率分别达36.92%和13.06%,分别是原始污泥的4.55倍和8.7倍,初步达到了Dufreche等认为“酯化的脂肪酸甲酯含量达到10%以上,油脂提取才更具有经济价值”这一标准,但是相应的单位质量碳源转化为生物柴油的效率却不尽如人意,仅为4%左右,而培养基中投加碳源的成本所占比例又是极高的,为进一步满足生物柴油合成的技术经济的要求,除油脂提取方法、培养条件pH和C/N优化措施外,仍需采取其他措施改善碳源转化率亦或进一步提高生物柴油的制备效率。
发明内容
本发明的目的就是为了克服上述现有技术存在的缺陷而提供一种碳源转化率高、生物柴油制备效率佳、生产成本低的采用FeCl3强化剩余污泥微生物富集产脂制备生物柴油的方法,同时为剩余污泥的处理提供一条新的具有高附加值的资源化途径。
本发明的目的可以通过以下技术方案来实现:一种强化剩余污泥微生物富集产脂制备生物柴油的方法,包括以下几个步骤:
(1)将剩余污泥放入培养基中,加入FeCl3后搅拌发酵;
(2)发酵结束后分离、冷干得到污泥干粉;
(3)采用均质-酸热-有机溶剂法提取步骤(2)所得污泥干粉中的微生物油脂;
(4)将步骤(3)所得微生物油脂进行三氟化硼甲酯化法转化,即得生物柴油。
所述的剩余污泥为来源于采用生物法处理污水的污水处理厂。
所述的培养基包括碳源、氮源、缓冲液和痕量金属,其中碳源包括葡萄糖、木糖或蔗糖中的一种或几种,氮源为(NH4)2SO4,碳源与氮源的质量比为(70~150):1,碳源的浓度为30~60g/L,缓冲液包括K2HPO4和NaH2PO4﹒2H2O,其含量分别为1~2g/L和1~3g/L,痕量金属的添加量为3~10mL,培养基的pH为2.0~5.0,剩余污泥最终接种浓度MLVSS为2~3g/L。
所述的痕量金属按以下比例配制而成:1L蒸馏水添加1~2mL25%HCl、50~100mgZnCl2、80~150mgMnCl2﹒4H2O、50~100mgH3BO3、100~300mgCoCl2﹒6H2O、10~50mgCuCl2﹒2H2O、10~50mgNiCl2﹒6H2O、10~50mgNaMoO4﹒2H2O。
所述发酵温度为通常微生物最适生长的温度,即25~35℃;此外,为保证培养过程中培养基内含有适量的溶解氧,摇床搅拌的转速为150~200rpm,发酵时间为5~7天。
所述的FeCl3的添加量为使培养基中Fe3+的浓度为0.1~2.5mmol/L。Fe3+作为铁元素的一种存在形式,在水中容易水解,并且随着pH不同可以生成不同电荷的络合阳离子和络合阴离子,因其水解产生的无机物质可以和金属氢氧化物发生共沉现象,可去除某些对微生物生长过程中重要酶产生抑制作用的重金属。而且铁不仅是微生物氧化酶体系的重要组成部分,可以和细胞色素配合反应,在氧化底物的过程中起到电子传递的作用,又和微生物有非常强的亲和力,对微生物的繁殖以及酶分泌起到一定的促进作用。目前有关铁在产油微生物纯菌培养过程中的促产作用已有报道,例如Liu等考察铁离子对产油微藻生长和油脂积累的影响,表明FeCl3添加量为1.2×10-5mol/L时,油脂产量最高(56.6%),是较低浓度FeCl3产量的3~7倍。
步骤(2)所述的分离采用离心分离,被分离发酵液体积为30~50mL,转速为3000~5000rpm,离心时间为10~20min,所述的冷干为在-50~-80℃下冷冻1~2h,然后在冷干机内冷干18~24h,冷干机内温度为-50~-80℃。
步骤(3)所述采用均质-酸热-有机溶剂法提取污泥干粉中的微生物油脂包括以下几个步骤:
(a)向管中加入玻璃珠至约与下端线平,制得均质小管;
(b)称取污泥干粉至均质小管中,记录重量,然后向其中加入甲醇,加入的污泥干粉的重量与甲醇的体积比为(0.1~0.2)g:(0.5~1.0)mL混合均匀后所得溶液于0~5℃温度下放置6~24h;
(c)用均质器在最高档下均质5~10s,然后用氯仿将均质小管中溶液转移至空瓶中;
(d)往空瓶中加入浓度为3~5mol/L的盐酸,加入盐酸的体积与空瓶中甲醇的体积比为(10~20):(0.5~1)在多管震荡器上以2500rpm的转速震荡30~60min,100℃沸水浴10~15min,-20℃速冷30~60min,然后将混合溶液转移至离心管内;
(e)在离心管内加入等体积混合的甲醇与氯仿混合液,加入体积与离心管内甲醇体积比为(20~30):(0.5~1),在多管震荡器上以2500~3000rpm的转速震荡30~60min,以4000~5000rpm的转速离心10~15min,然后取氯仿层待用,重复本步骤,并将氯仿层合并;
(f)加入与步骤(e)所得氯仿层等体积的质量分数为0.1~0.25%的NaCl溶液,混匀后离心,萃取氯仿层,40℃旋转蒸发10~15min,即得微生物油脂。
步骤(4)所述微生物油脂进行三氟化硼甲酯化法转化,包括以下步骤:
(Ⅰ)将微生物油脂置于氮吹仪下吹扫,得到脂质置于容器中;
(Ⅱ)在容器中加入浓度为0.3~0.7mol/L的氢氧化钠甲醇溶液,加入的氢氧化钠甲醇溶液体积与脂质的质量之比为(8~10)mL:(0.02~0.04)g,然后导入氮气将容器中的空气排尽,然后将容器置于多管震荡器上震荡5~10min,然后于80℃恒温水槽中水浴30~60min,直至油滴消失,期间每30s~60s缓慢摇动容器,以防止氢氧化钠形成固态附着在瓶壁上,水浴完毕待顶空瓶冷却至室温;
(Ⅲ)往容器中加入0.5~1mol/L的盐酸甲醇溶液和10~15%(m/v)BF3甲醇溶液,盐酸甲醇溶液与BF3甲醇溶液的加入体积与脂质的质量之比均为(8~10)mL:(0.02~0.04)g;导入干燥氮气将容器中空气排掉,然后将容器置于多管震荡器上震荡5~10min,然后于80℃恒温水槽中水浴30~60min,冷却至室温;
(Ⅳ)加入饱和氯化钠溶液和色谱级异辛烷,饱和氯化钠溶液的加入量与脂质的加入量之比为(2~4)mL:(0.02~0.04)g,色谱级异辛烷的加入量与脂质的加入量之比为(8~20)mL:(0.02~0.04)g;将该溶液置于多管震荡器上震荡10~15min后,于4000~5000rpm下离心15~20min,取上层异辛烷相即为生物柴油。
与现有技术相比,本发明的有益效果体现在以下几方面:
1.本发明所采用的FeCl3廉价易得,且投加量极其微少,不会造成二次污染。
2.在剩余污泥中投加极低浓度的FeCl3(以Fe3+计)即可使污泥甲酯化效率、生物柴油的产量和制备效率、碳源转化率大幅提高,特别是可使生物柴油的产量较原始污泥和空白组污泥分别提高42倍和0.9倍。
3.本发明不仅为生物柴油的制备提供了一种新的廉价原料来源,而且为生活污水处理厂剩余污泥的资源化提供了一条新的途径,且资源化产物的附加值高。