申请日2016.08.31
公开(公告)日2017.01.04
IPC分类号C02F9/04; B01D53/78; B01D53/75; B01D53/96; B01D53/52; B01D53/58; C01C1/242; C01B17/22
摘要
本发明涉及一种炼油加氢工艺产生的废水的脱硫脱氨处理方法,包括对废水依次进行脱硫及硫回收处理步骤和脱氨及氨回收处理步骤。本发明获得的对炼油加氢工艺产生的废水的脱硫脱氨处理方法,以pH值作为关键的调控因素,实现各处理环节的有机结合,高效脱除废水中的硫和氨氮污染,使处理后废水中硫与氨氮含量达到GB8978‑1996《污水综合排放标准》中的二级排放标准要求,并将脱除的硫、氨氮转化为可再利用的化工产品,在经济价值和环保方面均具有显著的效益,实现绿色化工。此外,本发明提供的处理装置,更利于本发明处理方法的操作及运行控制,方便、高效地实现对废水的脱硫、脱氨氮处理及回收。
摘要附图
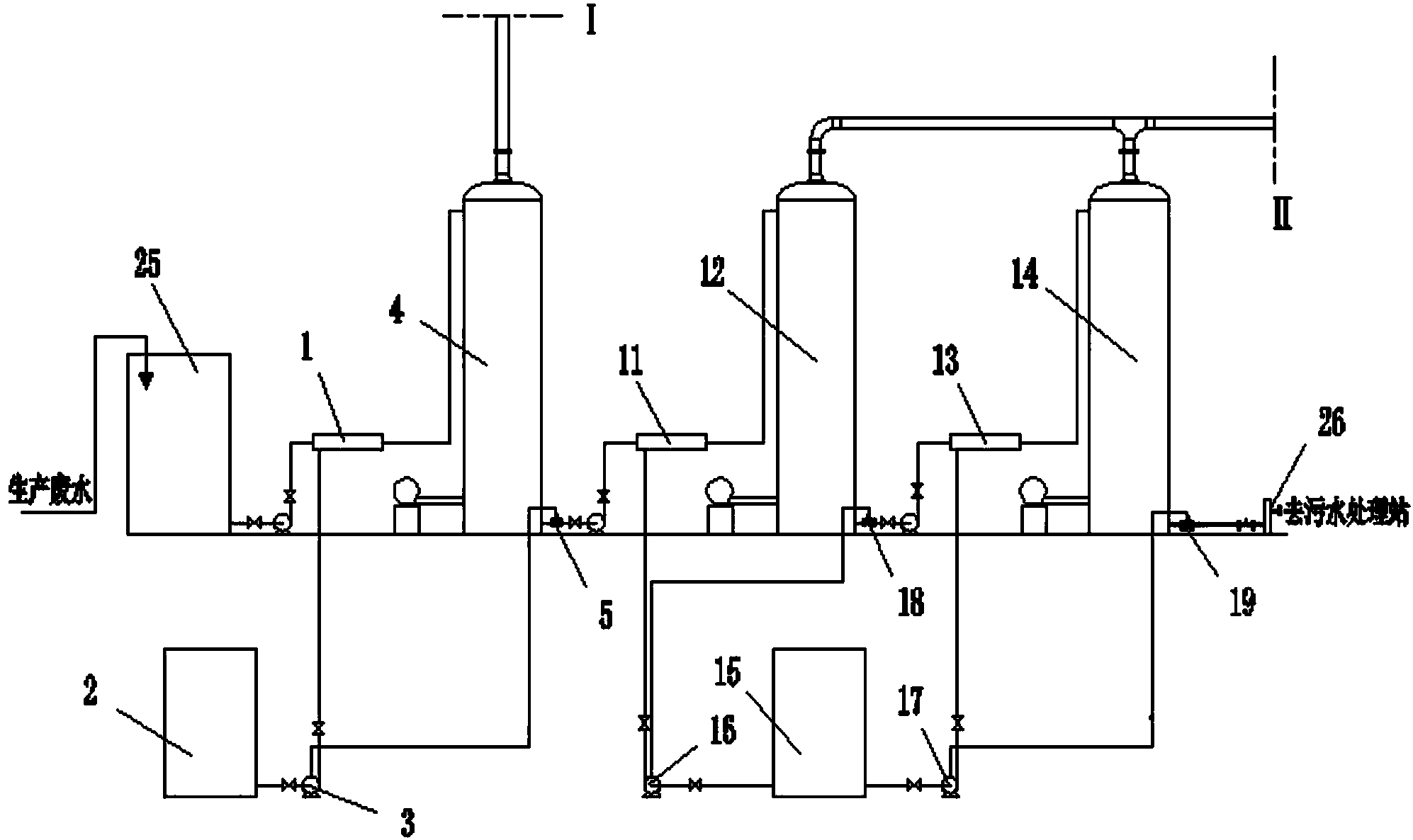
权利要求书
1.一种炼油加氢工艺产生的废水的脱硫脱氨处理方法,其特征在于,包括以下步骤:
a、脱硫及硫回收处理步骤:
a1、脱硫处理步骤:向炼油加氢工艺产生的废水加入稀硫酸溶液Ⅰ,调节酸碱度后喷淋,与空气逆向接触进行空气吹脱脱硫处理,脱硫后的废水输送至脱氨处理步骤;所述脱硫后废水的pH值控制为0.8~1.2;所述稀硫酸溶液Ⅰ中H2SO4的质量含量为30%~50%;
a2、硫回收处理步骤:将经过所述脱硫处理步骤后逸出的气体经过两级脱硫吸收处理后排放,所述两级脱硫吸收处理包括由循环喷淋的一级脱硫吸收液对经过所述脱硫处理步骤后逸出的气体进行第一级脱硫吸收处理步骤,以及由循环喷淋的二级脱硫吸收液和补充喷淋的NaOH溶液Ⅰ对经过所述第一级脱硫吸收处理步骤后逸出的气体进行第二级脱硫吸收处理步骤;控制一级脱硫吸收液的pH值为10.7~11.3,回收一级脱硫吸收液;所述NaOH溶液Ⅰ中NaOH的质量含量为20%~22%,所述二级脱硫吸收液为由NaOH溶液Ⅰ在第二级脱硫吸收处理步骤中进行硫吸收后再循环喷淋进行硫吸收得到的混合溶液,所述一级脱硫吸收液为由二级脱硫吸收液在第一级脱硫吸收处理步骤中进行硫吸收后再循环喷淋进行硫吸收得到的混合溶液;
b、脱氨及氨回收处理步骤:
b1、脱氨处理步骤:向脱硫后的废水加入NaOH溶液Ⅱ,调节酸碱度后喷淋,与空气逆向接触进行空气吹脱脱氨处理,脱氨后的废水排放;所述脱氨后废水的pH值控制为10.5~11.5;所述NaOH溶液Ⅱ中NaOH的质量含量为20~30%;
b2、氨回收处理步骤:将经过所述脱氨处理步骤后逸出的气体经过两级脱氨吸收处理后排放,所述两级脱氨吸收处理包括由循环喷淋的一级脱氨吸收液对经过所述脱氨处理步骤后逸出的气体进行第一级脱氨吸收处理步骤,以及由循环喷淋的二级脱氨吸收液和补充喷淋的稀硫酸溶液Ⅱ对经过所述第一级脱氨吸收处理步骤后逸出的气体进行第二级脱氨吸收处理步骤;控制一级脱氨吸收液的pH值为4.5~6.5,回收一级脱氨吸收液;所述稀硫酸溶液Ⅱ中H2SO4的质量含量为30%,所述二级脱氨吸收液为由稀硫酸溶液Ⅱ在第二级脱氨吸收处理步骤中进行氨吸收后再循环喷淋进行氨吸收得到的混合溶液,所述一级脱氨吸收液为由二级脱氨吸收液在第一级脱氨吸收处理步骤中进行氨吸收后再循环喷淋进行氨吸收得到的混合溶液。
2.根据权利要求1所述的炼油加氢工艺产生的废水的脱硫脱氨处理方法,其特征在于:于所述步骤b2后设有将回收的一级脱氨吸收液依次进行蒸发浓缩、降温结晶和离心脱水的步骤,得到固体硫化铵产品。
3.根据权利要求1所述的炼油加氢工艺产生的废水的脱硫脱氨处理方法,其特征在于:步骤a1中,所述空气吹脱脱硫处理过程,空气与废水的气液比为(3000-5000):1,空气的空塔流速为1.0-2.0m/s。
4.根据权利要求1所述的炼油加氢工艺产生的废水的脱硫脱氨处理方法,其特征在于:步骤a2中,所述第一级脱硫吸收处理步骤,气体与一级脱硫吸收液的气液比为(30-100):1;所述第二级脱硫吸收处理步骤,气体与二级脱硫吸收液的气液比为(30-100):1。
5.根据权利要求1所述的炼油加氢工艺产生的废水的脱硫脱氨处理方法,其特征在于:步骤b1中,所述空气吹脱脱氨处理为两级空气吹脱脱氨处理,每级空气吹脱脱氨处理过程中,空气与废水的气液比均为(3000-5000):1,空气的空塔流速均为1.0-2.0m/s。
6.根据权利要求1所述的炼油加氢工艺产生的废水的脱硫脱氨处理方法,其特征在于:步骤b2中,所述第一级脱氨吸收处理过程,气体与一级脱氨吸收液的气液比为(30-100):1;所述第二级脱氨吸收处理过程,气体与二级脱氨吸收液的气液比为(30-100):1。
7.一种炼油加氢工艺产生的废水的脱硫脱氨处理装置,其特征在于:包括脱硫处理机构及连接于脱硫处理机构下游的脱氨处理机构;
所述脱硫处理机构包括第一管道混合器,在第一管道混合器上经由加酸计量泵连接有第一酸液罐,还包括连接于第一管道混合器下游的脱硫吹脱塔,所述脱硫吹脱塔的出液口连接脱氨处理机构,所述脱硫吹脱塔的出气口连接有硫回收单元,且所述硫回收单元包括相串接的均具有储液槽及经由循环泵与储液槽相连的喷淋头的第一硫尾气吸收塔和第二硫尾气吸收塔,第一硫尾气吸收塔及第二硫尾气吸收塔的储液槽相连通,在第二硫尾气吸收塔上设有经由加碱泵与第一碱液罐相连的碱液补充喷淋头,在第一硫尾气吸收塔的储液槽处连接有溢流口;
所述脱氨处理机构包括依次串接的第二管道混合器、第一脱氨吹脱塔、第三管道混合器及第二脱氨吹脱塔,在第二管道混合器和第三管道混合器上分别经由第一加碱计量泵和第二加碱计量泵连接有第二碱液罐,在第一脱氨吹脱塔及第二脱氨吹脱塔的出气口并联相接有氨回收单元,且所述氨回收单元包括相串接的均具有储液槽及经由循环泵与储液槽相连的喷淋头的第一氨尾气吸收塔和第二氨尾气吸收塔,第一氨尾气吸收塔及第二氨尾气吸收塔的储液槽相连通,在第二氨尾气吸收塔上设有经由加酸泵与第二酸液罐相连的酸液补充喷淋头,在第一氨尾气吸收塔的储液槽处连接有溢流口;
在所述脱硫吹脱塔的出液口设有第一PH检测仪,所述加酸计量泵控制联接于第一PH检测仪,在所述第一硫尾气吸收塔的溢流口设有第二PH检测仪,所述加碱泵控制联接于第二PH检测仪,在所述第一脱氨吹脱塔和第二脱氨吹脱塔的出液口分别设有第三PH检测仪和第四PH检测仪,所述第三PH检测仪与第一加碱计量泵控制联接,所述第四PH检测仪与第二加碱泵控制联接,在第一氨尾气吸收塔的溢流口连接有第五PH检测仪,所述加酸泵控制联接于第五PH检测仪。
8.根据权利要求7所述的炼油加氢工艺产生的废水的脱硫脱氨处理装置,其特征在于:在第一管道混合器的上游串接有均质罐。
9.根据权利要求7所述的炼油加氢工艺产生的废水的脱硫脱氨处理装置,其特征在于:在所述第一氨尾气吸收塔溢流口的下游连接有集液槽,以及经由输送泵依次串接于集液槽上的蒸发浓缩器、结晶器和离心机。
10.根据权利要求7所述的炼油加氢工艺产生的废水的脱硫脱氨处理装置,其特征在于:在第二硫尾气吸收塔中所述碱液补充喷淋头置于喷淋头之上;在第二氨尾气吸收塔中所述酸液补充喷淋头置于喷淋头之上。
说明书
炼油加氢工艺产生的废水的脱硫脱氨处理方法及处理装置
技术领域
本发明涉及一种废水脱硫脱氨技术领域,尤其涉及一种炼油加氢工艺产生的废水的脱硫脱氨处理方法,以及用于该处理方法的处理装置。
背景技术
因国内对车用燃料油、润滑油品质的提升,炼油厂在炼油工艺中增加了加氢工艺,以脱除燃料油、润滑油中含有的巯基(-SH)、氨基(-NH2)、硝基(-NO2)、醇、醛、酮等亲水基团,减少发动机在油品燃烧排放中的二氧化硫和氮氧化物含量,减少润滑油乳化的风险,提升油品品质。
对燃料油、润滑油加氢后,巯基(-SH)、氨基(-NH2)、硝基(-NO2)、醇、醛、酮等亲水基团转换成水、(NH4)2S和NH4NO3,与油品分离后形成水溶液,该水溶液中硫离子(S2-)浓度高达9000mg/L,氨氮(NH4-N)浓度高达15000mg/L,属于超高浓度含硫、含氨氮废水,必须要进行脱硫、脱氨氮处理。
发明内容
为解决现有技术中存在的不足,本发明提供了一种炼油加氢工艺产生的废水的脱硫脱氨处理方法,以脱除废水中高含量的硫和氨氮污染,使处理后废水中硫与氨氮含量达到GB8978-1996《污水综合排放标准》中的二级排放标准要求,并能回收硫获得硫化钠,回收氨氮获得硫酸铵。
为实现上述目的,本发明提供了一种炼油加氢工艺产生的废水的脱硫脱氨处理方法,包括以下步骤:
a、脱硫及硫回收处理步骤:
a1、脱硫处理步骤:向炼油加氢工艺产生的废水加入稀硫酸溶液Ⅰ,调节酸碱度后喷淋,与空气逆向接触进行空气吹脱脱硫处理,脱硫后的废水输送至脱氨处理步骤;所述脱硫后废水的pH值控制为0.8~1.2;所述稀硫酸溶液Ⅰ中H2SO4的质量含量为30%~50%;
a2、硫回收处理步骤:将经过所述脱硫处理步骤后逸出的气体经过两级脱硫吸收处理后排放,所述两级脱硫吸收处理包括由循环喷淋的一级脱硫吸收液对经过所述脱硫处理步骤后逸出的气体进行第一级脱硫吸收处理步骤,以及由循环喷淋的二级脱硫吸收液和补充喷淋的NaOH溶液Ⅰ对经过所述第一级脱硫吸收处理步骤后逸出的气体进行第二级脱硫吸收处理步骤;控制一级脱硫吸收液的pH值为10.7~11.3,回收一级脱硫吸收液;所述NaOH溶液Ⅰ中NaOH的质量含量为20%~22%,所述二级脱硫吸收液为由NaOH溶液Ⅰ在第二级脱硫吸收处理步骤中进行硫吸收后再循环喷淋进行硫吸收得到的混合溶液,所述一级脱硫吸收液为由二级脱硫吸收液在第一级脱硫吸收处理步骤中进行硫吸收后再循环喷淋进行硫吸收得到的混合溶液;
b、脱氨及氨回收处理步骤:
b1、脱氨处理步骤:向脱硫后的废水加入NaOH溶液Ⅱ,调节酸碱度后喷淋,与空气逆向接触进行空气吹脱脱氨处理,脱氨后的废水排放;所述脱氨后废水的pH值控制为10.5~11.5;所述NaOH溶液Ⅱ中NaOH的质量含量为20~30%;
b2、氨回收处理步骤:将经过所述脱氨处理步骤后逸出的气体经过两级脱氨吸收处理后排放,所述两级脱氨吸收处理包括由循环喷淋的一级脱氨吸收液对经过所述脱氨处理步骤后逸出的气体进行第一级脱氨吸收处理步骤,以及由循环喷淋的二级脱氨吸收液和补充喷淋的稀硫酸溶液Ⅱ对经过所述第一级脱氨吸收处理步骤后逸出的气体进行第二级脱氨吸收处理步骤;控制一级脱氨吸收液的pH值为4.5~6.5,回收一级脱氨吸收液;所述稀硫酸溶液Ⅱ中H2SO4的质量含量为30%,所述二级脱氨吸收液为由稀硫酸溶液Ⅱ在第二级脱氨吸收处理步骤中进行氨吸收后再循环喷淋进行氨吸收得到的混合溶液,所述一级脱氨吸收液为由二级脱氨吸收液在第一级脱氨吸收处理步骤中进行氨吸收后再循环喷淋进行氨吸收得到的混合溶液。
本发明的废水处理方法针对炼油加氢工艺产生的废水具有高含量硫、高含量氨氮的特性,采用依次进行脱硫及硫回收处理和脱氨及氨回收处理的方式,高效脱除废水中的硫和氨氮污染,使处理后废水中硫与氨氮含量达到GB8978-1996《污水综合排放标准》表4中的二级排放标准要求,并回收硫获得硫化钠,回收氨氮获得硫酸铵,使污染物转化成可利用的有价值的化工产品,实现绿色化工。
在处理方法中对废水先进行脱硫处理,通过向废水加入稀硫酸调节废水的酸碱度,一方面实现由空气吹扫废水进行的脱硫处理,并利用硫酸作为调节酸以避免空气吹脱过程除硫化氢污染物外的杂质污染物的逸出,以保证后续步骤的硫回收效果及空气处理效果;另一方面控制脱硫后废水的pH值,以保证废水的脱硫效果,使废水中硫含量低于1mg/L,达到GB8978-1996《污水综合排放标准》表4中的二级排放标准要求。废水中加入的稀硫酸量以脱硫后废水的pH值为标准进行调控,使脱硫后废水的pH值维持在0.8~1.2。脱除的硫污染物以硫化氢形式随空气进入到硫回收过程进行回收,依次经由一级脱硫吸收液对大部分硫化氢进行第一级循环喷淋吸收,形成以硫氢化钠为主的浓液循环,再经由二级脱硫吸收液和补充的NaOH溶液对剩余少量硫化氢进行第二级循环喷淋吸收,形成以硫化钠为主的贫液循环;所述NaOH溶液需以喷淋的方式补充,并通过控制一级脱硫吸收液的pH值维持在10.7~11.3范围,调控NaOH溶液的补充喷淋量,从而实现对脱除空气中硫化氢的彻底吸收,使经吸收处理后气体达到《恶臭污染物排放标准》(GB14554-93);另外,通过限定补充喷淋的NaOH溶液的质量含量(20%~22%)以及回收的一级脱硫吸收液的pH值范围(10.7~11.3),使回收的一级脱硫吸收液达到硫氢化钠的质量含量满足28%的标准,可直接用作化工产品使用,如可用于制革工业中生皮的脱毛及鞣革处理等。
经由上述脱硫处理后的废水再进行脱氨处理,通过向废水加入NaOH溶液调节废水的酸碱度,一方面实现由空气吹扫废水进行的脱氨处理,并利用NaOH作为调节碱以避免空气吹脱过程除氨气污染物外的杂质污染物的逸出,以保证后续步骤的氨回收效果及空气处理效果;另一方面控制脱氨后废水的pH值,以保证废水的脱氨效果,使废水中氨氮含量小于25mg/L,达到GB8978-1996《污水综合排放标准》表4中二级排放标准的要求。废水中加入的NaOH溶液量以脱氨后废水的pH值为标准进行调控,使脱氨后废水的pH值维持在10.5~11.5。脱除的氨氮污染物以氨气形式随空气进入到氨回收过程进行回收,依次经由一级脱氨吸收液对大部分氨气进行第一级循环喷淋吸收,形成以硫酸铵为主的循环吸收液,再经由二级脱氨吸收液和补充的稀硫酸溶液对剩余少量氨气进行第二级循环喷淋吸收,形成以硫酸氢铵为主的循环吸收液;并通过控制一级脱氨吸收液的pH值维持在4.5~6.5范围,调控稀硫酸溶液的补充喷淋量,从而实现对脱除空气中氨气的彻底吸收,使经吸收处理后气体达到《恶臭污染物排放标准》(GB14554-93)标准;另外,通过限定补充喷淋的稀硫酸溶液的质量含量(30%),以及回收的一级脱氨吸收液的pH值范围(4.5~6.5),使回收的一级脱氨吸收液达到硫酸铵浓度为40%即近饱和硫酸铵溶液,满足直接制备固体硫酸铵的标准,同时不会出现在吸收塔内析出晶体的问题。
本发明的处理方法,以pH值作为关键的调控因素,实现各处理环节的有机结合,进而完成对炼油加氢工艺产生高硫、高氨氮废水的高效脱硫、脱氨氮处理,并限定硫回收中补充喷淋的NaOH溶液的质量含量和氨回收中补充喷淋的稀硫酸溶液的质量含量,实现将脱除的硫、氨氮直接转化为可再利用的化工产品,在经济价值和环保方面均具有显著的效益。
作为对上述方式的进一步限定,于所述步骤b2后设有将回收的一级脱氨吸收液依次进行蒸发浓缩、降温结晶和离心脱水的步骤,得到固体硫化铵产品。
在处理方法中回收的一级脱氨吸收液只需进行蒸发浓缩、降温结晶和离心脱水处理,就能得到满足销售产品标准的固体硫化铵产品,而且回收的一级脱氨吸收液达到近饱和硫酸铵溶液,在蒸发浓缩过程可以极大的节约能源,具有较高的经济价值。
作为对上述方式的进一步限定,步骤a1中,所述空气吹脱脱硫处理过程,空气与废水的气液比为(3000-5000):1,空气的空塔流速为1.0-2.0m/s。
作为对上述方式的进一步限定,步骤a2中,所述第一级脱硫吸收处理步骤,气体与一级脱硫吸收液的气液比为(30-100):1;所述第二级脱硫吸收处理步骤,气体与二级脱硫吸收液的气液比为(30-100):1。
作为对上述方式的进一步限定,步骤b1中,所述空气吹脱脱氨处理为两级空气吹脱脱氨处理,每级空气吹脱脱氨处理过程中,空气与废水的气液比均为(3000-5000):1,空气的空塔流速均为1.0-2.0m/s。
作为对上述方式的进一步限定,步骤b2中,所述第一级脱氨吸收处理过程,气体与一级脱氨吸收液的气液比为(30-100):1;所述第二级脱氨吸收处理过程,气体与二级脱氨吸收液的气液比为(30-100):1。
进一步限定处理方法中空气吹脱脱硫处理过程的气液比、空塔流速,脱硫吸收处理过程的气液比,空气吹脱脱氨处理过程的气液比、空塔流速,脱氨吸收处理过程的气液比等操作参数,使脱硫及脱氨氮处理达到最佳运行过程,进而在处理效果及处理成本等方面达到俱佳。
同时,本发明还提供了炼油加氢工艺产生的废水的脱硫脱氨处理装置,包括脱硫处理机构及连接于脱硫处理机构下游的脱氨处理机构;
所述脱硫处理机构包括第一管道混合器,在第一管道混合器上经由加酸计量泵连接有第一酸液罐,还包括连接于第一管道混合器下游的脱硫吹脱塔,所述脱硫吹脱塔的出液口连接脱氨处理机构,所述脱硫吹脱塔的出气口连接有硫回收单元,且所述硫回收单元包括相串接的均具有储液槽及经由循环泵与储液槽相连的喷淋头的第一硫尾气吸收塔和第二硫尾气吸收塔,第一硫尾气吸收塔及第二硫尾气吸收塔的储液槽相连通,在第二硫尾气吸收塔上设有经由加碱泵与第一碱液罐相连的碱液补充喷淋头,在第一硫尾气吸收塔的储液槽处连接有溢流口;
所述脱氨处理机构包括依次串接的第二管道混合器、第一脱氨吹脱塔、第三管道混合器及第二脱氨吹脱塔,在第二管道混合器和第三管道混合器上分别经由第一加碱计量泵和第二加碱计量泵连接有第二碱液罐,在第一脱氨吹脱塔及第二脱氨吹脱塔的出气口并联相接有氨回收单元,且所述氨回收单元包括相串接的均具有储液槽及经由循环泵与储液槽相连的喷淋头的第一氨尾气吸收塔和第二氨尾气吸收塔,第一氨尾气吸收塔及第二氨尾气吸收塔的储液槽相连通,在第二氨尾气吸收塔上设有经由加酸泵与第二酸液罐相连的酸液补充喷淋头,在第一氨尾气吸收塔的储液槽处连接有溢流口;
在所述脱硫吹脱塔的出液口设有第一PH检测仪,所述加酸计量泵控制联接于第一PH检测仪,在所述第一硫尾气吸收塔的溢流口设有第二PH检测仪,所述加碱泵控制联接于第二PH检测仪,在所述第一脱氨吹脱塔和第二脱氨吹脱塔的出液口分别设有第三PH检测仪和第四PH检测仪,所述第三PH检测仪与第一加碱计量泵控制联接,所述第四PH检测仪与第二加碱泵控制联接,在第一氨尾气吸收塔的溢流口连接有第五PH检测仪,所述加酸泵控制联接于第五PH检测仪。
作为对上述方式的进一步限定,在第一管道混合器的上游串接有均质罐。
作为对上述方式的进一步限定,在所述第一氨尾气吸收塔溢流口的下游连接有集液槽,以及经由输送泵依次串接于集液槽上的蒸发浓缩器、结晶器和离心机。
作为对上述方式的进一步限定,在第二硫尾气吸收塔中所述碱液补充喷淋头置于喷淋头之上;在第二氨尾气吸收塔中所述酸液补充喷淋头置于喷淋头之上。
本发明提供的处理装置更利于上述处理方法的操作及运行控制,能够方便、高效地实现对废水的脱硫、脱氨氮处理,使处理后的废水满足GB8978-1996《污水综合排放标准》表4中的二级排放标准,更利于将脱除的硫、氨氮转化为可再利用的化工产品,实现回收。
综上所述,采用本发明的技术方案,获得的对炼油加氢工艺产生的废水的脱硫脱氨处理方法,采用对废水依次进行脱硫及硫回收处理和脱氨及氨回收处理的方式,以pH值作为关键的调控因素,实现各处理环节的有机结合,高效脱除废水中的硫和氨氮污染,使处理后废水中硫与氨氮含量达到GB8978-1996《污水综合排放标准》表4中的二级排放标准要求,并将脱除的硫、氨氮转化为可再利用的化工产品,在经济价值和环保方面均具有显著的效益,实现绿色化工。此外,本发明提供的处理装置,更利于上述处理方法的操作及运行控制,方便、高效地实现对废水的脱硫、脱氨氮处理及回收。