申请日2017.02.16
公开(公告)日2017.06.23
IPC分类号C02F9/04; C01C1/16; C02F1/26; C02F101/12
摘要
本发明是一种回收利用 废水 中氯离子的方法,涉及工业水处理、资源综合利用技术领域;本发明的工艺是含氯废水经预处理除去悬浮物后,送至萃取塔,以有机胺作为萃取剂,逆流萃取脱硫废水中氯离子,萃余液从萃取系统中排出,当萃余液中的氯离子含量未达到循环利用或排放标准,可回流萃取;萃取液进入反萃取塔,以含氨的氯化铵溶液进行逆流反萃取,反应生成氯化铵,经水洗塔分离、冷却结晶得到氯化铵产品,有机胺返回萃取塔回用,洗液范围水洗塔回用。
摘要附图
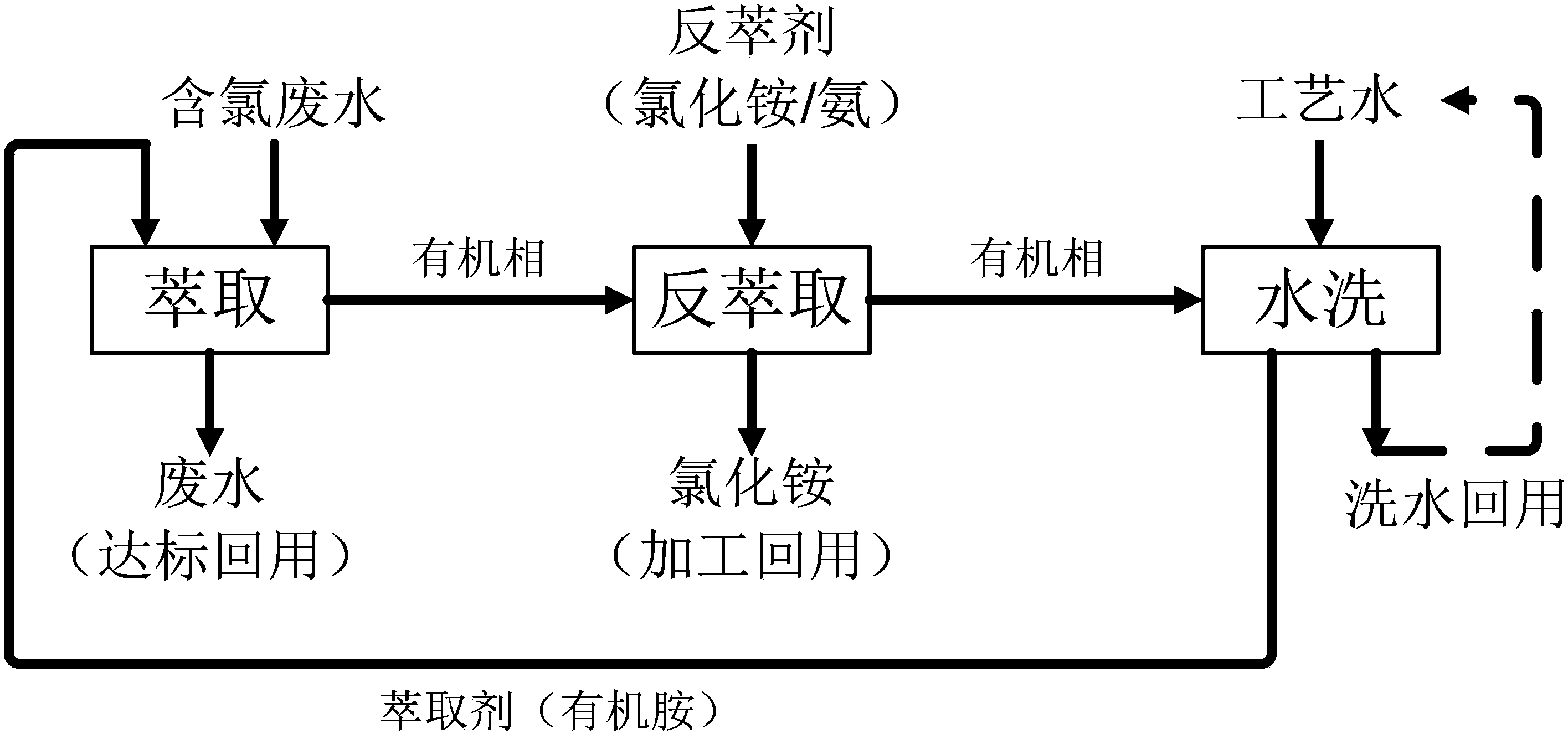
CN106882884A[中文]
权利要求书
1.一种回收利用废水中氯离子的方法,其特征在于:所述的方法包括如下工艺步骤:
步骤一:含氯废水的预处理,包括如下过程:废水缓冲池→中和箱→反应箱→絮凝箱→澄清浓缩池→清水箱,
所述缓冲池和中和箱中加入碱调节pH为8~10,
所述反应箱中加入质量分数0.5-1.5%TMT-15和0.5-1.5%混凝剂,
所述絮凝箱中加入0.08-0.12%助凝剂,所述清水箱中加入酸调节pH至6~6.8;
运行过程中废水流量控制在2~2.5m3/h,经过预处理后含氯废水的悬浮物(SS)低于70mg/L,pH值低于6.8,氯离子浓度为300~60000mg/kg;
步骤二:萃取废水中的氯离子,选用脉冲筛板塔作为萃取设备,脉冲频率0.5~5.0Hz,脉冲幅度0.5~25mm,有机胺为萃取剂,有机相与水相体积比为1:10~10:1,溶剂油为稀释剂,稀释剂中溶剂油与有机胺体积比为5%~300%,在4~90℃下萃取60s~480min;
步骤三:反萃取有机相中的氯离子:选用脉冲筛板塔作为反萃取设备,脉冲频率0.5~5.0Hz,脉冲幅度0.5~25mm,氨/氯化铵混合溶液为反萃取剂,氨水质量浓度为1%~25%,氯化铵溶液质量浓度为20%~40%,氨的过量系数为0.05~1.0,在4~90℃下,萃取60s~480min;
步骤四:有机相的再生:选用脉冲筛板塔作为有机相再生水洗设备,脉冲频率0.5~5.0Hz,脉冲幅度0.5~25mm,在4~90℃,水洗60s~480min;
步骤五:氯化铵的加工利用:反萃取后的氯化铵溶液经浓缩,配制反萃取剂用氯化铵溶液;或经结晶析出,生产农用氯化铵产品。
2.根据权利要求1所述的回收利用废水中氯离子的方法,其特征在于:所述的含氯废水源自化工、冶金、电力、化肥、电镀、皮革等行业含氯废水,氯离子浓度范围在1000~60000mg/kg之间。
3.根据权利要求1所述的回收利用废水中氯离子的方法,其特征在于:所述的缓冲池和中和箱中加入碱调节pH为9,
所述反应箱中加入质量分数1%TMT-15和1%混凝剂,
所述絮凝箱中加入0.1%助凝剂。
4.根据权利要求1所述的回收利用废水中氯离子的方法,其特征在于:所述的步骤二中的有机胺萃取剂包括乙胺、三乙醇胺、聚丙烯酰胺。
5.根据权利要求1所述的回收利用废水中氯离子的方法,其特征在于:所述的步骤二中的溶剂油稀释剂包括磺化煤油、橡胶溶剂油、油漆溶剂油。
说明书
一种回收利用废水中氯离子的方法
技术领域
本发明属工业水处理、资源综合利用技术领域,特别涉及氯碱化工、化工、冶金、电力、化肥、电镀、皮革等行业含氯废水的处理及氯资源的回收利用。
背景技术
目前,水资源危机已成为一个世界性难题,严重制约着人类社会的可持续发展,解决水资源危机刻不容缓,因此在各项水处理技术逐渐发展成熟的同时,人们逐渐认识到污水回用具有节水和环保的双重效益,通过污水回用解决水资源短缺问题已成为当前水资源可持续发展的必由之路。
随着各种污水处理技术的发展,工业废水的处理技术已日臻成熟,排放废水的水质已达到工业废水排放标准。然而,目前存在一个显著问题是某些工厂所排放的废水中国家规定的水质检测项目均达标,但废水中氯离子浓度太高,不仅导致废水难以回用,排放后造成水质恶化,水体自然生态平衡被破坏,甚至污染地下水和引用水源。
由于氯离子活性大,工业废水,特别是高浓度的含氯工业废水,如不加处理直接回用,氯化物会引起腐蚀龟裂和点腐蚀,影响金属管道的正常使用,缩短金属管道的使用周期。
含氯废水的处理和回用对解决目前工业上大量水资源的浪费起着举足轻重的作用,直接关系到该技术的大规模工业化应用的可行与否。
目前去除水中氯离子的方法主要有:阴离子交换树脂法、复合絮凝剂絮凝处理、反渗透膜技术、电渗析等处理技术,同时多种方法联用对氯离子的去除也有很好的效果通常工业废水的脱氯过程是通过添加亚硫酸盐来完成的,氯离子作为水中的盐分组分,通过运用工业废水降低盐度的方法来处理废水中的氯离子也是可行的。
201210591676.3“一种钯-铁颗粒催化脱氯处理含氯废水的方法”提出钯/铁颗粒在厌氧环境下,搅拌下催化脱除含氯有机废水中的氯(如2,4-二氯苯氧乙酸,简称2,4-D),实现溶液中游离的Fe2+(可能含Fe3+)快速去除,防止铁钝化层的形成,工艺简单,条件温和,铁和EDTA损耗小,对钯/铁颗粒还原脱氯效率提高显著,处理后钯/铁颗粒与水易分离。该方法以2,4-D的脱氯为研究对象,在钯/铁颗粒的催化还原作用下,反应生成苯氧乙酸,声明同样适用于其他含氯有机物的脱氯过程。因此,从反应机理的角度,该方法仅适用于含氯有机物的脱氯过程,对于无机盐氯化物中的氯离子的脱除是不适用的。
201210595467.6“一种去除污水中氯离子的方法”提出用聚合硫酸亚铁对含氯废水进行絮凝沉淀处理,在去除悬浮颗粒物的含氯废水中加入1~5ppt的硝酸汞试剂,调节pH值9.5~11.5,并充分搅拌10~30min,使之反应完全,再在500~1000mg/L废水中加入过量的硫酸钠和草酸钠,常压下继续浸出30~50min,使废水中剩余的微量汞离子得以沉淀去,最后废水流经盛有生物质滤料的吸附塔,进行吸附处理,出水既为完全去除氯离子的废水。该方法所用药剂成本低,投加量相对较小,操作简单,运行成本低,氯离子脱除率高,然而,处理氯离子过程中引入了重金属(汞),生物质滤料吸附氯离子后成为二次污染物,如焚烧或掺烧,存在潜在较大的设备安全风险与环境风险。
201420835128.5“一种离子交换除氯废水的脱氯装置”提出一种一种离子交换除氯废水的脱氯装置,包括反应器、吸收器、吸附器、蒸发结晶器、抽风机、自吸泵和余氯测定仪,能够实现从离子交换除氯废水中直接脱氯,同时不引入新的杂质,保证脱氯后液的质量,可会用于离子交换柱作解吸剂。该装置运用工业废水降低盐度的方法,降离子交换吸附、蒸发结晶联用,实现脱氯的目的,易于实现工业化。然而,蒸发结晶能耗高,运行成本高,蒸发结晶产生“三氯化铁”副产品纯度低,钠钾钙镁等杂质含量高,不能直接作为产品销售,多作为二次污染物填埋处置。
201520933376.8“一种废水处理系统”提出一种用于处理含氯离子废水的系统,包括脱氯单元,用于向含氯离子的废水中添加硫酸,并通过加热将废水中氯离子以盐酸气体的形式从废水中分离;脱硫单元,用于通过化学反应生成沉淀的方法将脱氯后废水中的硫酸根离子去除。该装置的脱氯单元,不仅实现了氯离子的脱除,还产生副产物盐酸;脱硫单元,不仅实现了硫酸根的脱除,还产生副产物硫酸钙。然而,从工业化的角度,原料成本远高于副产品价值,经济性差。脱氯单元加热将废水中氯离子以盐酸气体的形式从废水中分离,盐酸气体量小,不易直接液化,多采用洗水吸收,进而浓缩至合格浓度,整个过程设备材质要求高,设备基建成本及运行维护成本高。因此,该方法产业化前景差。
201511007842.0“一种脱硫浆液脱氯的方法”提出采取对脱硫石膏脱水过滤液与臭氧反应,释放出氯气,除氯的过滤液送回吸收塔,从而使浆液中氯含量降低。该方法以空气为原料,生产臭氧,以臭氧为脱氯反应的氧化剂,不消耗其他原料,通过鼓泡反应释放氯气,空气汽提,不用真空泵,有效降低了原料成本、设备基建与维护成本。虽说臭氧发生器已实现工业化,但系统中臭氧的逃逸、控制及小量氯气的回收利用技术不够成熟,近期难以应用于脱硫系统。
发明内容
本发明的目的在于提供一种回收利用废水中氯离子的方法,涉及工业水处理、资源综合利用技术领域。经预处理除去含氯废水中的悬浮物后,送至萃取塔,以有机胺作为萃取剂,逆流萃取脱硫废水中氯离子,萃余液从萃取系统中排出,当萃余液中的氯离子含量未达到循环利用或排放标准,可回流萃取;萃取液进入反萃取塔,以含氨的氯化铵溶液进行逆流反萃取,反应生成氯化铵,经水洗塔分离、冷却结晶得到氯化铵产品,有机胺返回萃取塔回用,洗液范围水洗塔回用。
包括如下工艺步骤:
步骤一、含氯废水的预处理:废水缓冲池→中和箱→反应箱→絮凝箱→澄清浓缩池→清水箱,其中缓冲池和中和箱中加入碱调节pH为9左右,反应箱中加入质量分数1%TMT-15(重金属捕集剂)和1%混凝剂,絮凝箱中加入0.1%助凝剂,清水箱中加入酸调节pH至6~6.8;运行过程中废水流量控制在2~2.5m3/h。悬浮物(SS)低于70mg/L(悬浮物会污染有机相,可能产生第三相,影响分配系数,且悬浮物过高也会影响萃取效果,因此须严格控制料液的悬浮物),pH值低于6.8(该工艺试验对象主要为酸性废水,直接进行萃取,会腐蚀设备,萃取效果差;调整成弱酸性,6.5~6.8,减少了设备腐蚀,萃取效果高;选择氨/氯化铵溶液作为反萃取剂,弱酸性条件有助于促进回收氯离子),氯离子浓度300~60000mg/kg(优选氯离子浓度1000~60000mg/kg);
步骤二、萃取废水中的氯离子:选用脉冲筛板塔(萃取是液液传质单元操作,筛板塔、脉冲筛板塔是萃取过程常见设备,轻重两相在塔内作逆流流动,而在每块塔板上成错流接触。在塔内分散相液体的分散和凝聚多次发生,筛板的存在又抑制了塔内的轴向返混,传质效率比较高。为改善两相接触状况,强化传质的过程,可在筛板塔内提供外加机械能以造成脉动,这种筛板塔称为脉冲筛板塔。脉动的产生,通常可由往复泵来完成,也可用压缩空气来实现。)作为萃取设备,脉冲频率0.5~5.0Hz,脉冲幅度0.5~25mm(脉动筛板塔的效率与脉动的振幅和频率有关。若脉动过分激烈,会导致严重的轴向混合,传质效率反而降低。实验选定的脉动频率为0.5~5.0Hz,脉冲幅度为0.5~25mm),有机胺(试验发现,有机胺类适用于液相中氯离子的萃取,对于高浓度含氯废水的萃取率高达90%以上;同时有机胺类萃取的氯离子,易于氨反应生成氯化铵,便于反萃取过程的进行)为萃取剂,物料配比(有机相与水相体积比)为1:10~10:1,溶剂油(在萃取过程中,存在有机相与水相两相,在试验过程中,有机胺作为有机相,若直接加入体系,有效浓度高,萃取效率降低,原料成本大幅增加,因此通常选用能相容、不参与反应、不抑制分配系数的溶剂作为稀释剂,溶剂油价格相对较低,是最常见的萃取稀释剂)为稀释剂,稀释剂的添加量(溶剂油与有机胺体积比)5%~300%,在4~90℃下(常温下可以萃取,适当提高温度可以提高萃取率,但考虑到后续工序——反萃取过程中选用氨/氯化铵作为反萃取剂,温度不宜过高,故选择90℃,通常40~50℃为最佳温度),萃取60s~480min;(对合格废水没有硬性指标,取决于废水排放单位/系统的技术指标,以脱硫废水为例,贵州某客户期望值为3000mg/kg以下;而对盐酸法白炭黑生产,内蒙某客户期望值为500mg/kg以下,试验过程中会依据废水特性、氯离子含量及技术指标,适当调整萃取工艺参数。)
步骤三、反萃取有机相中的氯离子:选用脉冲筛板塔作为反萃取设备,脉冲频率0.5~5.0Hz,脉冲幅度0.5~25mm,氨/氯化铵(选择氨/氯化铵混合溶液作为反萃取剂,是因为氯离子反萃取过程中,氨易于氯离子反应,是最适宜的反萃取剂,而反应产物是氯化铵,浓度控制合适不影响反萃取率,为了保障反萃取过程的长时间稳定运行,选择氨/氯化铵混合溶液作为反萃取剂)混合溶液为反萃取剂,氨水质量浓度为1%~25%,氯化铵溶液质量浓度为20%~40%,氨的过量系数为0.05~1.0(氨水易挥发,反萃取过程中考虑到氨逃逸或氨损,在适宜温度下,经物料衡算得氨损失率约1%~3%,为了反萃取过程的长时间稳定运行,选择氨的过量系数为0.05~1.0),在4~90℃下,萃取60s~480min;
步骤四、有机相的再生:选用脉冲筛板塔作为有机相再生水洗设备,脉冲频率0.5~5.0Hz,脉冲幅度0.5~25mm,在4~90℃,水洗60s~480min;
步骤五、氯化铵的加工利用:反萃取后的氯化铵溶液经浓缩,配制反萃取剂用氯化铵溶液;或经结晶析出,生产农用氯化铵产品。
优选地,所述的回收利用废水中氯离子的方法中所述的含氯废水源自化工、冶金、电力、化肥、电镀、皮革等行业含氯废水,氯离子浓度范围在1000~60000mg/kg之间。
优选地,所述的回收利用废水中氯离子的方法,其特征在于:所述的缓冲池和中和箱中加入碱调节pH为9,
所述反应箱中加入质量分数1%TMT-15和1%混凝剂,
所述絮凝箱中加入0.1%助凝剂。
优选地,所述的回收利用废水中氯离子的方法中的步骤二中的有机胺萃取剂包括乙胺、三乙醇胺、聚丙烯酰胺。
优选地,所述的回收利用废水中氯离子的方法中的步骤二中的溶剂油稀释剂包括磺化煤油、橡胶溶剂油、油漆溶剂油。
与现有技术相比,本发明的优点在于:
(1)以有机胺作为萃取剂,采用萃取法处理含氯废水,回收利用废水中氯离子,攻克了废水中氯离子含量高、循环利用困难等技术难题,增加含氯废水循环倍率,减少了废水排放量,有效推进水资源的高效利用。
(2)攻克了工业副产品(烟气脱硫石膏、盐酸法白炭黑等)中氯离子含量高、水洗(稀释)成本高、难以直接加工高附加值产品等技术难题,拓展了工业副产品高值化利用的应用领域。
(3)生产氯化铵产品,实现了含氯废水处理与煤炭伴生氯资源综合利用过程集成、多联产系统,是一项清洁生产、循环经济关键技术。
本发明以有机胺作为萃取剂,采用萃取法处理含氯废水,回收利用废水中氯离子,攻克了废水中氯离子含量高、循环利用困难、工业副产品(烟气脱硫石膏、盐酸法白炭黑等)中氯离子含量高、水洗(稀释)成本高、难以直接加工高附加值产品等技术难题,增加含氯废水循环倍率,减少了废水排放量,有效推进水资源的高效利用,拓展了工业副产品高值化利用的应用领域,生产氯化铵产品,实现了含氯废水处理与煤炭伴生氯资源综合利用过程集成、多联产系统,是一项清洁生产、循环经济关键技术。