申请日2017.02.09
公开(公告)日2017.05.31
IPC分类号C02F11/12; C02F11/10; C10B53/00; F23G7/14; B01D53/78; B01D53/56; B01D53/76; B01D53/50
摘要
一种含油污泥干燥焚烧一体化处理工艺,属于含油污泥处理技术领域。其特征在于:包括以下步骤:给料;干燥,高温烟气烘干单元采用风力干燥的方式对含油污泥进行反复烘干,烘干后的污泥集中收集;热解,分离出热解气,产生热解焦,将热解气排出进行冷凝并集中收集,将热解焦输送至焚烧单元;焚烧,对热解焦进行流化燃烧,采用多方位供风的方式,调节热解焦的燃烧温度,焚烧后的烟气排入烟气处理单元;烟气处理,对烟气进行脱硫脱硝。本发明的形成了集干燥、热解、焚烧、烟气处理结合循环利用于一体的一体化处理系统,实现了含油污泥减量化、资源化和污染物减排化综合利用。
摘要附图
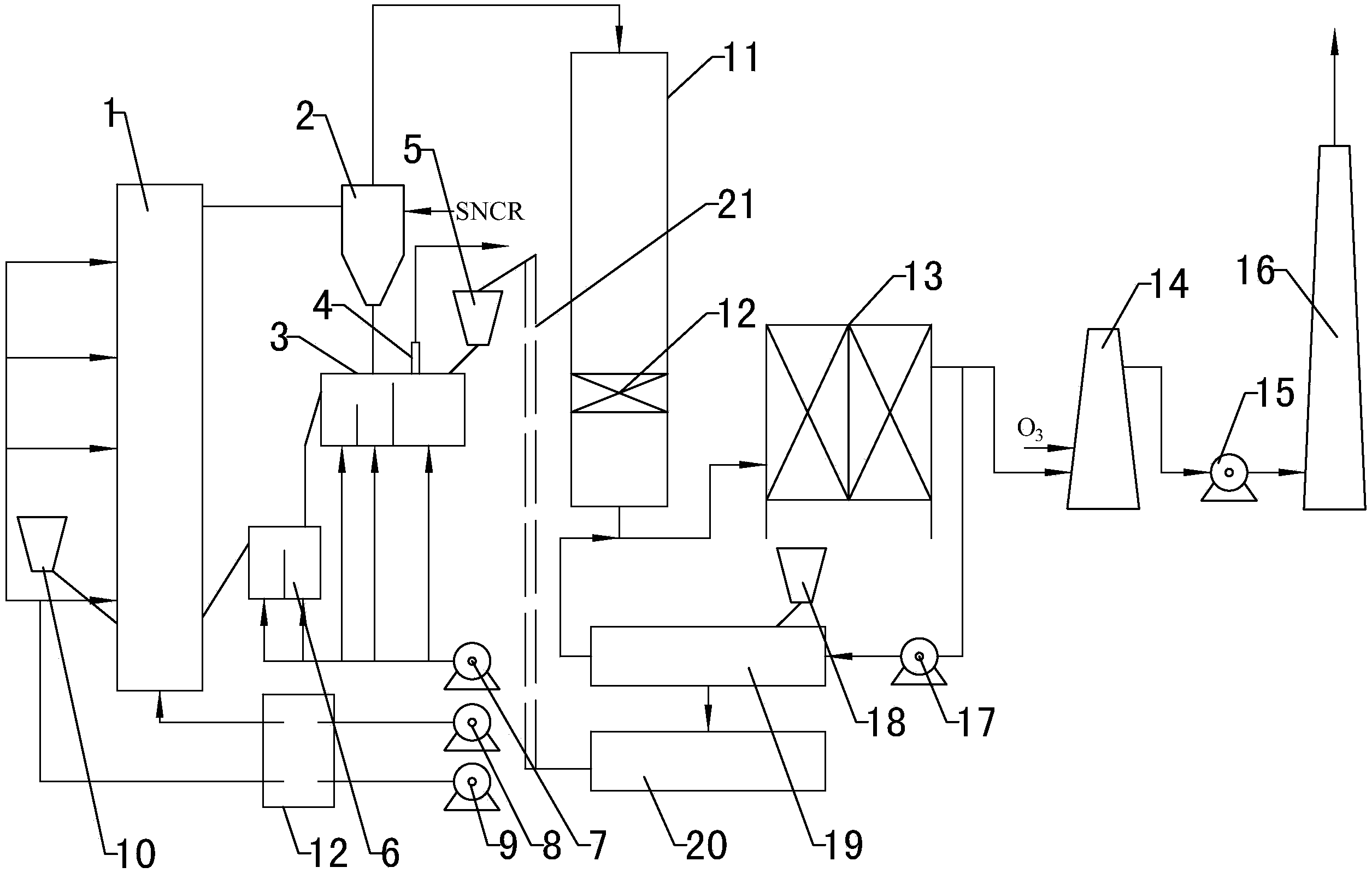
权利要求书
1.一种含油污泥干燥焚烧一体化处理工艺,其特征在于:包括以下步骤:
给料,将含油污泥输送给高温烟气烘干单元;
干燥,高温烟气烘干单元采用风力干燥的方式对含油污泥进行反复烘干,烘干后的污泥集中收集;
热解,将集中收集的烘干后的污泥输送至热解单元中,热解单元对干燥后的污泥进行热解,分离出热解气,产生热解焦,将热解气排出进行冷凝并集中收集,将热解焦输送至焚烧单元;
焚烧,对热解焦进行流化燃烧,采用多方位供风的方式,在热解焦的焚烧过程中供应一次风和二次风,调节热解焦的燃烧温度,焚烧后的烟气排入烟气处理单元;
烟气处理,在烟气处理单元中对携带焚烧颗粒的烟气进行氧化反应,对烟气进行脱硫脱硝;
其中,在干燥步骤中采用的风力为烟气处理单元处理后的烟气,收集烟气处理单元处理后的烟气作为高温烟气烘干单元的供风源,并且回收高温烟气烘干单元中的烟气循环使用。
2.根据权利要求1所述的一种含油污泥干燥焚烧一体化处理工艺,其特征在于:在利用所述的高温烟气烘干单元进行干燥之前,先对焚烧单元进行预热,达到预热温度后,加入燃料,提高焚烧温度,直至达到循环烘干用温度,启动烟气处理单元与高温烟气烘干单元之间的循环连接,将焚烧单元燃烧后产生的高温烟气经过烟气处理单元脱硫脱硝之后排入高温烟气烘干单元中作为烘干用循环风。
3.根据权利要求2所述的一种含油污泥干燥焚烧一体化处理工艺,其特征在于:所述的焚烧单元的预热温度为500℃,焚烧单元内的温度高于500℃时,加入燃料,所述的循环烘干用温度为800℃。
4.根据权利要求1所述的一种含油污泥干燥焚烧一体化处理工艺,其特征在于:所述的热解单元包括上返料器、热解器和下返料器(6)及高压流化风机(7),上返料器通过下返料器(6)连接焚烧单元,高压流化风机(7)分别连接上返料器和下返料器(6)的供风进气口,热解气出口(4)通过管路连接冷凝收集器;含油污泥进入焚烧单元之前,通过高压流化风机(7)先向上返料器输送松动风,而后向下返料器(6)输送流化风,然后通过下返料器(6)使循环灰返回焚烧单元内进行焚烧。
5.根据权利要求1所述的一种含油污泥干燥焚烧一体化处理工艺,其特征在于:所述的焚烧单元采用循环流化床锅炉(1),循环流化床锅炉(1)炉膛一侧设有辅助燃料给料机(10),炉膛的下部及一侧分别连接多方位供风装置,多方位供风装置包括一次风机(8)和二次风机(9),一次风机(8)连通循环流化床锅炉(1)炉膛下部,二次风机(9)设有多层出风口分别纵向设置在循环流化床锅炉(1)炉膛侧面。
6.根据权利要求1所述的一种含油污泥干燥焚烧一体化处理工艺,其特征在于:所述的循环风建立起来后,启动焚烧单元纵向设置的四层二次风,当热解单元温度到达600℃以上时,将干燥后的含油污泥通过输送装置送到热解单元中。
7.根据权利要求1所述的一种含油污泥干燥焚烧一体化处理工艺,其特征在于:所述的焚烧单元在焚烧热解焦时的燃烧温度保持在900~1000℃,气体表观线速度为3.5~5.0米/秒,焚烧单元内稀相区过量空气系数维持在1.1~1.2。
8.根据权利要求1所述的一种含油污泥干燥焚烧一体化处理工艺,其特征在于:所述的烟气处理单元为脱硫脱硝系统,包括旋风分离器(2)、烟道(11)、除尘器(13)和脱硫塔(14),旋风分离器(2)的烟气出口通过烟道(11)连接除尘器(13),除尘器(13)的出气口连接脱硫塔(14),脱硫塔(14)的出气口通过引风机(15)连接烟囱(16)。
9.根据权利要求8所述的一种含油污泥干燥焚烧一体化处理工艺,其特征在于:所述的旋风分离器(2)一侧设有脱硝剂喷枪,脱硝剂为氨水或尿素溶液;脱硫塔(14)内布置高压臭氧喷口。
10.根据权利要求8所述的一种含油污泥干燥焚烧一体化处理工艺,其特征在于:烟气循环管路包括连接在烟道(11)出气口与高温烟气烘干单元出气口之间的循环风送风管,及连接在除尘器(13)出气口与高温烟气烘干单元进气口之间的循环风回风管,循环风回风管上设有循环风机(17),所述烟道(11)内设有空气预热器(12)。
说明书
一种含油污泥干燥焚烧一体化处理工艺
技术领域
一种含油污泥干燥焚烧一体化处理工艺,属于含油污泥处理技术领域。
背景技术
石油作为一种化学能源,石油在开采、运输、储存和加工等过程中会产生大量的废渣、废水和废气,造成了严重的环境污染。含油污泥是石油及石油化工工业中常见的具有回收价值的危险废弃物,主要由水、石油烃类和固体泥沙等混合而成。根据成因不同,含油污泥主要可以分为:落地含油污泥、罐底含油污泥、地面溢油、炼厂含油污泥等。含油污泥中含有大量老化的原油、蜡质、沥青质,同时还含有苯系物、酚类、蒽类等毒性物质,若不经处理直接排放,会对土壤、水体、大气和植被造成严重污染。
我国对含油污泥的研究开始较晚,含油污泥处理技术与国外差距较大,目前还没有一套成熟、有效的处理含油污泥的技术,大部分油田和石油相关产业通过简单的露天堆放和填埋处理含油污泥,这样不仅浪费了资源,并且对当地环境造成了较大污染。目前含油污泥处理工艺主要有物理化学处理技术、无害化处理技术、生物降解技术、热处置技术、新型处理技术等。其中,热处置技术中的焚烧法具有工艺简单、占地面积小、处理周期短、处理彻底等优势,因而得到比较广泛的应用。
含油污泥成分复杂、危害严重,但是回收利用价值高,对含油污泥进行资源化利用具有良好的环境价值和较高的经济收益。随着环保法规的进一步完善,含油污泥的减量化、无害化、资掘化、清洁化技术将成为其发展的必然趋势。
发明内容
本发明所要解决的技术问题是:克服现有技术的不足,提供一种实现含油污泥减量化、资源化和污染物减排化综合利用的。
本发明解决其技术问题采用的技术方案是:该含油污泥干燥焚烧一体化处理工艺,其特征在于:包括以下步骤:
给料,将含油污泥输送给高温烟气烘干单元;
干燥,高温烟气烘干单元采用风力干燥的方式对含油污泥进行反复烘干,烘干后的污泥集中收集;
热解,将集中收集的烘干后的污泥输送至热解单元中,热解单元对干燥后的污泥进行热解,分离出热解气,产生热解焦,将热解气排出进行冷凝并集中收集,将热解焦输送至焚烧单元;
焚烧,对热解焦进行流化燃烧,采用多方位供风的方式,在热解焦的焚烧过程中供应一次风和二次风,调节热解焦的燃烧温度,焚烧后的烟气排入烟气处理单元;
烟气处理,在烟气处理单元中对携带焚烧颗粒的烟气进行氧化反应,对烟气进行脱硫脱硝;
其中,在干燥步骤中采用的风力为烟气处理单元处理后的烟气,收集烟气处理单元处理后的烟气作为高温烟气烘干单元的供风源,并且回收高温烟气烘干单元中的烟气循环使用。
本发明的处理工艺包括含油污泥干燥、热解、焚烧及烟气处理等多个步骤,含油污泥干燥装置利用高温烟气对含水量在60~80%的含油污泥进行干燥,利用焚烧系统将可燃物质燃烧,而且高温烟气烘干单元的高温进气口和出气口分别通过烟气循环管路连接烟气处理单元的出气端和进气端,使得经过处理之后的高温烟气又回到干燥系统中用于高温烘干,使得整个系统的高温烟气处于循环利用的状态;高温烟气从烟气处理单元引出,进入含油污泥干燥单元,干燥后的废气通入烟气处理单元再次经过处理,可以降低烟气处理单元入口的烟气温度,保证烟气处理单元的安全稳定运行。形成了集干燥、热解、焚烧、烟气处理结合循环利用于一体的一体化处理系统,实现了含油污泥减量化、资源化和污染物减排化综合利用。
在利用所述的高温烟气烘干单元进行干燥之前,先对焚烧单元进行预热,达到预热温度后,加入燃料,提高焚烧温度,直至达到循环烘干用温度,启动烟气处理单元与高温烟气烘干单元之间的循环连接,将焚烧单元燃烧后产生的高温烟气经过烟气处理单元脱硫脱硝之后排入高温烟气烘干单元中作为烘干用循环风。
所述的焚烧单元的预热温度为500℃,焚烧单元内的温度高于500℃时,加入燃料,所述的循环烘干用温度为800℃。
所述的热解单元包括上返料器、热解器和下返料器及高压流化风机,上返料器通过下返料器连接焚烧单元,高压流化风机分别连接上返料器和下返料器的供风进气口,热解气出口通过管路连接冷凝收集器;含油污泥进入焚烧单元之前,通过高压流化风机先向上返料器输送松动风,而后向下返料器输送流化风,然后通过下返料器使循环灰返回焚烧单元内进行焚烧。
上返料热解混合装置既可以完成热解工作,也可以将热解后的含油污泥焦通过高压流化风送入返料器内返回炉膛焚烧;上返料器和热解器之间有挡板隔开,热解后的热解气通过热解气出口经保温管道送入储罐冷凝,收集油品,由于热解过程不掺杂循环灰,能够保证油品不受污染。
所述的焚烧单元采用循环流化床锅炉,循环流化床锅炉炉膛一侧设有辅助燃料给料机,炉膛的下部及一侧分别连接多方位供风装置,多方位供风装置包括一次风机和二次风机,一次风机连通循环流化床锅炉炉膛下部,二次风机设有多层出风口分别纵向设置在循环流化床锅炉炉膛侧面。
优选的,一次风机和二次风机供风为空气,一次风、二次风经过空气预热器预热后进入炉膛。二次风沿炉膛高度纵向布置了四层,通过高层二次风布置实现空气分级燃烧,从而降低燃料燃烧过程中氮氧化物排放量。
所述的循环风建立起来后,启动焚烧单元纵向设置的四层二次风,当热解单元温度到达600℃以上时,将干燥后的含油污泥通过输送装置送到热解单元中。
所述的焚烧单元在焚烧热解焦时的燃烧温度保持在900~1000℃,气体表观线速度为3.5~5.0米/秒,焚烧单元内稀相区过量空气系数维持在1.1~1.2。
所述的烟气处理单元为脱硫脱硝系统,包括旋风分离器、烟道、除尘器和脱硫塔,旋风分离器的烟气出口通过烟道连接除尘器,除尘器的出气口连接脱硫塔,脱硫塔的出气口通过引风机连接烟囱。
通过脱硝剂喷枪喷入氨水或尿素溶液与烟气中的氮氧化物反应,之后,烟气进入尾部烟道、经过布袋除尘器进入脱硫塔,脱硫塔内布置高压臭氧喷口,尾部烟道脱硫塔内补入臭氧,将贡单质氧化为二价贡,实现重金属、硫协同脱除在脱硫的同时将贡协同脱除,最后烟气经引风机引入烟囱排到大气中。
所述的旋风分离器一侧设有脱硝剂喷枪,脱硝剂为氨水或尿素溶液;脱硫塔内布置高压臭氧喷口。
烟气循环管路包括连接在烟道出气口与高温烟气烘干单元出气口之间的循环风送风管,及连接在除尘器出气口与高温烟气烘干单元进气口之间的循环风回风管,循环风回风管上设有循环风机,所述烟道内设有空气预热器。
与现有技术相比,本发明所具有的有益效果是:本发明的处理工艺包括含油污泥收集、干燥、热解、焚烧及烟气处理等步骤,高温烟气烘干单元利用高温烟气对含水量在60~80%的含油污泥进行干燥,利用焚烧系统将可燃物质燃烧,而且高温烟气烘干单元的高温进气口和出气口分别通过烟气循环管路连接烟气处理单元的出气端和进气端,使得经过处理之后的高温烟气又回到干燥系统中用于高温烘干,使得整个系统的高温烟气处于循环利用的状态;高温烟气从烟气处理单元引出,进入含油污泥干燥单元,干燥后的废气通入烟气处理单元再次经过处理,可以降低烟气处理单元入口的烟气温度,保证烟气处理单元的安全稳定运行。形成了集干燥、热解、焚烧、烟气处理结合循环利用于一体的一体化处理系统,实现了含油污泥减量化、资源化和污染物减排化综合利用。